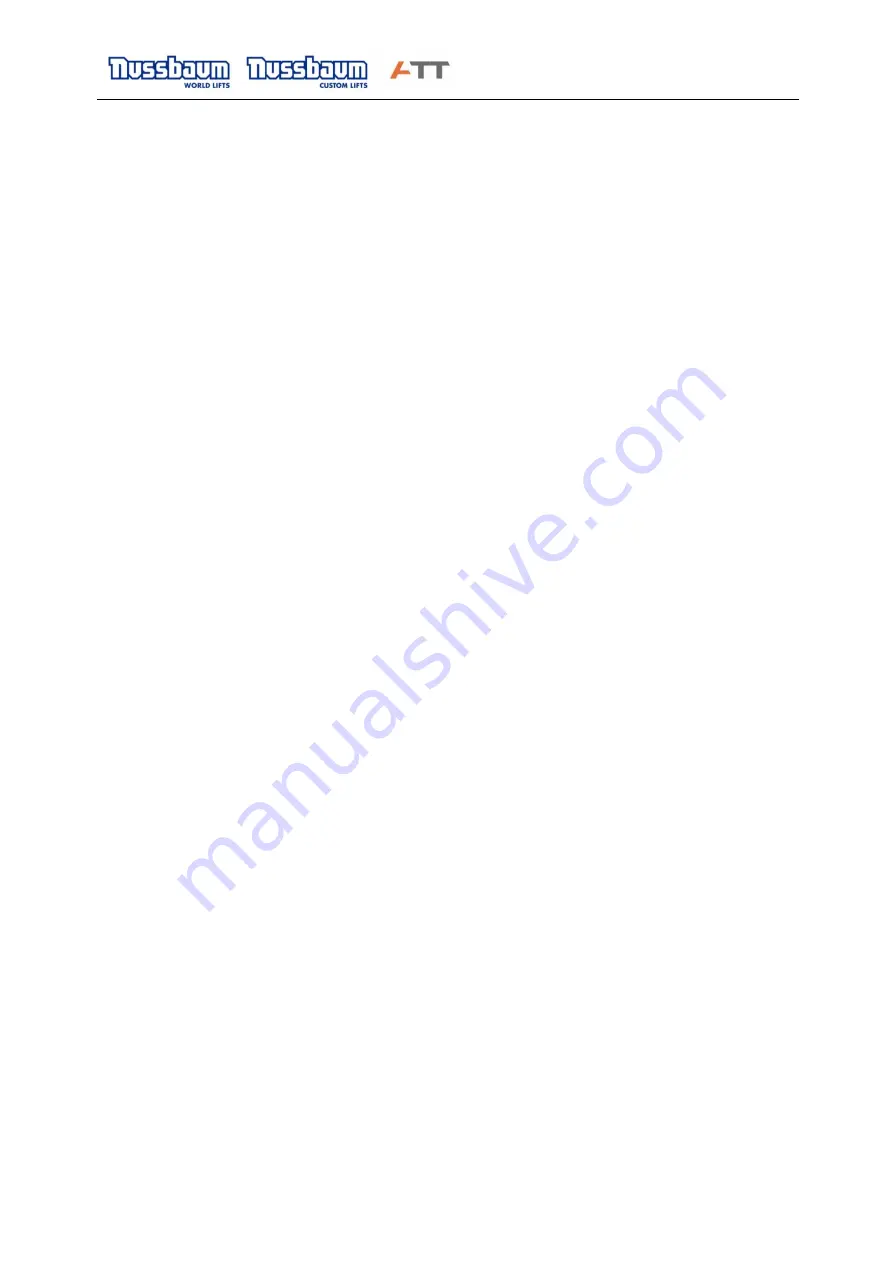
Operating Manual and Inspection Book
COMBI LIFT 4.80 H / HYMAX II 8000
46
Version 3.0
9.2 Erection and bolting down the lift
It is necessary to dowel the columns at 4 points. For this a concrete floor without rein-
forcement, thickness of 140 mm and quality C20/25 is needed. In case of doubt a test
drill is necessary and a dowel is to put in. Afterwards the Liebig-dowel (German Dowel
manufacturer) is to fasten with a torque of 40 Nm. If the necessary torque is too low or
if there are cracks in the concrete floor, a foundation in accordance with the sheet
”foundation plan” is to erected. As well it must be paid attention that the installation
place is even to guarantee a horizontal erection of the lift.
