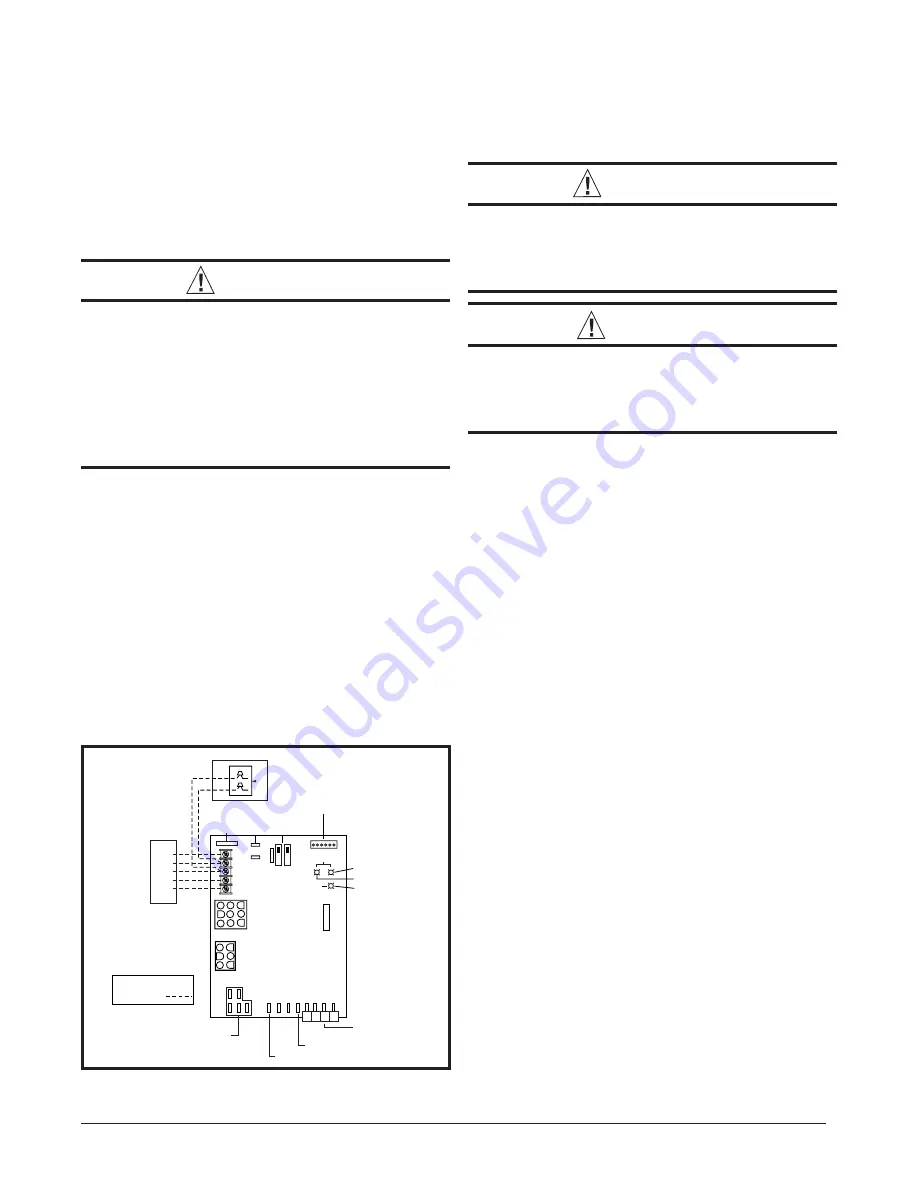
13
When deration is completed, it is required that you measure
the gas input rate. This may be accomplished in the usual
way, by clocking the gas meter and using the local gas
heating value.
NOTE:
It will be necessary to check the
input rate using the actual heating value, (which will be
less) because the atmospheric pressure is also lower
than sea level. See Verifying and Adjusting the Input Rate
(page 15).
