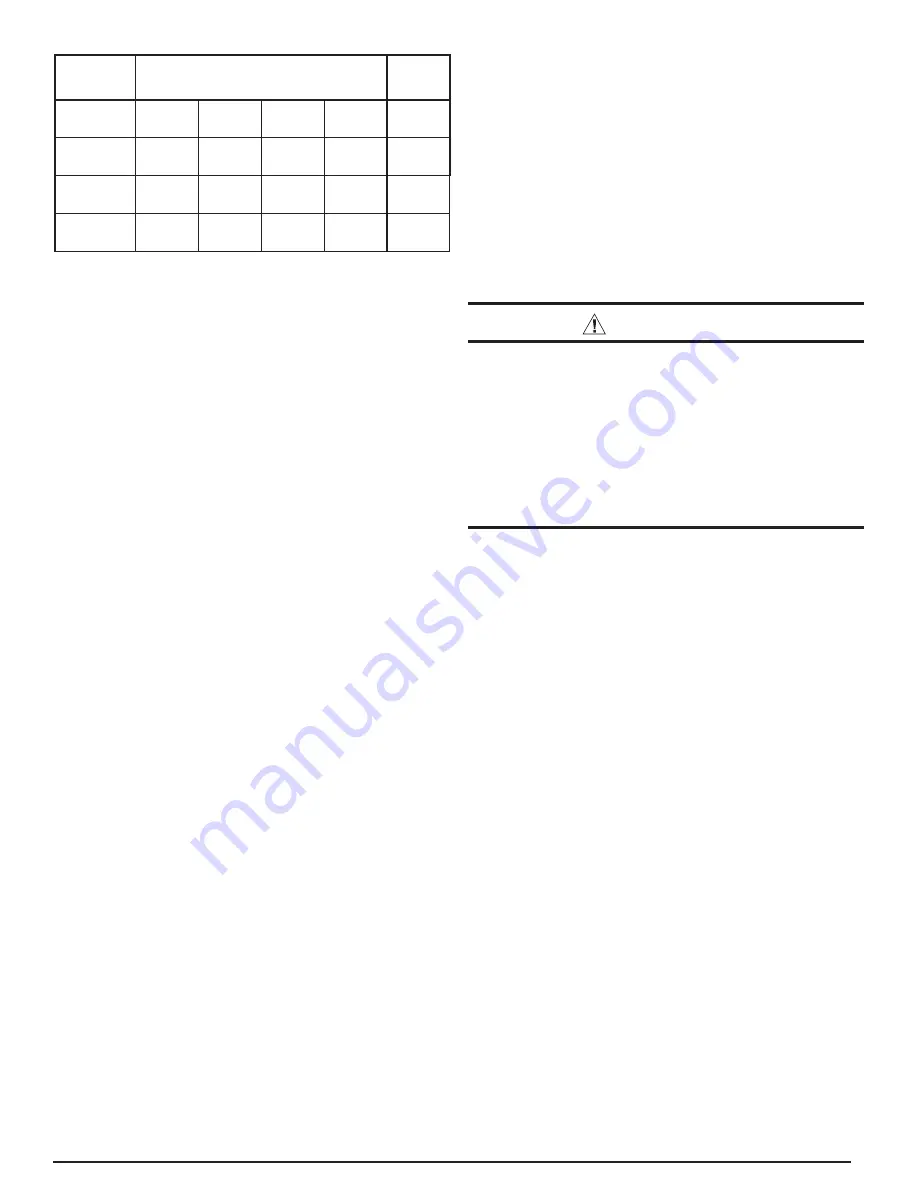
5
Vapor Line
Liquid
Line
Line Set
Length
up to 24 ft. 25 to 39 ft. 40 to 75 ft.
75 to 100
ft.
up to 100
ft.
-024K Units
3/4 in.
(19 mm)
3/4 in.
(19 mm)
7/8 in.
(22 mm)
1 1/8 in.
(29 mm)
3/8 in.
(10 mm)
-036K Units
7/8 in.
(22 mm)
7/8 in.
(22 mm)
1 1/8 in.
(29 mm)
1 1/8 in.
(29 mm)
3/8 in.
(10 mm)
-048K Units
7/8 in.
