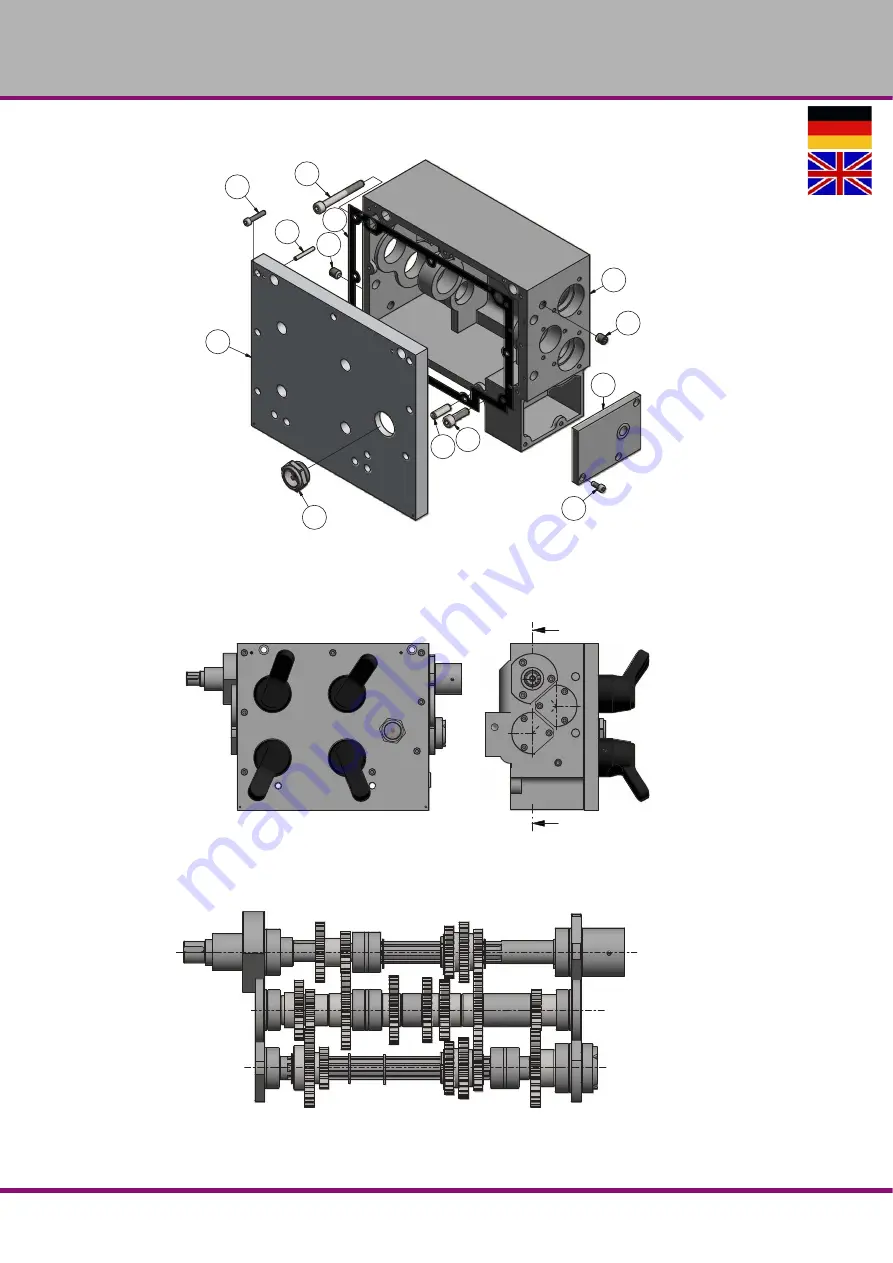
OPTIMUM
M A S C H I N E N - G E R M A N Y
Version 1.0.1 2018-1-31
80
Originalbetriebsanleitung
TM4010 | TM4010D
DE | GB
T
M
4010_
T
M
4010D_p
art
s.
fm
7.12
Vorschubgetriebe 1-6 - Feed gear 1-6
7-9: Vorschubgetriebe 1-6 - Feed gear 1-6
7.13
Vorschubgetriebe 2-6 - Feed gear 2-6
7-10: Vorschubgetriebe 2-6 - Feed gear 2-6
13
72
71
59
60
28
17
13
102
104
95
85
101
A
B
C
D
E
F
G
A
A
A-A