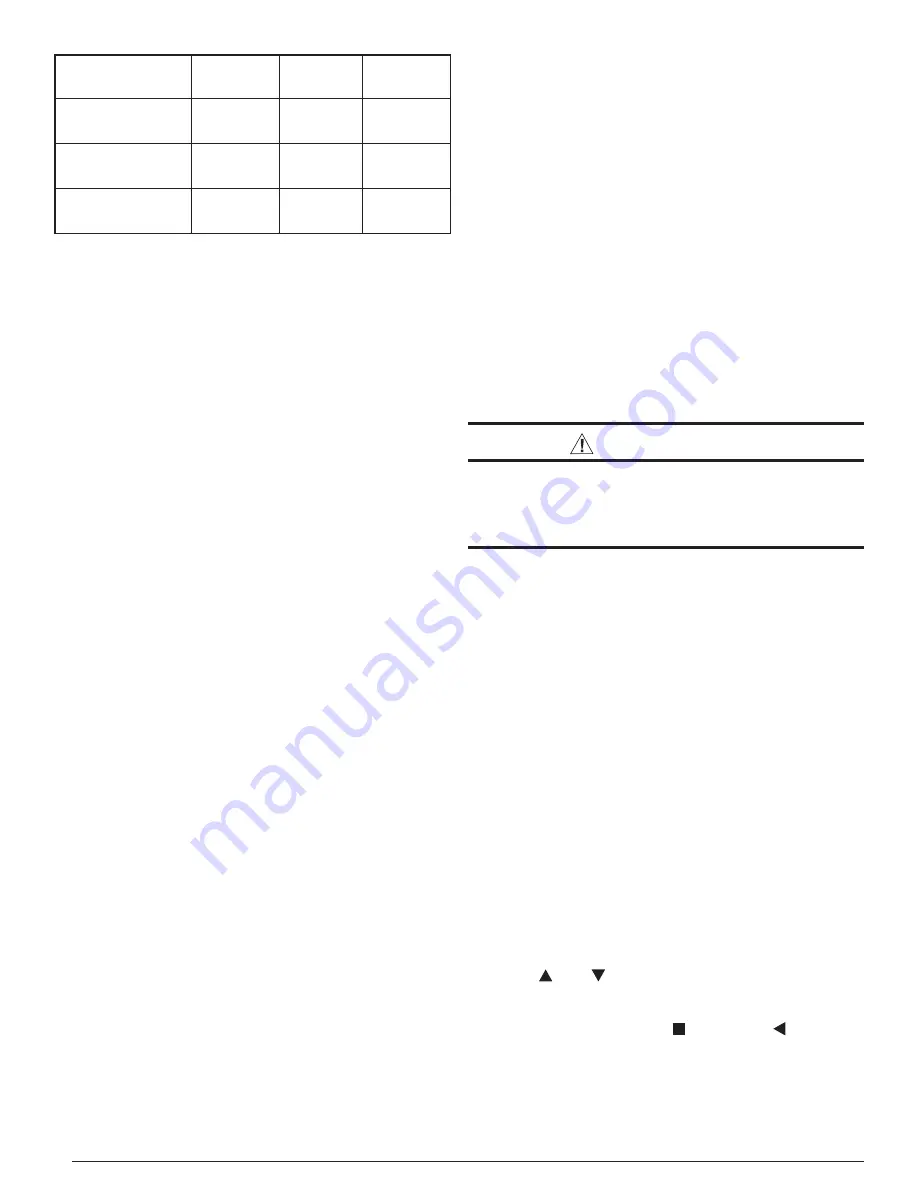
6
MODEL:
2 TON
(-024K)
3 TON
(-036K)
4 TON
(-048K)
Factory Charge
(for 15 ft. line set)
10.0 lbs
(160 oz)
10.5 lbs
(168 oz)
11.8 lbs
(188 oz)
Additional Charge
for 50 ft. line set
+ 1.1 lbs
(18 oz)
+ 1.1 lbs
(18 oz)
+ 1.1 lbs
(18 oz)
Additional Charge
for 100 ft. line set
+ 2.8 lbs
(44 oz)
+ 2.8 lbs
(44 oz)
+ 2.8 lbs
(44 oz)
Table 4. Refrigerant Charge Quantities
Alternate Procedure for Charging Heat Pump in
Cooling Mode (with outdoor temperatures above
60 °F) Based on Subcooling:
While charging based on weight is preferred, this method is
acceptable. Use this method when the outdoor temperature
is 60°F or higher to verify the correct charge in cooling mode.
