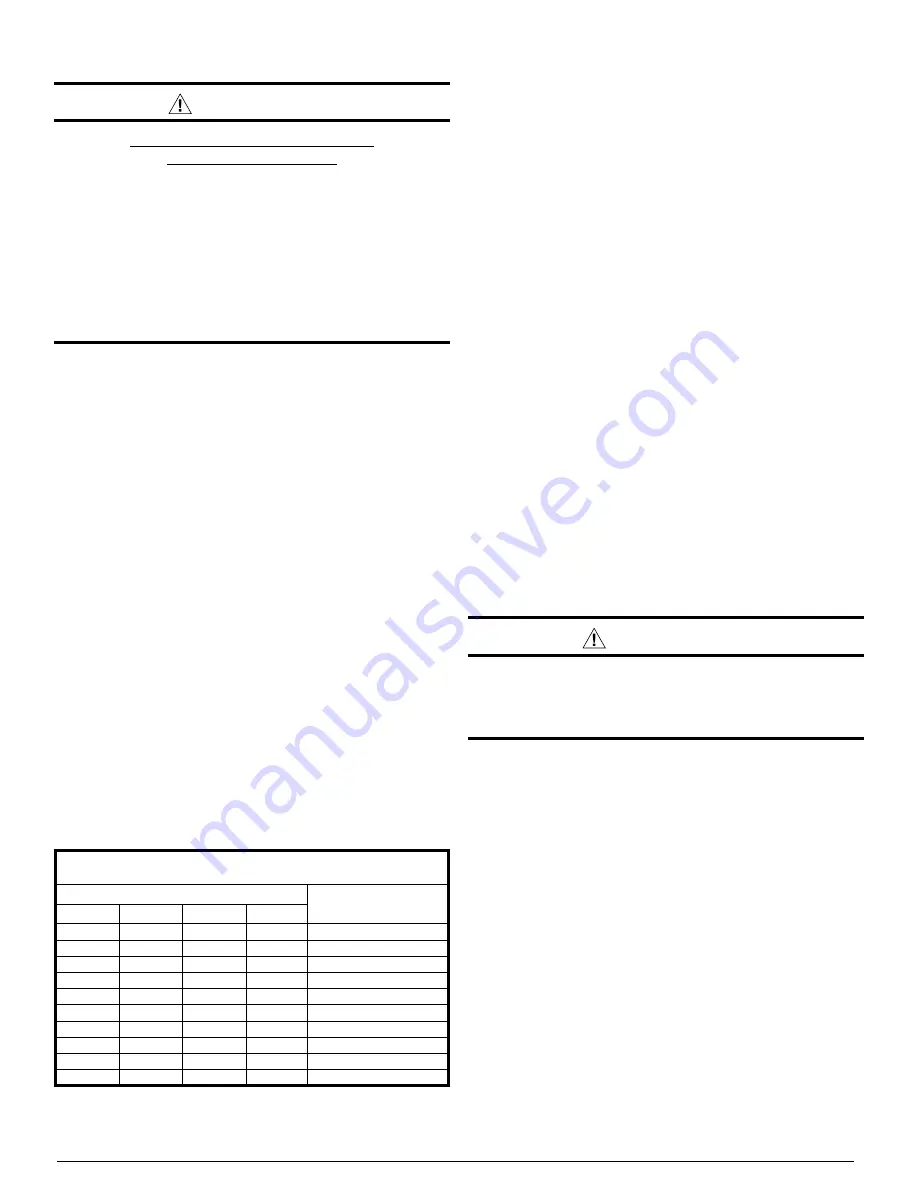
7
Line Voltage
• An electrical disconnect must be located within sight of and
readily accessible to the unit. This switch shall be capable
of electrically de-energizing the unit. See unit data label for
proper incoming field wiring. Any other wiring methods must
be acceptable to authority having jurisdiction.
• It is recommended that the line voltage to the unit be supplied
from a dedicated branch circuit containing the correct fuse
or circuit breaker for the unit.
