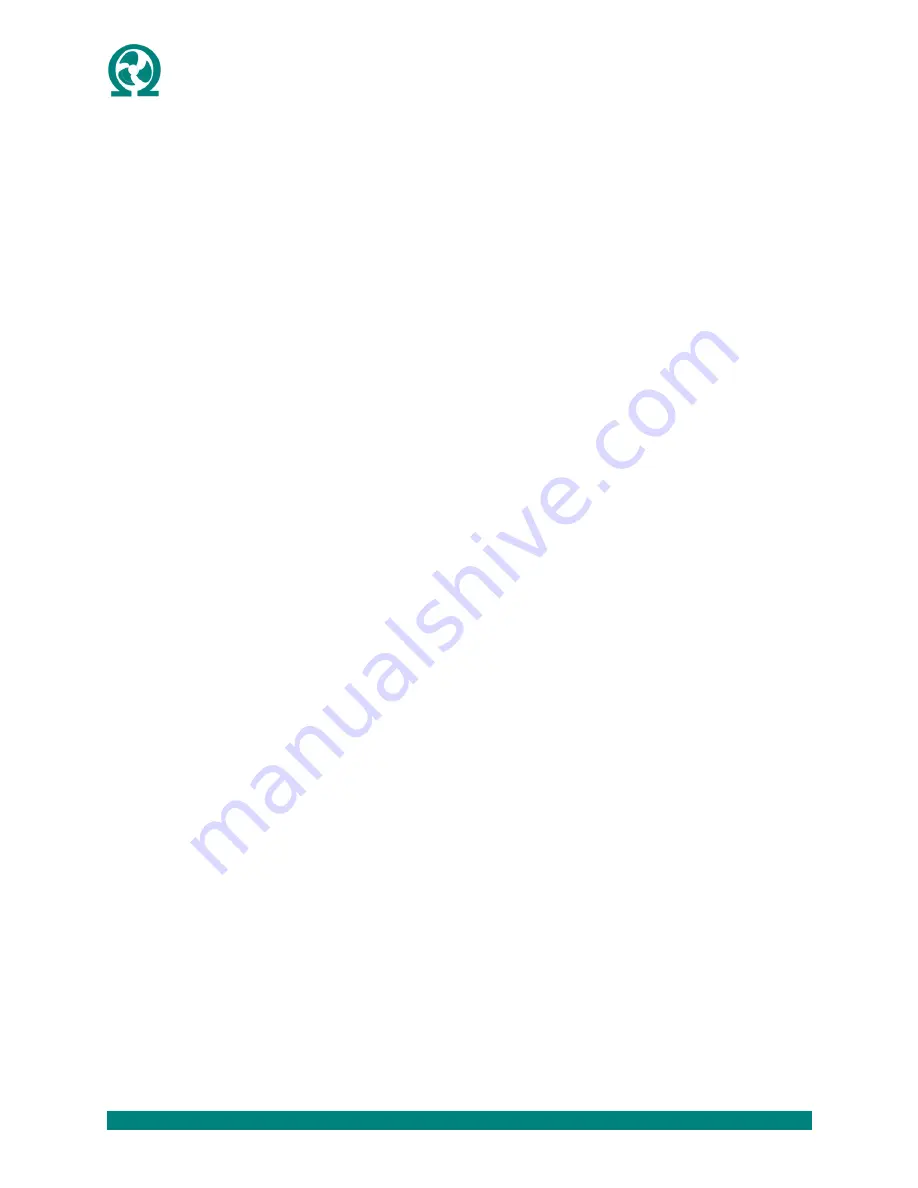
OMEGA | OMEGA-VSHP.F-PGD-1904
44
www.omega-heatpump.com
1 GENERAL
Install Omega series Vertical Stack Heat Pumps as indicated on
the plans and capacities listed in the schedule and specifications.
Each unit shall be factory tested and ship factory-charged with R-
410A refrigerant. All units from 1/2 to 3 Tons shall be tested and
certified by ASHRAE/ANSI/AHRI/ ISO 13256-1 and ETL listed for
United States and Canada. Each unit shall have factory affixed
label showing ASHRAE/ANSI/AHRI/ISO and ETL logos. Cabinets
and refrigeration chassis shall be factory wired and pre-piped.
2 CABINET
2.1
The vertical stacked heat pump units shall be Omega
(Gold) or (Silver) Series. Units shall provide scheduled capacities at
the ampacity and voltage specified.
