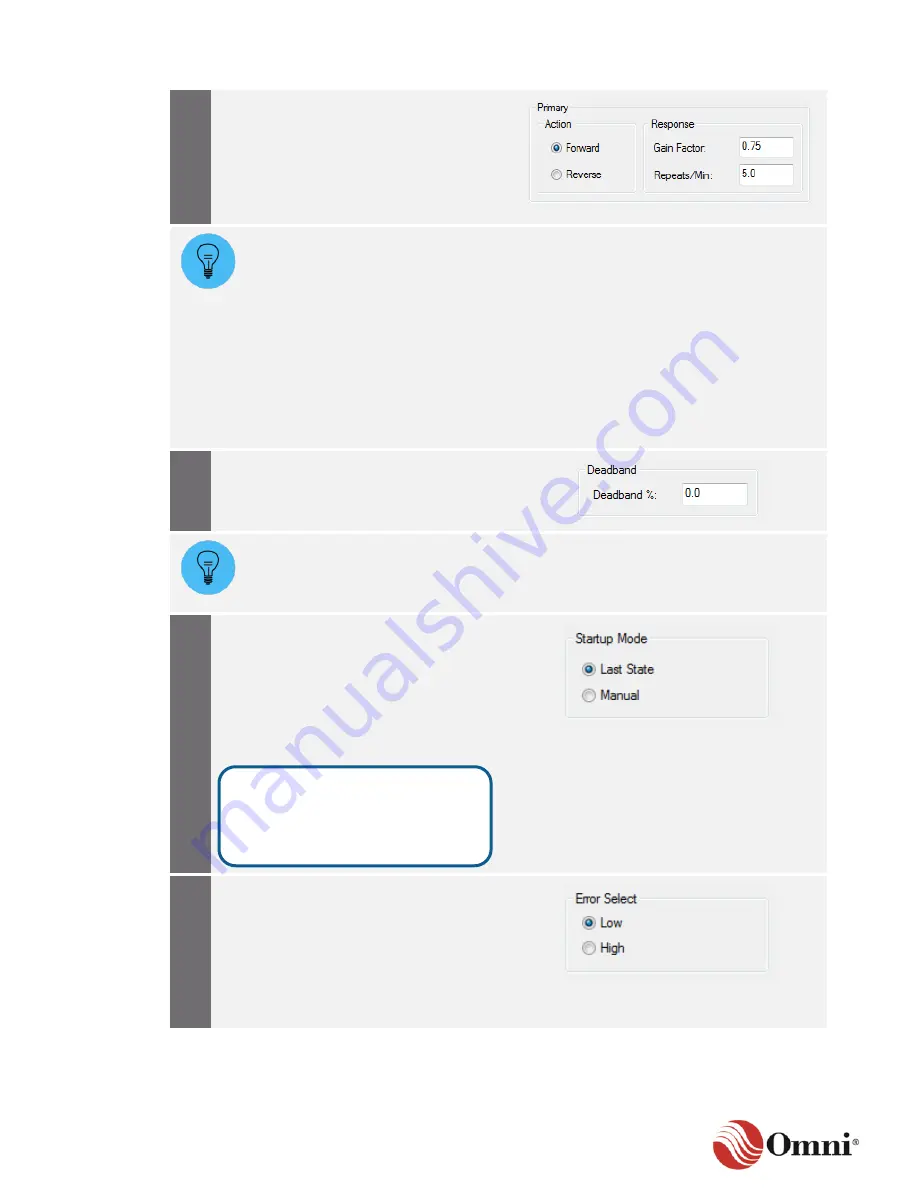
OMNI 4000/7000 Operations and Maintenance Guide
– Rev F
3-50
OMNICONNECT® Operations
5.
In the
Response
group, enter the
Gain
Factor
and
Repeats/Min
values for the
primary control variable.
a. Enter a
Gain Factor
number between
0.01 and 99.99.
b. Enter a
Repeats/Min
value between
0.0 and 40.00.
The
Primary Gain Factor
setting determines how responsive the control will be to
changes or upsets to the primary variable. The higher the entry, the more
responsive the control, but a value that is too high will cause instability and
oscillations to occur. If the setting is too low, the system will be slow to respond and
unable to adapt to changing conditions. For flow control, an initial value of 0.75
is reasonable.
The
Repeats per Minute
entry determines the integral action of the controller.
Integral action gradually integrates the error between the measurement and the
setpoint, adjusting the error to zero. The larger this entry is, the faster the output will
respond. If this entry is set too high, the system will be too responsive, and the
controller will overshoot the setpoint, causing instability and oscillations. An initial
value of 5 is a reasonable starting point for both primary and secondary entries.
6.
Enter a
Deadband %
number.
PID
Deadband
is used to minimize wear and tear on the control valve actuator in
cases where the controlled variable is continuously changing. The control output of
the flow computer will not change as long as the calculated PID error percentage is
less than or equal to the entered
Deadband
percentage.
7.
Select the
Startup Mode
:
a. Choose
Last State
to keep the PID
loop in the operating mode it was in
before a system reset occurs.
b. Choose
Manual
to start up in the
Manual Mode
with the control output
percentage frozen to the value it was
before the system reset.
8.
Select the
Error Select
parameter:
a. Choose
Low
to instruct the flow
computer to control which variable
(primary or secondary) has the
“lowest calculated error percentage.”
b. Choose
High
to control which variable
has the “highest calculated error
percentage.
”
This entry determines how the PID
control will resume after a system
reset or power-up (such as a
momentary power loss).