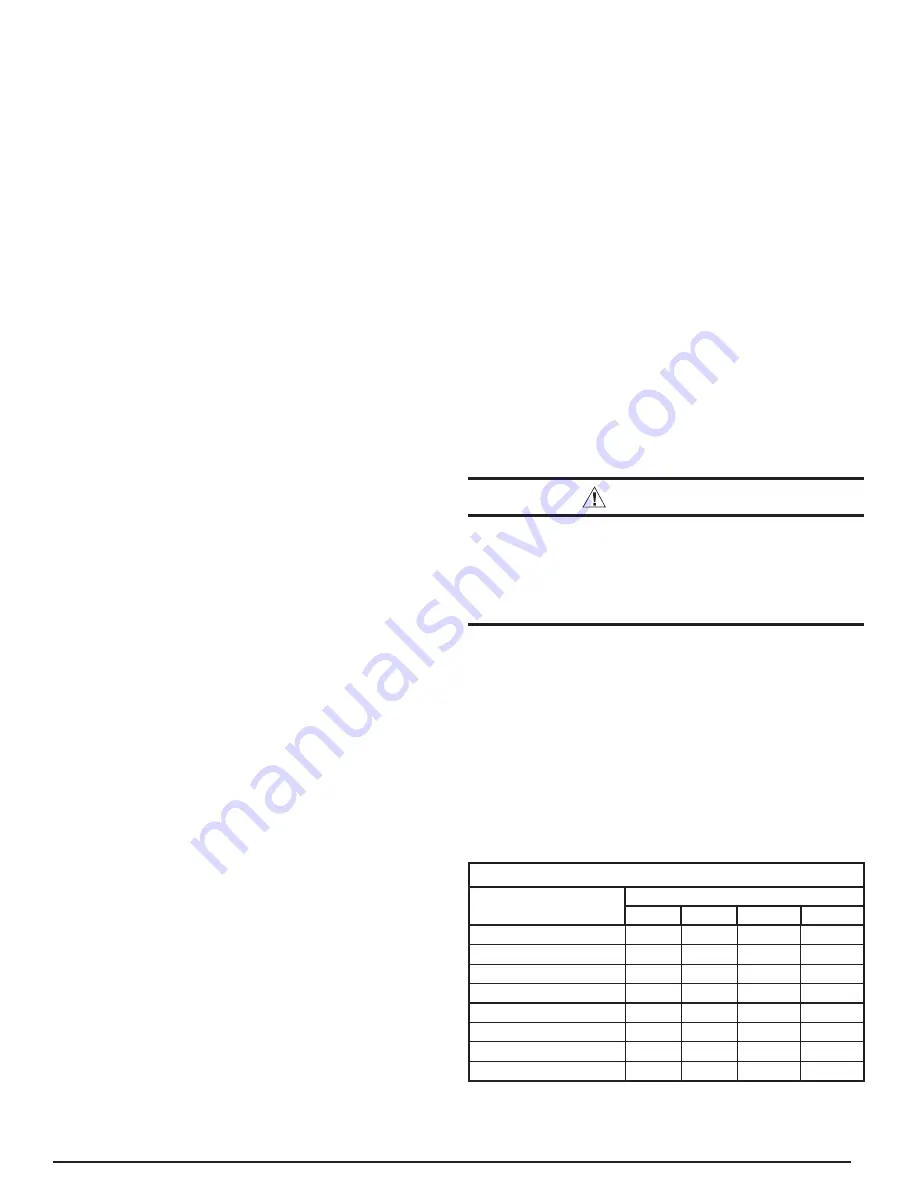
3
PREPARATION
Before proceeding with installation of iQ heat pump equipment,
consult with the distributor and homeowner to confi rm that the
equipment listed on the order is what was ordered, and that
it matches labeling on the equipment packaging.
Next determine (including consultation with the homeowner) the
intended/preferred location for placement of the compressor/
outdoor coil unit. Unit envelope dimensions are shown in
Figure 1.
This heat pump is designed for outdoor installation only.
Unit placement must take into consideration the following
clearances: (a) A minimum of 18 inches must be provided
between each of the four sides and any solid barrier or wall
which might block free inlet air fl ow into the coil. A minimum
clearance of 36 inches is required between multiple units.
