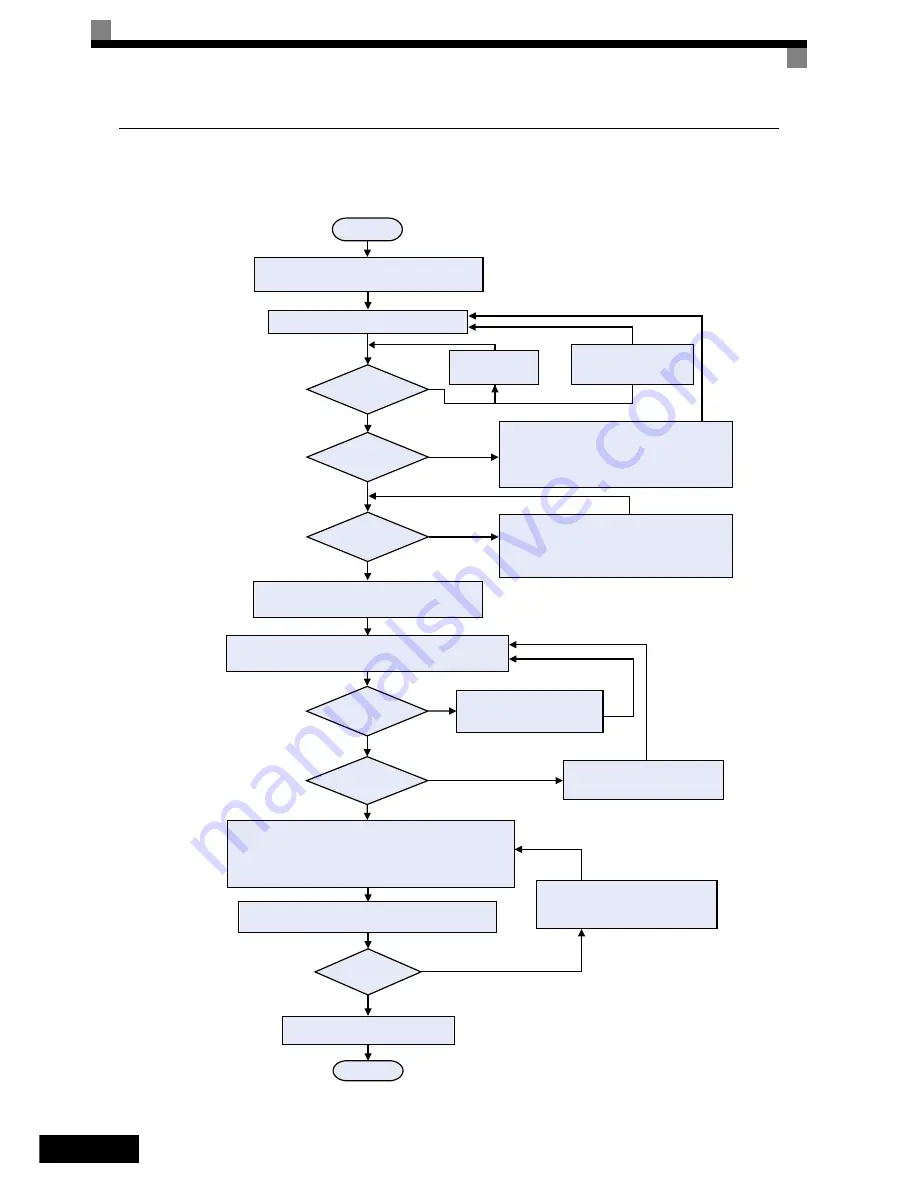
EN-17
Autotuning Procedure for PM Motors
Fig 7
shows the autotuning procedure for permanent magnet motors. Before tuning make sure that the control
mode is set to PM Closed Loop Vector (A1-02 = 6).
Fig 7 Autotuning for Permanent Magnet Motors
T2-04 - Motor rated current
T2-05 - Motor pole number
T2-09 - Encoder resolution
T2-10 - Motor voltage constant
START
* Remove the ropes so that the motor can rotate freely
* Set the Base Block inputs BB and BB1
T1-01 = 0 - Rotational Tuning
T2-01 - Motor rated power
T2-02 - Motor base frequency
T2-03 - Motor rated voltage
Press the UP button until the “Tuning Ready” display appears
Set the autotuning parameters:
Set mechanical constants:
S3-13 - Traction sheave diameter
S3-14 - Roping
S3-15 - Gear ratio
Close the motor contactor(s) and press the RUN button
Wait until tuning is finsihed
Tuning successful?
Yes
(”Tuning successful” is displayed)
No
(Fault code is displayed)
Open the contactors, open the baseblock
inputs and close the brake
FINISH
Refer to
and eliminate the fault source
Does a CPF24 fault
occur?
Switch ON the power supply if it is OFF
* Check parameter n8-35
* If EnDat / Hiperface is used
- check the encoder power supply
- check the CLOCK and DATA signal wiring
* Switch off the power supply.
No
Yes
Does a OPE06 fault
occur?
Check parameter
* F1-01
* n8-35
Switch off the power supply
and check if the right PG card
is correctley installed
Yes
No
Does a OPE02 fault
occur?
* Check if the correct PG constant (F1-01) and
absolute encoder resolution (F1-21) has been set.
* Refer to:
and eliminate the fault source
No
Yes
* Check the wiring
* Check/readjust the encoder
power supply
* Check the encoder wiring
* Change parameter F1-05
Does PGO (no
encoder feedback)
occur?
Is the sign of the
U1-05 value positive
(not -)?
No
Yes
No
Yes
Open the brake, close the motor contactor,
turn the motor slowly in Forward direction*
1
and check monitor U1-05.
page 27, Auto-tuning Faults
page 26, Operator Programming Errors (OPE)
* 1. Forward direction means:
The direction the motor turns with an UP command at terminal S1 (i.e.
with a clockwise rotating 3 phase supply and U-U, V-V, W-W wiring
between inverter and motor). Usually the direction is clockwise seen
from the motor shaft (traction sheave) side.
Refer to the motor instruction manual or consult the manufacturer for
details about the rotation direction.