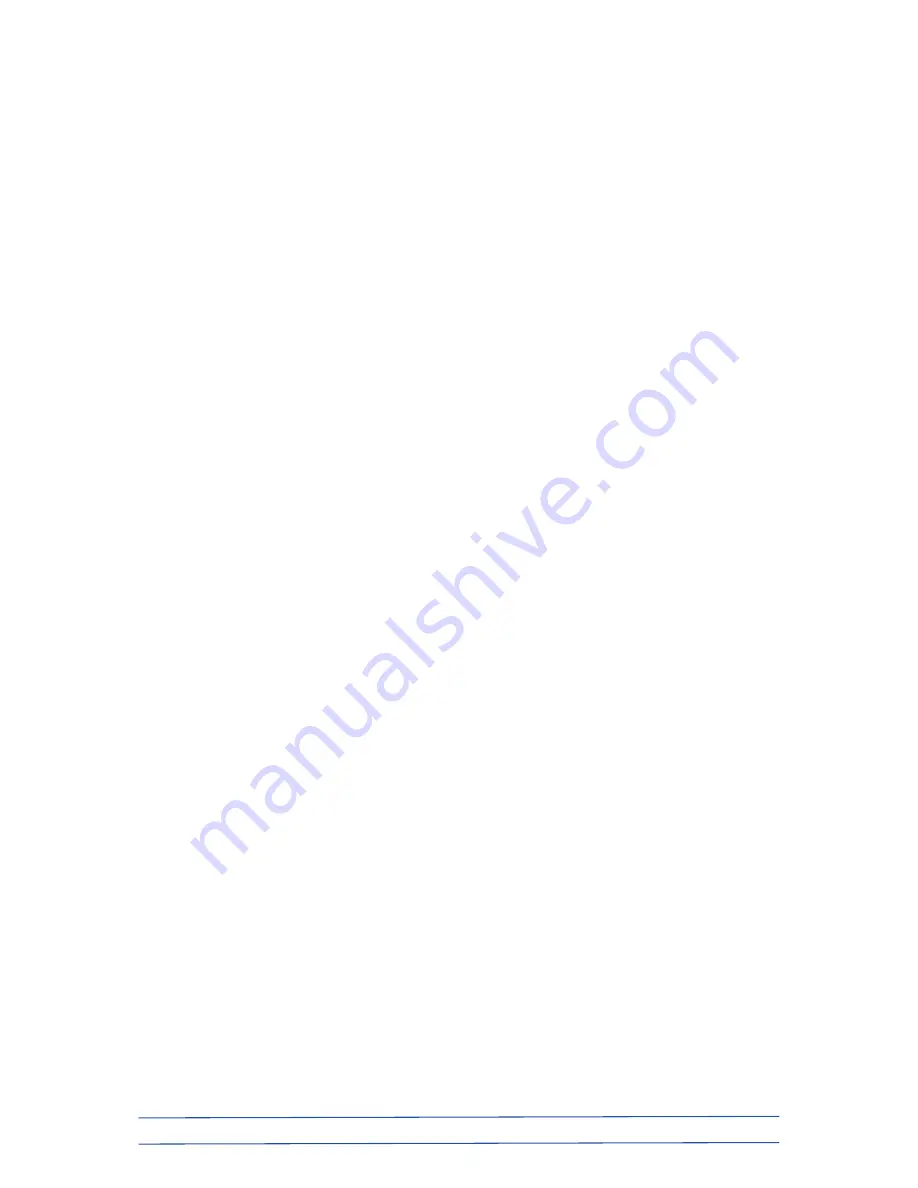
OMRON ELECTRONICS LTD
●
Technical Support: 0870 752 0871 or visit www.myOMRON.com
3
Preparation:
Installing the Analogue I/O Option Module:
1. Remove the blanking cover from the leftmost Option Board position of the CP1L-E
PLC (Slot 1) and insert the CP1W-ADB21/DAB21V/MAB221 module.
2. If you have ordered the JX or MX2 inverter option, please insert the CP1W-CIF11
RS422/485 option module into the rightmost Option Board position (Slot 2). The
supplied software application for the JX/MX2 inverter is written assuming that that
this module will be located in Slot 2*
* Note that CP1L-E20 models only have one expansion slot on the front of the CPU; this is designated as ‘Slot 2’
Wiring the PLC, HMI and power supply:
The S8VS-06024 power supply included with your kit is capable of supplying 2.5A at
24VDC, which is intended to supply the required power to the CP1L-E PLC, the NB-series
HMI, the Westermo 5-port Ethernet switch and all I/O signals to the inverter and
servomotor systems. If you are connecting additional devices to the outputs of the PLC
that require 24VDC, please be aware of the maximum current capability of this power
supply.
1. Using 0.5mm
2
– 2.0mm
2
cable, connect a 230VAC mains supply to the S8VS-
06024 in accordance with datasheet T01E-EN-02
(see Resource CD > TECHNICAL
DOCUMENTATION > S8VS PSU )
2. Using 0.5mm
2
(20AWG) wire, connect the ‘+V’ output terminal of the S8VS-06024
power supply to the ‘+’ input terminal of the PLC and the ‘24V’ terminal of the NB-
series HMI
3. Using 0.5mm
2
(20AWG) wire, connect a ‘jumper’ between the ‘+’ terminal of the
PLC and the ‘COM’ terminal, as show in diagram 1 overleaf.
4. Using 0.5mm
2
(20AWG) wire, connect the ‘-V’ output terminal of the S8VS-06024
power supply to the ‘-’ input terminal of the PLC and the ‘0V’ terminal of the NB-
series HMI
5.
Using 0.5mm
2
(20AWG) wire, connect ‘jumpers’ between the first four ‘COM’
terminals of the PLC output terminal block and a longer wire to the ‘-V’ output
terminal of the S8VS-06024 for NPN configuration (CP1L-M30DT-D model) or to
the ‘+V’ terminal for PNP configuration (CP1L-M30DT1-D model).
This step is only
necessary if you have selected the SmartStep2 servomotor option.
6. Connect the NQ-CN222 cable between the NQ HMI and the PLC, connecting the
end marked “PT” to the HMI.
Note: If you selected the SmartStep2 servomotor option, you will have been supplied with
a transistor output PLC, either CP1L-M30DT-D (NPN outputs) or CP1L-M30DT1-D (PNP
outputs). Pleas ensure that you follow the correct wiring procedure depending on your
model; page 18 for PNP or page 20 for NPN. Although the inputs (to the PLC) may be
wired for NPN or PNP, the shown configuration provides NPN inputs, which are necessary
for compatibility with the SmartStep2 output signals.
If you have not chosen the SmartStep2 option, you can wire the inputs for PNP
configuration, by connecting the ‘COM’ terminal to the adjacent ‘-‘ (0V) terminal.