• Put runways on two erection trestles at installation place, pay attention of exactly
difference between the runways (refer to data sheet)
• Position the Traverses on the face of the runways, and put the plugs together.
• Lay out Ropes into right position (see pic)
• Fasten the crossbeam at the rail. Connect the plugs (optional: lighting, CE-Stop
switch).
• Pull the ropes through the crossbeam.
• Pull cables (power supply, air etc.) through the crossbeam and connect..
• Position the columns at the end of the crossbeam.
• Adjust the columns with a water bubble.
• Bore holes to fix the dowels through the borings of the base plates. Clean holes with
pressure air. Put in safety dowels with washers in borings. The manufacturer
demands LIEBIG safety dowels type B 10 or equal dowels of another manufacturer
(with allowance) but observe their regulations! Before doweling check concrete
floor with quality C20/25 if the concrete floor goes to the top edge of the floor. In this
case the dowels have to be chosen according to picture 9. If the ground is covered
with floor tiles, the dowels have to be chosen according to picture 10.
• Tighten the dowels a little bit.
• Fasten the ropes at the top of the column.
• Check the position of the columns again.
• Connect the electrical power supply.
Summary of Contents for COMBI LIFT 4.80 H
Page 2: ......
Page 14: ...Operating Manual and Inspection Book COMBI LIFT 4 80 H HYMAX II 8000 14 Version 3 0...
Page 17: ...Operating Manual and Inspection Book COMBI LIFT 4 80 H HYMAX II 8000 17 Version 3 0...
Page 18: ...Operating Manual and Inspection Book COMBI LIFT 4 80 H HYMAX II 8000 18 Version 3 0...
Page 19: ...Operating Manual and Inspection Book COMBI LIFT 4 80 H HYMAX II 8000 19 Version 3 0...
Page 20: ...Operating Manual and Inspection Book COMBI LIFT 4 80 H HYMAX II 8000 20 Version 3 0...
Page 21: ...Operating Manual and Inspection Book COMBI LIFT 4 80 H HYMAX II 8000 21 Version 3 0...
Page 22: ...Operating Manual and Inspection Book COMBI LIFT 4 80 H HYMAX II 8000 22 Version 3 0...
Page 23: ...Operating Manual and Inspection Book COMBI LIFT 4 80 H HYMAX II 8000 23 Version 3 0...
Page 24: ...Operating Manual and Inspection Book COMBI LIFT 4 80 H HYMAX II 8000 24 Version 3 0...
Page 26: ...Operating Manual and Inspection Book COMBI LIFT 4 80 H HYMAX II 8000 26 Version 3 0...
Page 27: ...Operating Manual and Inspection Book COMBI LIFT 4 80 H HYMAX II 8000 27 Version 3 0...
Page 28: ...Operating Manual and Inspection Book COMBI LIFT 4 80 H HYMAX II 8000 28 Version 3 0...
Page 29: ...Operating Manual and Inspection Book COMBI LIFT 4 80 H HYMAX II 8000 29 Version 3 0...
Page 30: ...Operating Manual and Inspection Book COMBI LIFT 4 80 H HYMAX II 8000 30 Version 3 0...
Page 31: ...Operating Manual and Inspection Book COMBI LIFT 4 80 H HYMAX II 8000 31 Version 3 0...
Page 32: ...Operating Manual and Inspection Book COMBI LIFT 4 80 H HYMAX II 8000 32 Version 3 0...
Page 33: ...Operating Manual and Inspection Book COMBI LIFT 4 80 H HYMAX II 8000 33 Version 3 0...