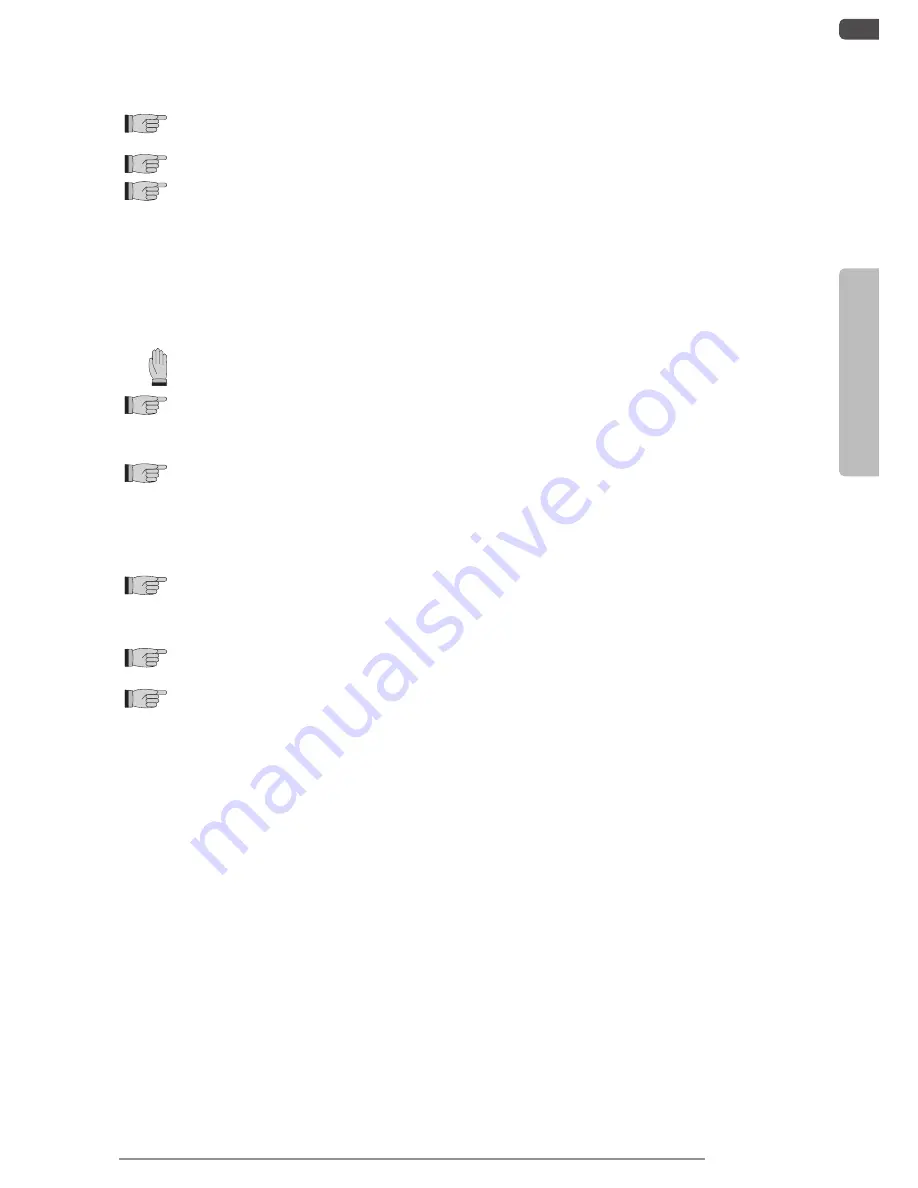
45
ENGLISH
UNICO BOILER
2
2.2.7
Cooler connection (figg. 4, 29, 30)
Take the cover off the boiler (ref. 4 fig. 3) after removing the nut cover and the fixing nut.
IMPORTANT: Do not make the connections using normal hydraulic pipes that could contain residues of flashing, dirt or
water and that could damage the parts inside the unit and interfere with proper operation.
