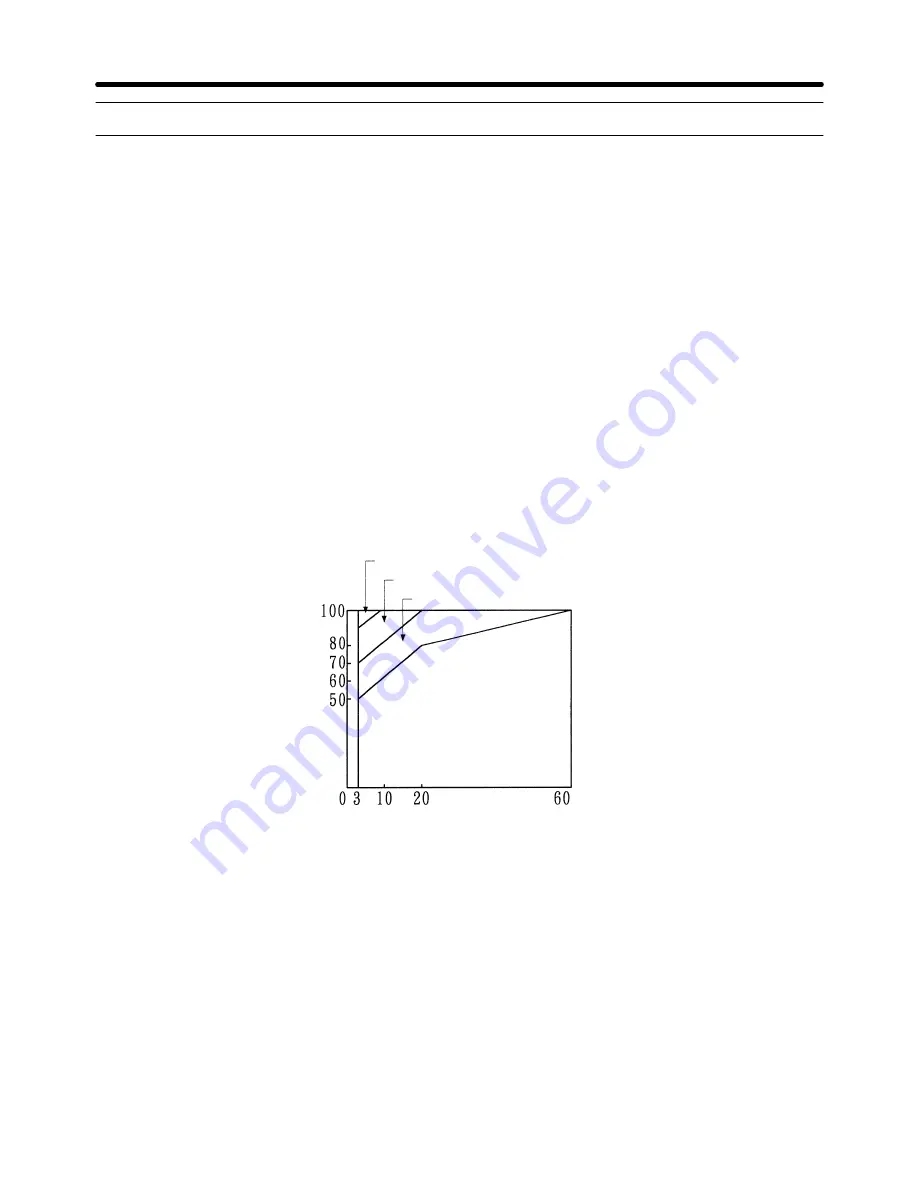
7-2
7-1
Notes on Using Inverter for Motor
H
Using Inverter for Existing Standard Motor
When a standard motor is operated with this Inverter, a power loss is slightly higher than
when operated with a commercial power supply.
In addition, cooling effects also decline in the low-speed range, resulting in an increase
in the motor temperature. Therefore, motor torque should be reduced in the low speed
range.
The figure on the right-hand side shows allowable load characteristics of a standard
motor.
If 100% torque is continuously required in the low-speed range, use a special motor for
use with Inverters.
Allowable Load Characteristics of Standard Motor
25% ED (or 15 minutes)
40% ED (or 20 minutes)
60% ED (or 40 minutes)
Continuous
Frequency (Hz)
T
orque (%)
D
High-speed Operation
When using the motor at a high speed (60 Hz or more), note that problems may arise in
dynamic balance, bearing durability, and so on.
D
Torque Characteristics
When the motor is operated with the Inverter, torque characteristics differ from when
operated with a commercial power supply. Check the load torque characteristics of the
machine to be used with the motor.
Appendix A
Chapter 7
Summary of Contents for SYSDRIVE 3G3EV SERIES
Page 1: ...USER S MANUAL SYSDRIVE 3G3EV Standard Models Compact Low noise Inverter Cat No I011 E1 3...
Page 5: ...Chapter 1 Getting Started 1 1 Items to be Checked when Unpacking 1 2 Precautions 1...
Page 9: ...Chapter 2 Overview 2 1 Features 2 2 Component Names 2...
Page 14: ...Chapter 3 Design 3 1 Installation 3 2 Wiring 3...
Page 72: ...Chapter 6 Specifications 6 1 Specifications of Main Unit 6...