2.2
The cabinet shall be 20-gauge galvanized steel with
riveted internal components for rigidity. Cabinet shall have internal
surfaces insulated with 1 inch thick, 3.5 lbs. high-density, mould
resistant, thermal and acoustic insulation. Insulation shall meet
NFPA 90, UL-181, and ASTM-C1071 standards and insulation shall
have a flame spread of less than 25, and a smoke developed clas-
sification of less than 50 per ASTM E-84 and UL 723.
(STANDARD SILVER UNIT) The unit shall be a single cabinet
construction. Contractor shall be responsible for isolating the
supply duct and supply grille from the cabinet.
(OPTIONAL GOLD UNITS) The cabinet shall be sectionalized
for acoustic and installation purposes. The lower section shall
include the risers, blower and fan motor assembly, all con-
trols, and removable refrigeration chassis. The upper section
shall be an acoustic discharge plenum lined with 1 inch thick,
3.5 lbs. high-density, mould resistant, thermal and acoustic
insulation. The discharge plenum shall be designed to be
fastened to the underside of the concrete slab with field cut
”Knockout” discharge openings. There shall be no rigid con-
nection between the upper and lower cabinet sections. A
factory supplied flexible canvas connection shall be provided
between the upper and lower sections joined by factory pro-
vided “S” and “D” cleats. Heat pump manufacturer shall
factory attach flexible connection to the plenum section.
Installing contractor shall make the final connection of the
flexible connection to the lower cabinet section with field
provided sheet metal screws and factory supplied “S” and
“D” cleats.
2.3
A removable inner chassis service panel allowing ser-
vice access to the fan and compressor compartment shall be pro-
vided with each unit.
2.4
The drain pan shall be 16-gauge stainless steel. The
drain pan shall come standard with a condensate overflow switch.
The drain pan outlet shall be readily accessible for cleaning with a
7/8 inch OD copper drain connection. Unit shall be provided with a
flexible p-trap condensate hose for connection to the condensate
riser.
2.5
Factory installed supply and return risers shall be (Type
L) (Type M) copper, with (factory) (field) mounted shut-off ball
valves on each supply and return riser. Valves shall be brass and
rated for 400 psig. A (Type M/DWV) condensate riser shall be
(factory) (field) installed. Risers sizes shall be installed according to
building plans.
2.6
Risers shall be factory swaged. Transition pieces shall
be field supplied.
2.7
Unit cabinet shall come with supply discharge opening
“knockouts”.
An optional noise attenuating insulated privacy air
baffle (LOSB) shall be provided for horizontal supply discharge
openings. All cabinet discharge openings shall include 1-1/2 inch
drywall flange around the full opening perimeter. Supply ducts
shall not be rigidly attached to the cabinet and shall be acoustically
isolated from cabinet using flexible canvas connections.
2.9
Each unit shall have an (Acoustic) (Perimeter) return air
panel. The panels shall be insulated with 1/2 inch thick, lined
fiberglass insulation. The panel shall be easily removable without
tools to allow access to the filter, chassis compartment and
(optional) service disconnect switch.
3 FAN & BLOWER
3.1
Each unit shall include a factory mounted forward
curved, double inlet double width centrifugal direct drive fan and
motor assembly with internal overload protection. The blower fan
assembly shall be positioned horizontally from a sheet metal blow-
er deck.
3.2
Units shall be supplied with a 3 speed PSC fan motor
with permanent split capacitor or ECM fan motor. Fan motors
speeds shall be field selectable using unit mounted 3-speed fan
switch or by 3-speed thermostat.
4 REFRIGERATION CHASSIS
4.1.
Provide high temperature and pressure rated water
hoses for connection of the risers to the chassis. The hoses sup-
plied shall be constructed with an inner core of rubber, a stainless-
steel metal braid, and rubber outer covering. Fittings shall be brass
construction. Hoses shall carry a pressure rating of 600 psig.
4.2.
The compressor chassis shall be mounted and vibration-
ally isolated on 12-gauge slide rails using a double isolated base.
Compressor shall have an acoustical enclosure ensuring compres-
sor noise is isolated from air stream. Provide plug type electrical
connections for chassis control and power connections allowing for
easy removal of the chassis from the front of the cabinet.
4.3
The refrigeration circuit shall have two service valves,
for measuring high and low refrigerant pressure, in the chassis
compartment enclosure. The refrigerant circuit shall contain a
thermal expansion valve (TXV) refrigerant metering device and a
reversing valve.
4.4
Compressor shall be hermetically sealed type with inter-
nal thermal overload protection. Compressor shall be mounted on
rubber vibration isolators.
4.5
Air side coils shall have copper tubes mechanically
10. SPECIFICATIONS