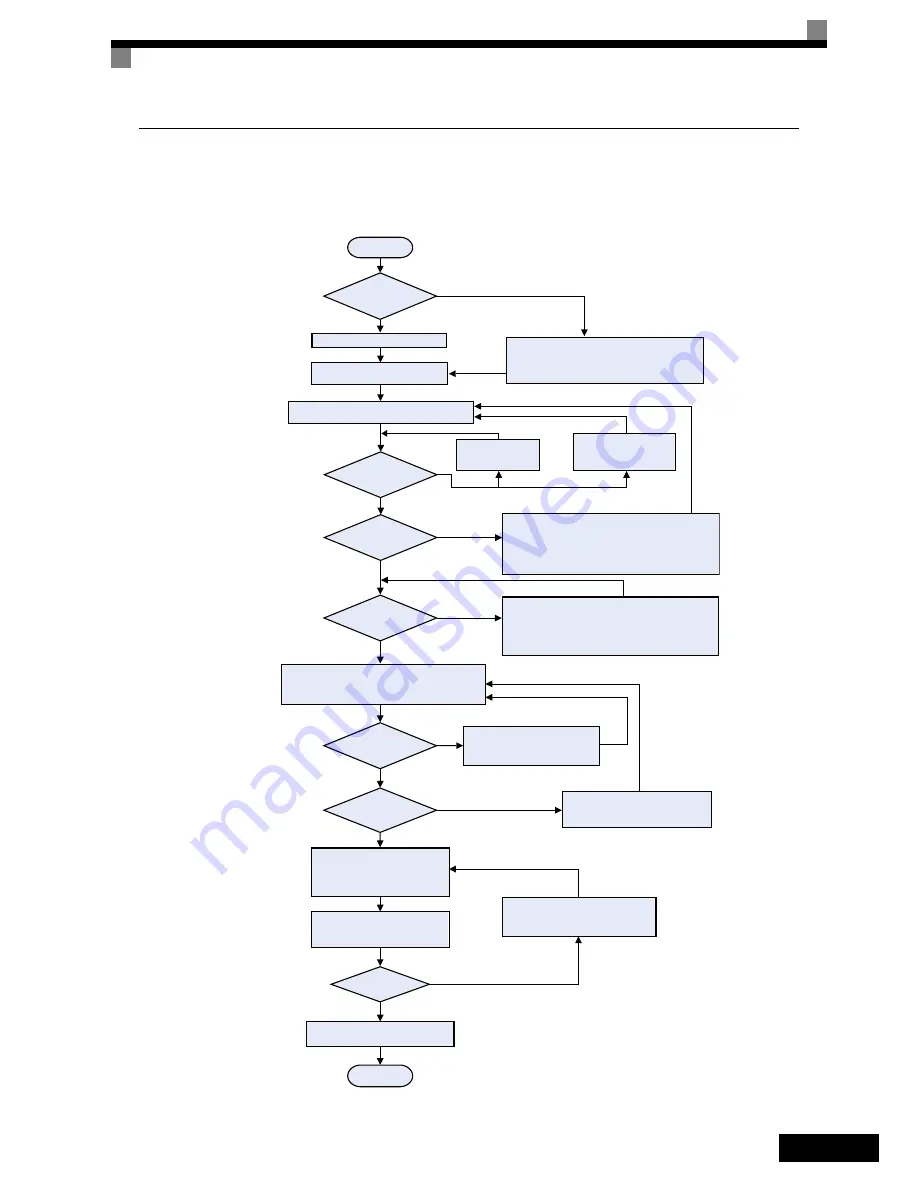
EN-18
PM Motor Encoder Offset Tuning
Fig 8
shows the autotuning procedure for an encoder offset tuning. The procedure should be performed if the
encoder has been changed or has not been aligned correctly. Before tuning make sure that PM losed loop vec-
tor control is selected (A1-02 = 6) and that the E1-
and E5-
parameters are set up correctly.
Fig 8 Encoder Offset Autotuning
* Check the wiring
* Check/readjust the encoder
power supply
Yes
* Check the encoder wiring
* Change parameter F1-05
START
Remove the ropes.
Does PGO (no
encoder feedback)
occur?
Set the Base Block inputs BB and BB1
Open the brake, close the motor contactor,
turn the motor slowly in Forward direction*
1
and check
monitor U1-05.
Is the sign of the
U1-05 value positive
(not -)?
No
Yes
No
Yes
Set:
T1-01 = 4 - Encoder Offset Tuning
Press the UP button until the “Tuning
Ready” display appears.
Close the motor contactor(s) and
press the RUN key.
Wait until the tuning is finished.
Tuning successful?
No
(Fault code is
displayed)
Yes
(”Tuning successful”
display is shown)
Refer to
and eliminate the fault source.
Open the contactors, open the base
block inputs and close the brake
FINISH
Is it possible to remove
the ropes ?
Does a CPF24 fault
occur?
Balance the car so that it does not move
with open brakes.
Note: The tuning accuracy will be lower
in this tuning mode
* Check parameter n8-35
* If EnDat / Hiperface is used
- check the encoder power supply
- check the CLOCK and DATA signal wiring
* Switch off the power supply.
No
No
Yes
Does a OPE06 fault
occur?
Check parameter
* F1-01
* n8-35
Switch off the power supply
and check if PG card is
correctly installed
Yes
No
Does a OPE02 fault
occur?
* Check if the correct PG constant (F1-01) and
absolute encoder resolution (F1-21) has been set.
* Refer to:
and eliminate the fault source
No
Yes
Switch ON the power supply if it is OFF
page 27, Auto-tuning Faults
page 26, Operator Programming Errors (OPE)
* 1. Forward direction means:
The direction the motor turns with an UP command at terminal S1 (i.e.
with a clockwise rotating 3 phase supply and U-U, V-V, W-W wiring
between inverter and motor). Usually the direction is clockwise seen
from the motor shaft (traction sheave) side.
Refer to the motor instruction manual or consult the manufacturer for
details about the rotation direction.