The indoor temperature should be between 70°F and 80°F.
1. Connect the gauge manifold to the liquid and vapor service
valves (Figure 8).
2. Start the system in CHARGE MODE, COOLING. Allow
the system to run 15 minutes to stabilize.
3. Record the liquid refrigerant pressure in psig at the service
valve.
4. Record the liquid refrigerant temperature in °F at the service
valve.
5. Using the temperature value recorded, determine the
corresponding liquid refrigerant pressure from the upper
curve (for cooling) in the charging chart (Figure 9).
6. If the pressure measured in step 3 is less than the required
liquid refrigerant pressure determined in step 5, then
refrigerant needs to be added.
7. If the pressure measured in step 3 is greater than the
required liquid refrigerant pressure determined in step 5,
then the system is over-charged.
8. Add or remove charge from the system depending on the
measurements recorded. Allow the system to stabilize for
15 minutes before taking the next readings.
Alternate Procedure for Charging Heat Pump in
Heating Mode (with outdoor temperatures below
60 °F) Based on Subcooling:
Use this method when the outdoor temperature is 60°F or
lower to estimate the correct charge in heating mode. The
indoor temperature should be between 65° F and 75° F.
The preferred method of charging is by weighing in the
additional refrigerant required. If a charging scale is not
available, the correct charge can be estimated by this method.
Refrigerant can be stored in the receiver and accumulators
and result in an over-charged system. If it is necessary to
use this method, follow up service should be scheduled when
the temperature is above 60°F, and then charge should be
verifi ed in cooling mode.
1. Connect the gauge manifold to the liquid service valve and
suction service port located at the left side of the access
panel above the liquid service valve. See Figure 8.
2. Start the system in CHARGE MODE, HEATING. Allow the
system to run 15 minutes to stabilize.
3. Record the liquid refrigerant pressure in psig at the service
valve.
4. Record the liquid refrigerant temperature in °F at the service
valve.
5. Using the temperature value recorded, determine the
corresponding liquid refrigerant pressure from the lower
curve (for heating) in the charging chart (Figure 9).
6. If the pressure measured in step 3 is less than the required
liquid refrigerant pressure determined in step 5, then
refrigerant needs to be added.
7. If the pressure measured in step 3 is greater than the
required liquid refrigerant pressure determined in step 5,
then the system is over-charged.
8. Add or remove charge from the system depending on the
measurements recorded. Allow the system to stabilize for
15 minutes before taking the next readings.
SYSTEM SETUP USING THE IQ CONTROLLER
IMPORTANT:
It essential that the wires meant to provide 24 volts
to the outdoor unit are not mistakenly connected to
the communication terminals. Check again before
you apply power!
General
Power up the entire system with the iQ controller (thermostat)
installed in its base. The controller will be of use to the installer
for the following general purposes:
• Confi guring the system using INSTALLER SETTINGS
screens (required)
• Running system service tests (recommended)
• Using service information screens to examine and diagnose
system operation (very helpful, if needed)
• Setting options and features which are not typically used
or understood by the homeowner (recommended)
• Setting options and features with the homeowner’s oversight
in an effort to train him/her (suggested)
The following descriptions of the controller apply specifi cally
to software Version 5.0. A summary of the controller menu
structure is provided in Figures 10 & 11. NOTE: This guideline
is not intended to be a comprehensive substitute for proper
iQ Drive system training (required).
Screen Navigation
Moving between option categories on menu screens or
moving between possible values for any one option is done
using the and keys. The line or value with a dark
background behind the characters is considered “selected”.
In order to change a selected option in most screens, or to
save a changed value, use the key. Use the key to back
up into the previous screen in the menu/screen structure.
The Main Screen
The Main Screen is the normal display viewed on the
controller. It prominently shows room temperature and