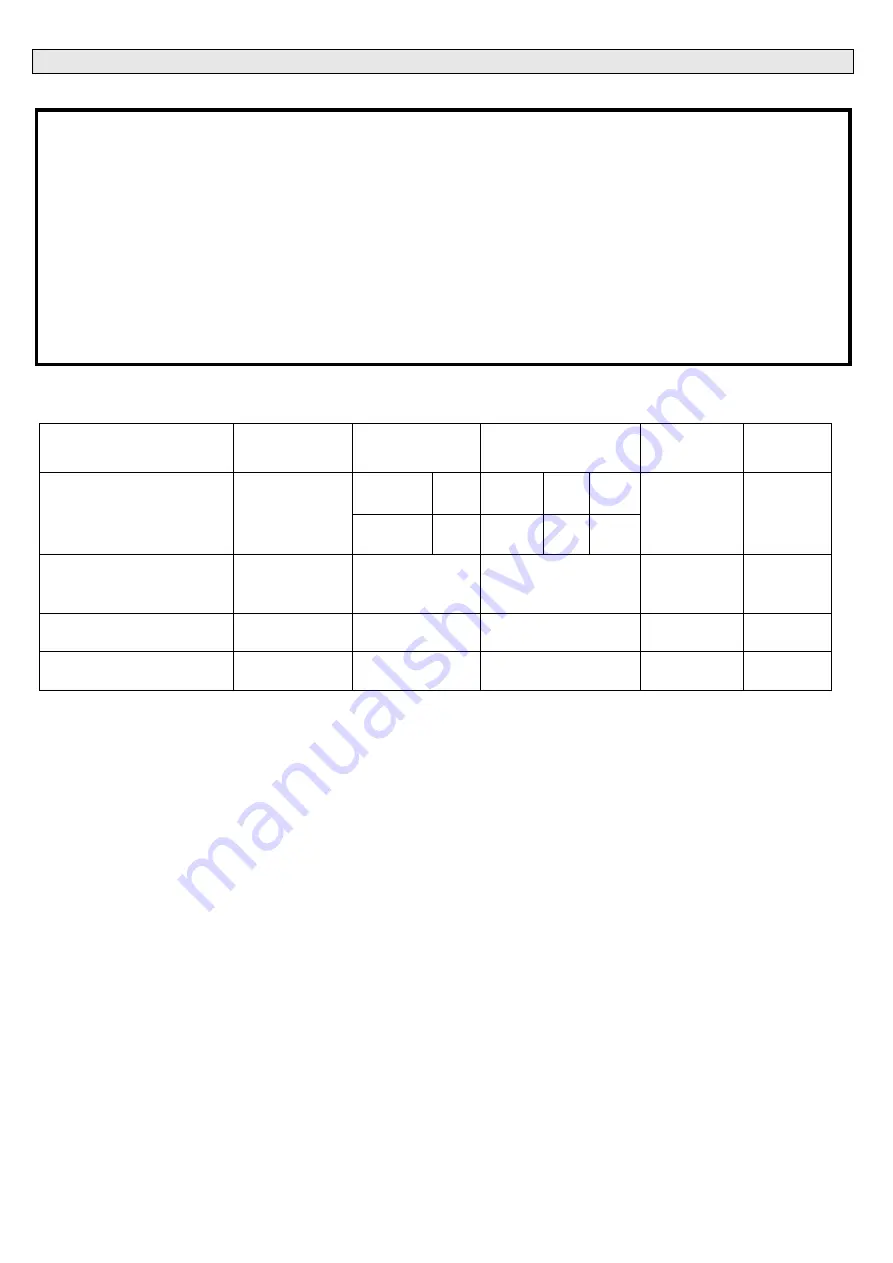
Cod. 710.0159.01.00 Rev0A – 10.2011
5 - 275
2.0 SAFETY INFORMATION
2.1 General safety instruction
SAFETY INFORMATION
This dryer has been designed and manufactured in accordance with the European safety directive
2006/42/CE
Machine Directive
2006/95/CE
Low tension Directive
2004/108/CE
Electromagnetical compatibility Directive
97/23/CE
PED Directive
According to PED Directive, this plant is supplied with safety devices on the frigorific circuit, calibrated according to the
under mentioned specifications.
The working life of such equipments is expected between 10 and 20 years.
Any installation, use and maintenance operations must be done according to the instructions contained in this manual and in
accordance to the national rules.
