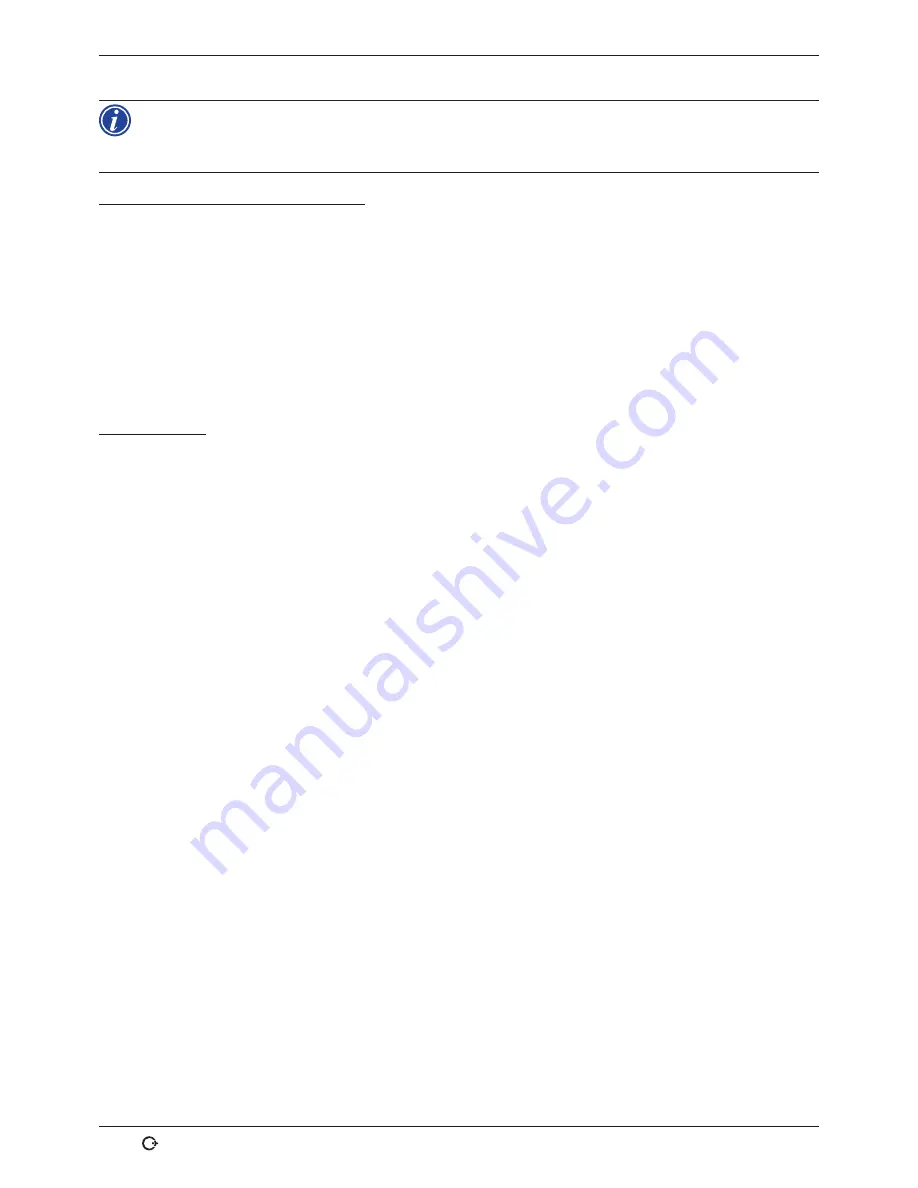
Operation
ORBIMAT 180 SW
| Operating instructions
48
orbitalum tools
GmbH, D-78224 Singen, www.orbitalum.com, Phone +49 (0) 77 31 792-0
(17.09.18) OW_ORBIMAT_180SW_BA_850060202_00_EN
Initial password at the initial login:
12345
The password can be changed at any time under the menu item "
System settings
".
If the password is lost/forgotten, please use the machine-specific master password specified in the
calibration certificate. If logging in with the master password is not possible, please contact Orbitalum.
Limitation of the percentage current change
In the "disabled" position, the operator can not adjust or delete existing procedure sequences.
If it is necessary, however, to make small adjustments for a welding task (e.g. due to batch-based fluctuations of the
material composition or minor changes in the wall thickness), a percentage limit can be set in the welding procedure.
The operator can adjust the current within this limit.
This adjustment is not saved in the procedure and affects all sectors and the high-pulse and low-pulse current.
X
Recommendation:
Allow for maximum 10% (20% adjustment range).
Specifying "5%" means that it is possible to adjust up to 5% above or below the base value. The total adjustment range
amounts to 10%.
Specifying a limit
1. Locking the machine with a login
The main menu "Long form" appears in the display.
2. In the main menu, select "
System settings
" > "
Program settings
".
3. Select and highlight the "
Scale weld limit
" field and enter a percentage value.
– or –
If no adjustment is desired: Enter the value "0".
4. Save the procedure.
5. Lock the machine with a login.
8.6
Tacking function
1. Select the basic adjustments.
2. Use the rotary knob to select the "Advanced" option and confirm by pressing.
3. Select the "On" option for "Tacking".
The following four fields are activated:
4. Accept or adjust the suggested parameters.
5. Test the tacking function: Carry out welding on a test pipe.
6. Interrupt the test weld with "
STOP
" after the tacking phase.
7. Remove the test pipe from the weld head and assess the tacking.
8. Adjust the parameters manually if necessary.
Tack points
Number of tack points on the pipe. The system calculates the optimum position of the points from the specified number
of points and moves to them during the tacking procedure: With four tack points, the two opposite tack points (0° and
180°) come first, followed by the other points (90° and 270°).
Tack current
Presetting: High-pulse current from level 1.
During the tacking procedure, this current is switched on after the position for the respective tack point (with rotor not
moving) is reached. If the time specified under "
Tack time
" has past, the system switches to a low current (the "
Pilot
current
") and moves to the next tack point at the maximum possible speed.