(22 mm)
1 1/8 in.
(29 mm)
1 1/8 in.
(29 mm)
1 1/8 in.
(29 mm)
3/8 in.
(10 mm)
Table 3. Permissible Refrigerant Line Sizes
The maximum vertical elevation between the heat pump and
indoor coil is 50 ft. Systems that require more elevation will
need to have an oil trap installed in the vapor line. Refer to
Nordyne Application Guideline for Refrigerant Lines Over 75
Feet (document 044B-0600) for piping details.
A fi lter drier is supplied with the heat pump. It is required and
recommended that it be installed near the indoor coil.
It is recommended to replace existing refrigerant lines that
were previously used for an R-22 system. If the lines are not
replaced, they must be properly fl ushed by a licensed EPA
certifi ed technician in accordance with the manufacturer’s
instructions and established procedures.
Brazing
Use the appropriate safety equipment while brazing. Items
such as gloves, safety glasses, proper ventilation, and a fi re
extinguisher should be used.
1. Route the refrigerant lines from the indoor coil to the service
valves on the heat pump. Avoid sharp radius bends and
turns.
2. Make sure that the vapor line is properly insulated for the
entire length of the run for maximum system effi ciency.
Improper insulation may also create condensation and result
in water damage to the equipment and building structure.
3. Remove the valve cores from the heat pump service valves.
Wrap the valves completely with wet rags to protect them
from overheating during the brazing operation.
4. Connect both the vapor and liquid lines. Tubes should be
round, de-burred and free of debris. Use a phosphorous
and copper or silver brazing alloy for the joints. Do not use
soft solder with a low melting point.
5. Connect the indoor lines according to the indoor unit
instructions. The indoor coil will require the same alloys
and wet rags to protect the sensors from excessive heat
on the refrigerant lines.
6. Allow the service valves to cool and replace the valve cores.
7. Leak test the connections using low pressure dry nitrogen.
System Evacuation
1. Connect the refrigerant gauge manifold to both the vapor
and liquid service valves. See Figure 8. Connect the center
port to the vacuum pump.
2. Open both manifold valves and start the vacuum pump.
After a short time, it is recommended to close the manifold
valves and stop the vacuum pump to look for a rapid loss
of vacuum. Loss of vacuum indicates that there is a leak
in the system. Repeat the leak test if required.
3. Evacuate the system to at least 500 microns to remove
non-condensables and water vapor. Close the manifold
valves and remove the vacuum pump.
4. Connect the refrigerant tank to the center manifold port of
the gauge set. Pressurize the system enough to break the
vacuum.
5. Open both service valves by turning the valve stems ¼
turn counterclockwise. The stem will be in line with the
tubes. Replace the stem caps and tighten. Proceed with
Refrigerant Charging section.
WARNING:
The heat pump system contains liquid and
gaseous refrigerant under pressure. Adjustment
of refrigerant charge should only be done by a
qualifi ed, EPA certifi ed technician thoroughly
familiar with this type of equipment. Under no
circumstances should the homeowner attempt to
install and/or service this equipment. Failure to
comply with this warning could result in equipment
damage, personal injury, or death.
Refrigerant Charging
NOTE: The unit must be charged at a fi xed speed setting.
or this purpose the thermostat/controller needs to be wired
and powered prior to charging. Using the thermostat, go
to CHARGE MODE under SERVICE TESTS from the
INSTALLER SETTINGS menu, described later in this
document. Select CHARGE MODE to add or verify system
charge. In the CHARGE MODE screen, HEATING or
COOLING mode may be selected, depending upon which
mode of operation is more appropriate or convenient at the
time of charging.
NOTES:
• The heat pump is factory charged for fi eld installed lines 15
ft. in length with the matching indoor equipment. Adjustments
to the refrigerant charge will be required for other length
and tube sizes. For lines longer than 15 ft with a 3/8” OD
liquid line, add 0.52 oz. per ft.
• Small variations in the temperatures and pressures are
normal due to differences in the installation.
• Large variations in the temperatures and pressures
could indicate incorrect charge or another problem with a
component in the system.
The preferred method of charging is by weighing in the
additional refrigerant required. If a charging scale is not
available, the next preferred charging method would be to
use the sub-cooling method in cooling mode.