Any cleaning/maintenance operation which needs access to the dryer must be carried out by qualified and export personnel
who must be aware of all necessary precautions.
The machine has been designed and manufactured to be used in conformity to the following specifications.
In case of different use of the machine or not in conformity to this manual, the Manufacturer can’t be accused of any
responsibility.
2.2 Equipment nameplate values
(Nameplate values extracted from Calculation data sheet)
Fluid
Circuit Side
Press. Max. Amm.
Safety devices set
Work. Temp
Design Temp
MAWP
"PS" (bar rel)
(bar rel)
(°C)
(°C)
Freon HFC
(R507, R407c, R134a, R404a)
R134a R407c
R404a,
R507
R134a
R407c
R407c
R404a,
R507
Low press. -LP
20
20
18*
18*
18*
min -10°
min -15°
High Press. -HP
28
30,8
18*
27,9*
29*
max +100°
max +100°
Compressed air (Dryers)
Compress. Air Side
min 0
(Customer care)
min 0°
min 0°
max. 13(aluminium)
max +60°
max +60°
max. 16 (copper)
Refrigerant Liquid (Chiller)
Liquid side
min 0
(Customer care)
min -10°
min -15°
max 8
max +45°
max. +45°
Ambient air
Ventilation side
Atm.
( Not Appl.)
min 5°
min -15°
max +45°
max. +45°
* - Safety Pressure switch Cat IV PED, Manual reset
Welding Joints Coefficient
z
0,7
(Table 5.6-1)
Tickness allowance
c
0,1
mm
( Per rame - For copper )
(Not required for surfaces in contact with freon - EN 14276-1)
c
1
mm
( Per acciaio - For carbon steel )
Manufacturer design code
717.0012.01.00
Rev.08
Essential Safety Requirements
ON10.0010.02
Rev.01
Manufacturer Working Procedure
PO 08.2
Rev.01
Assembly classification according PED 97/23
Cat. II
Evaluation Module according PED 97/23
Mod. A1
PED Notified Body number
0474
2.3 Information about remaining risks of the equipment
Fire:
This equipment, in accordance to EN-378-2, isn’t supplied with freon drain safety valve.
In case of fire it is preferable to use fire extinguishers or extinction systems basically composed of powder or foam or carbon dioxide: it is possible to
cool the equipment thanks to nebulized water.
Avoid the massive use of water because, in case of freon gas leak, the chemical reaction can cause caustic effects, even if small.
In any case it is necessary to cool down the ambient and/or the equipment’s temperature and before any intervention wait until the temperature has
been reduced.
Therefore it is preferable to insert this equipment into the Fire Prevention and Factory Safety Plan.
Arrange adequate actions capable to prevent and fight the possible risk.
Dispersion of freon gas in the ambient:
the refrigerant means is toxic only if inhaled at high concentration: it is necessary to provide an adequate ventilation in the room where the equipment
is installed.
In any case check the scheme showing the values and the risk sentences.
Excessive pressure on the compressed air side:
this equipment isn’t supplied with safety devices on the compressed air side.
The safety devices on the compressed air side must be carried out by the installer.
Such devices will have to be carried out according to the applicable National Norms and to the limits mentioned in this Manual.
Ozone layer deterioration:
The adoption of HFC freon reduce to the minimum ozone layer deterioration and greenhouse effect.
Summary of Contents for ESD 1300
Page 2: ...1 119...
Page 4: ...5 119...
Page 87: ...RU OMI 1 ON OFF 12...
Page 88: ...1 0 1 1 OMI 5 IP 42 1 2 1 2 3 4 5 6 7 8 9...
Page 90: ...HFC 3 0 3 1 OMI 0 C 50 C 90 12 OMI 3 2 40 1000 3 3 1 2 3 4 5 10...
Page 91: ...4 0 1S1 ON OFF 3 3 5 0 5 1 5 2 5 3 6 6 0 SET POINT 1 DEW POINT...
Page 92: ...6 1 HP LP CO14 6 2 ON 6 3 3 ON OFF OFF SET POINT...
Page 93: ...6 4 15 1 ALrM 2 ALOG 3 C1Hr 4 Hot Key UPL 6 5 6 5 1 P2 P3 P4 6 5 2 1 2 AlrM 3 rSt NO 4 rSt rSt...
Page 101: ...7 0 A B 0 C A...
Page 103: ...8 3 TEST 9 0 10 0 R134a R407C R507 15 15 11 0 EN378 1...
Page 122: ......