Use only special copper pipes for cooling, that are supplied clean and sealed at the ends.
After cutting the proper lengths, seal the ends immediately on the roll and cut piece.
Pipes for refrigeration with preinsulation can also be used.
Only use pipes with the a diameter suitable for the dimensions described in the technical data sheets.
- Plan the route of the pipeline so as to reduce the length and number of bends as much as possible for best performance of
the system. The maximum length of the lines connecting the outside unit to the inside unit is 10 m in both directions.
- maximum height different between two units +/- 5 m.
- Fasten a cable raceway to the wall (possibly with internal partitioning) of suitable size for the pipes and electric wires to pass
through.
- Cut the sections of pipe leaving an extra 3-4 cm on the ends.
IMPORTANT: use a wheel pipe cutter only to cut the pipes (fig. 28) clamping it in short lengths so as not to crush the pipe.
NEVER USE A NORMAL HANDSAW
scraps could fall inside the pipe and enter the circuitry of the system, damaging the parts severely (fig. 29 A).
- Remove possible burrs with the special tool.
IMPORTANT: immediately after cutting and deburring the pipes, seal the ends with insulating tape.
If you do not use preinsulated pipes, they must be insulated as follows:
- material: polyurethane foam with closed cells
- max. coefficient of transmission : 0,45 W/ (Kxm
2
) or 0.39 kcal/(hxCxm
2
)
- minimum thickness: 6 mm (for liquid pipes)
- minimum thickness: 9 mm (for gas pipes)
Do not place both pipes in the same sheath, as this would jeopardize the proper operation of the system (fig. 29 B).
- Bind any joints in the sheath securely with insulating tape.
- Before flaring the pipe ends, insert the fastening nut (fig. 30 A).
- Flare the pipe ends using the special tool. Take care not to break, crack or split the pipe (fig. 30 B).
- Lubricate the connecting thread with oil for coolant
(DO NOT USE ANY OTHER TYPE OF LUBRICANT)
.
- Screw the pipe nut manually on the connecting thread.
- Tighten using a wrench to hold the threaded part of the connector, so as to avoid twisting the pipe, and a
dynamometric wrench on the nut (fig. 31) calibrated with the following values depending on the size of the pipe:
- 14-18 Nxm (1.4-1.8 kgxm) for pipe diameter ø 6-6.4 mm (1/4")
- 33-40 Nxm (3.3-4.0 kgxm) for pipe diameter ø 9.5-10 mm (3/8")
CAUTION:
- This product may only be serviced by a qualified and certified technician.
- Do not allow the fluorinated gas inside to escape.
- Make sure the fluorinated gas is never released into the atmosphere during installation, servicing or disposal.
- If any leakage of fluorinated gas is discovered, the leak must be found and repaired as quickly as possible.
- Any use of fluorinated gas in this product must comply with Regulation (EU) 517/2014 and any local rules that apply.
- No additional filling is needed in the installation phase.
- Do not exceed the load stated on the data plate.
Summary of Contents for Unico Boiler
Page 1: ......
Page 3: ...3 UNICO BOILER 7 B A 8 9 10 6 ...
Page 4: ...4 17 A 12 13 15 16 14 A B A 11 ...
Page 5: ...5 UNICO BOILER 18 19 20 B A A 21 A C B ...
Page 6: ...6 24 H G LED D LED C LED B LED A 25 A B 22 A A D C B 23 26 ...
Page 7: ...7 UNICO BOILER 27 29 B A 28 B 31 30 A ...
Page 8: ...8 33 32 A 34 A H B C D E F E G ...
Page 9: ...9 UNICO BOILER 35 37 36 UNICO BOILER WALL UNICO BOILER MASTER B A C D C B A D ...
Page 10: ...10 39 A B C B D C A E F B A C 40 A B 38 ...
Page 11: ...11 UNICO BOILER 42 B A 41 8 2 3 1 4 6 9 ...
Page 121: ......
Page 122: ......
Page 123: ......
Page 124: ...277482A 2 www olimpiasplendid it info olimpiasplendid it ...