(b) The corner of the unit covered by the control access
cover must be clear enough to allow comfortable access by
a serviceperson. (c) The top of the unit must be open and
unobstructed to prevent recirculation of outdoor fan discharge
air, particularly for air conditioning usage. A minimum distance
of 4 feet overhead clearance is recommended. Do not locate
the unit in a pit with high walls on all sides.
Locate the unit away from overhangs which would allow water
runoff or ice to fall directly onto the heat pump. Avoid placing
the unit near sidewalks or walkways to avoid possible icing
from defrost cycles. In low temperature climates, place the
unit where it is not directly in prevailing winds. Avoid placing
the heat pump near sleeping quarters or windows. As the unit
goes through defrost cycles, a change in sound will occur.
Slab Mounting
The preferred unit mounting is on an outdoor slab (concrete
or plastic), on the ground, in an area with good drainage
unlikely to be affected by heavy runoff, ground settling, or deep
snowdrift accumulation. The support slab should be level. If
the area is subject to heavy snowfall or drift accumulation, the
use of a snow stand is recommended as well. Make sure that
the drain holes in the bottom of the unit are not obstructed.
Roof Mounting
The method used for roof mounting should be designed so
as not to overload roof structures nor transmit noise to the
interior of the structure. Refrigerant and electrical lines should
be routed through suitably waterproofed openings to prevent
leaking into the structure. Make sure that the roof structure
can adequately support the weight of the equipment. Consult
local building codes for rooftop installations.
After a location has tentatively been selected, trace routing
of new (or pre-existing) refrigerant lines (two), and power and
control wiring. See further discussion below.
• Maximum recommended length for refrigerant lines: 100 ft.
• Maximum elevation difference, compressor base to indoor
coil base (compressor higher): 50 feet NOTE: An oil trap
is required for elevations exceeding 50 feet.
• Maximum elevation difference, compressor base to indoor
coil base (compressor lower): 50 feet NOTE: An oil trap is
required for elevations exceeding 50 feet.
• Refrigerant lines should NOT be buried. (in concrete or
otherwise)
• Refer to Nordyne Application Guideline for Refrigerant Lines
Over 75 Feet document 044B-0600, for piping details
Once the above information has been confi rmed and potential
questions regarding location, refrigerant line routing, and
wire routing have been resolved, proceed with unpacking the
equipment. It is strongly recommended that inspection of the
hardware be performed prior to bringing it to the installation
site. Inspect for cosmetic as well as functional damage (such
as obvious holes or gaps in tubes and joints, cut or pinched
wires or wire insulation).
Verify that the iQ Drive
®
heat pump unit package includes the
following:
• Coil/compressor/control unit.
• Packet containing installation instructions and one fi lter-drier.
NOTE: The thermostat/controller which is required for
system operation is part of a separately purchased kit.
ELECTRICAL CONNECTIONS
WARNING:
ELECTRIC SHOCK HAZARD
Disconnect all electrical power at main circuit box
before wiring electrical power to the outdoor unit.
Failure to follow these instructions may result in
electric shock or death.
Electrical Power Wiring
Electrical power wiring shall comply with the current
provisions of the National Electrical Code (ANSI/NFPA 70) as
supplemented by applicable local building codes. The installer
should become familiar with the wiring diagram before making
electrical connections to the outdoor unit. An equipment
wiring diagram is included in this instruction and inside the
unit control panel cover. Refer to the unit rating label located
on the exterior of the control box cover for operating voltage,
minimum circuit ampacity, and maximum fuse size. See Table
I for wire sizing.
COPPER WIRE SIZE - AWG (1% Voltage Drop)
Supply Circuit Ampacity
Supply Wire Length - Ft
up to 50
51 - 100
101 - 150
151 - 200
15
14
10
8
6
20
12
8
6
4
25
10
8
6
4
30
10
6
4
4
35
8
6
4
3
40
8
6
4
3
45
6
4
3
2
50
6
4
3
2
Wire Sized based on N.E.C. for 60°C type copper conductors
Table 1. Copper Wire Ampacity Tables