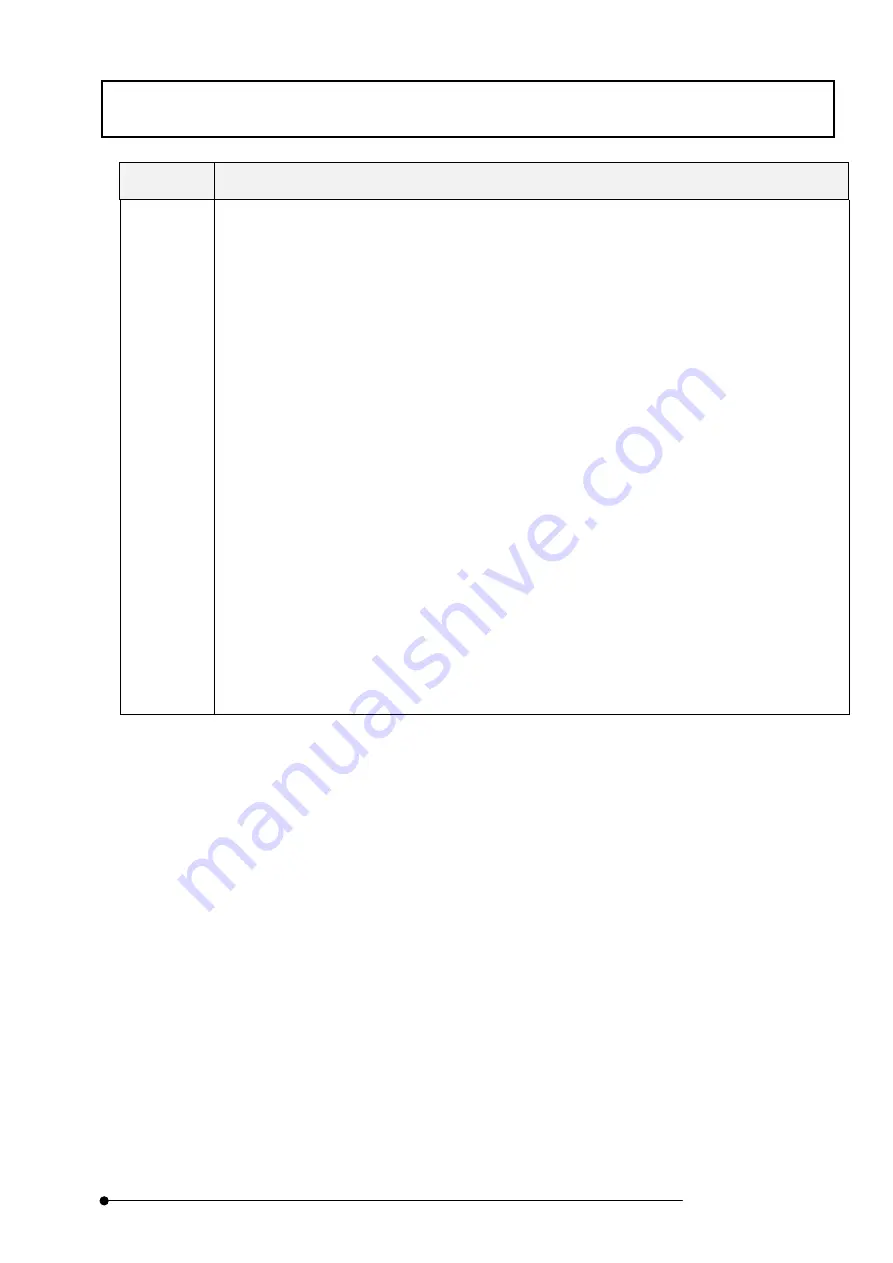
Maintenance Manual
Test Programs
3-25
Page
Test No./
Test Name
Function Outline
[M2]: Set date <Date>
Parameters to be set are displayed on the liquid crystal panel.
Select the parameters to be changed using the 4-way buttons.
[M2]: Save <Save>
[M3]: Delete <Back space>
[M4]: Exit the display <Exit>
[No.1 to No.9]: Input numbers 1 to 9
4-way buttons [RIGHT] and [LEFT]: Move the cursor.
4-way buttons [UP] and [DOWN]: Move between items.
Parameters that can be set:
•
Year <Year>
the last two digits of a calendar year
•
Month <Month>
•
Date <Date>
•
Hour <Hour>
•
Minute <Minute>
•
Second <Second>
Select an item using the 4-way buttons, and input a value using the [Wafer No.] buttons.
After the item has been corrected, press [M2]: <Save> to register the corrected item.
To quit the program without correcting the item, press [M4]: Exit the display <Exit>.
Summary of Contents for AL120-6Series
Page 2: ...This page intentionally left blank ...
Page 9: ...Operation Maintenance Manual Introduction Safety Precautions i 7 Page AL120 86 Series Unit mm ...
Page 16: ...Introduction Conformity Standards Operation Maintenance Manual i 14 Page ...
Page 17: ...Operation Maintenance Manual Introduction Conformity Standards i 15 Page ...
Page 20: ...Maintenance Manual Table of Contents C 2 This page intentionally left blank Page ...
Page 56: ...Test Programs Maintenance Manual 3 26 Page This page intentionally left blank ...
Page 64: ...Replacement of Consumables Maintenance Manual 4 8 Page This page intentionally left blank ...