• Overcurrent protection must be provided at the branch circuit
distribution panel and sized as shown on the unit rating
label and according to applicable local codes. See the unit
for maximum circuit ampacity and
maximum overcurrent protection limits.
• The installer should become familiar with the wiring diagram/
schematic before making any electrical connections to the
unit. See the unit wiring label or
.
• Use only copper wire for the line voltage power supply to
. Use proper code agency listed
conduit and a conduit connector for connecting the supply
wires to the unit. Even if not required by code, use of rain
tight conduit is always preferred.
• If replacing any of the original wires supplied with the unit,
the replacement wire must be copper wire consisting of the
same gauge and temperature rating.
• Provide power supply for the unit in accordance with the
unit wiring diagram, and the unit rating plate. Use UL listed
conduit and conduit connectors for connecting the supply
wires to the unit and for proper grounding. Field supplied
bushings for the power supply cables must be added to
support and protect the power supply cables.
Grounding
WarnInG:
the unit cabinet must have an uninterrupted or
unbroken electrical ground to minimize personal
injury if an electrical fault should occur. Do not use
gas piping as an electrical ground!
This unit must be electrically grounded in accordance with
local codes or, in the absence of local codes, with the National
Electrical Code (ANSI/NFPA 70) or the CSA C22.1 Electrical
Code. Use the grounding lug provided in the control box for
grounding the unit.
thermostat requirements
• This system can be controlled by any industry standard
thermostat. Set-back thermostats can be used, but are
generally not advantageous with geothermal systems. This
system has such low operational power requirements that
it is counter-productive to use them because the system
must work harder to bring the entire interior air space up to a
preferred temperature, rather than operating on a preferred
temperature “maintain” mode.
• If the system has electric strip heat back-up within the air
handler, the system can operate together with the electric
supplement heat, as the strip heating coils are installed
downstream of the refrigerant heat exchanger. The electric
strip heat is supplemental to the heat provided by the
geothermal system.
• The thermostat used with this equipment must operate in
conjunction with any installed accessories.
ElEctrIcal connEctIons
WarnInG:
ElEctrIcal shocK, FIrE or
EXPlosIon hazarD
Failure to follow safety warnings exactly could result
in serious injury or property damage.
Improper servicing could result in dangerous
operation, serious injury, death or property damage.
• Before servicing, disconnect all electrical power
to the unit.
• When servicing controls, label all wires prior to
disconnecting. reconnect wires correctly.
• Verify proper operation after servicing.
• Electrical connections shall be in compliance with all
applicable local codes and ordinances, and with the current
revision of the National Electric Code (ANSI/NFPA 70).
• For Canadian installations, the electrical connections and
grounding shall comply with the current Canadian Electrical
Code (CSA C22.1 and/or local codes).
Pre-Electrical checklist
• Verify the electrical wiring to the equipment is in compliance
with the maximum electrical capacity listed on the equipment
unit data label. This includes both the compressor unit and
the air handler selected for use, as well as any other related
supplemental equipment.
• Verify the circuit protection (fuse or circuit breaker size) is in
compliance with the minimum circuit amp capacity listed on
the unit data label. This includes both the compressor unit
and the air handler selected for use, as well as any other
related supplemental equipment.
• Verify all electric power wiring connections are correct and
tight prior to turning on any electrical power. Make sure
both the compressor section and air handler have been
properly grounded and have fuses and/or circuit breakers
in the primary electrical service box.
• Verify that the service provided by the utility is sufficient to
handle the additional load imposed by this equipment. See
• Verify factory wiring is in accordance with the unit wiring
diagram
. make sure no connections
came loose during shipping or installation.
coPPEr WIrE sIzE — aWG
(1% VoLTAGE Drop)
suPPlY WIrE lEnGth-FEEt
suPPlY cIrcuIt
aMPacItY
200
150
100
50
6
8
10
14
15
4
6
8
12
20
4
6
8
10
25
4
4
6
10
30
3
4
6
8
35
3
4
6
8
40
2
3
4
6
45
2
3
4
6
50
2
3
4
6
55
1
2
3
4
60
Wire Size based on N.E.C. for 60° type copper conductors.
table 2. copper Wire size