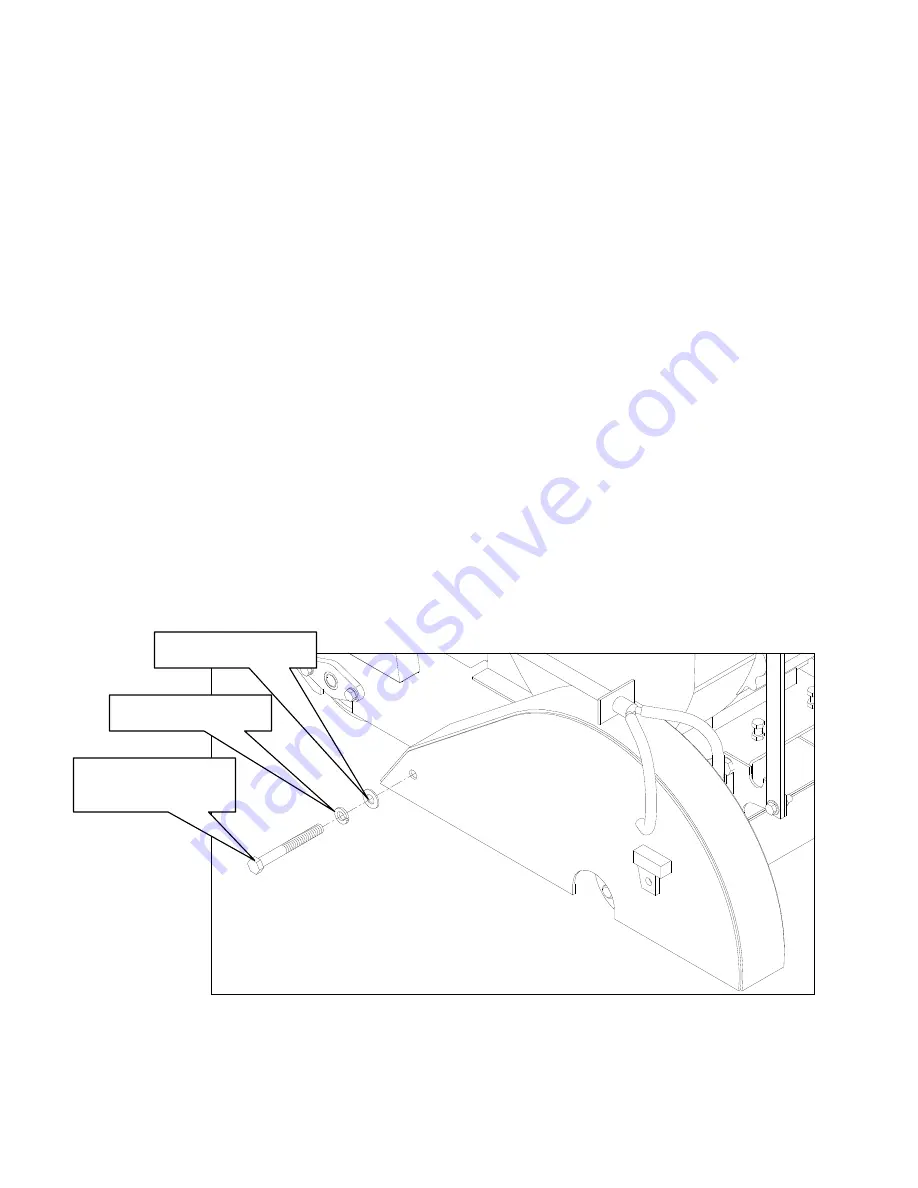
12
B. Changing the Blade Side:
1. Insure that the Ignition Power Key Switch is in the OFF position and
then disconnect the spark plug.
2. Remove the blade shaft nut, (NOTE: Operator’s Right side is a left
hand thread and the Operator’s Left side is right hand thread), and
remove the outside collar.
3. Clean off any foreign particles on the clamping surfaces of both the
outside and inside collars and on the mounting surface of the blade
and inspect the both collars for any damage and also inspect the drive
pin for damage. Reinstall the Blade Shaft Collars to the machine.
NOTE
: Replace any damage collars or pins before using the machine.
4. Inspect the blade for any damage, cracks, burnt or blue areas, missing
segments, and roundness of blade. Also inspect the arbor hole and
drive pin hole to insure both are round. If any problems are found do
not use the blade. In addition check that the blade is the correct
specification for the application.
5. Remove the Blade Guard from the machine by unscrewing the Blade
Guard Pivot Bolt from the rear of the Blade Guard. NOTE: Keep the
½” Flat Washer and ½” Lock Washer on the Bolt.
Blade Pivot Bolt Removal
Blade Guard
Pivot Bolt
½” Lock Washer
½” Flat Washer
Summary of Contents for C1320P
Page 1: ...OWNERS MANUAL MEDIUM CONCRETE SAWS MODEL C1320P FORM C1320P rev 9 2010...
Page 32: ...32 8 2 4 7 4 4 4 10 9 11 12 13 2 1 5 12 4 4 4 1 13 5 3 6 6 14 14 C1320P Raise Axle Group...
Page 36: ...36 1 10 5 14 13 16 15 14 13 7 16 15 19 C1320P Blade Guard and Water System Group...
Page 38: ...38 1 2 6 7 9 10 11 5 4 3 8 12 8 C1320P Controls and Console Group...
Page 42: ...42 1 2 4 3 4 9 5 10 8 To Blade Guard 7 C1320P Optional Water Tank Group...