Conversion to LP/Propane
WARNING:
The furnace was shipped from the factory
equipped to operate on natural gas. Conversion
to LP/propane gas must be performed by
qualifi ed service personnel using a factory
supplied conversion kit. Failure to use the
proper conversion kit can cause fi re, explosion,
property damage, carbon monoxide poisoning,
personal injury, or death.
Conversion to LP/propane is detailed in the installation
instructions provided with the conversion kit. Generally,
this will require the replacement of the burner orifi ces and
the spring found under the cap screw on the pressure
regulator.
The LP/Propane Gas Sea Level and High Altitude
Conversion Kit (P/N 904923) is an approved conversion
kit for LP/propane conversion at altitudes between zero
and 10,000 ft. above sea level. If the installation is above
2,000 ft., refer to Table 9 (page 26) to determine the correct
orifi ce size and manifold pressure. When conversion is
complete, verify the manifold pressure and input rate are
correct as listed in Table 9.
Please
follow the instructions
provided with the kit
.
ELECTRICAL WIRING
Electrical connections must be in compliance with all
applicable local codes. For electrical requirements, refer
to Table 2 (page 14) or the furnace nameplate.
WARNING:
To avoid electric shock, personal injury, or death,
turn off the electric power at the disconnect
or the main service panel before making any
electrical connections.
CAUTION:
Label all wires prior to disconnection when
servicing controls. Wiring errors can cause
improper and dangerous operation. Verify
proper operation after servicing.
NOTE:
If replacing any of the original wires supplied with
the furnace, the replacement wire must be copper wiring
and have a temperature rating of at least 105° F (40° C).
Low Voltage Wiring
The thermostat must be installed according to the
instructions supplied by the thermostat manufacturer. The
thermostat must not be installed on an outside wall or
any other location where its operation may be adversely
affected by radiant heat from fi replaces, sunlight, or lighting
fi xtures, and convective heat from warm air registers or
electrical appliances.
Low voltage connections (24 VAC) from the thermostat
are wired to the terminal strip on the integrated control
in the furnace. See Figure 11 for proper connections for
heating only (two-wire) and heating/cooling (four-wire)
applications. Recommended minimum wire gauge for
thermostat wiring is shown in Table 2.
NOTE:
Set the heat anticipator according to the instructions
supplied by the thermostat manufacturer.
To determine the
heat anticipator setting, perform the following steps:
1. Add the current draw of the system components; or
2. Measure the current fl ow on the thermostat
R
-
W
circuit
after the circulating blower motor has started.
Line Voltage Wiring
It is recommended that the line voltage (230 VAC) to
the furnace be supplied from a dedicated branch circuit
containing the correct fuse or circuit breaker for the
furnace (Table 2).
IMPORTANT NOTES:
An electrical disconnect must be installed readily
accessible from and located within sight of the
furnace. Any other wiring methods must be acceptable
to authority having jurisdiction.
Figure 11. Low Voltage Field, Four-wire
Heating/Cooling Applications
RCY
G
W
STATUS
FLAME
GREEN
RED
180
COOL
HEA
T
120
90
60
YELLOW
BLOWER
OFF
DELAY
LO
W
ML
MH
HIGH
EA
C
L1
XFMR
HUM
COM
SPEED
SELECT
3 AMP
FUSE
24V
5
NEUTRALS
ROOM
THERMOSTAT
A/C CONDENSING UNIT
CONDENSING UNIT
CONTROL BOX
EXPANSION PORT
(MOTOR CONNECTION)
FIELD WIRING
LOW VOLTAGE
CONNECTION
R
C
Y
G
W
NOTE: The “Y” terminal
on the control board
must be connected to
the thermostat for
proper cooling mode
operation.
Connect
R & W
For Heating
Only
2
ELECTRONIC AIR CLEANER
MOTOR SPEED TAPS
(NOT USED)
HUMIDIFIER TAP
NEUTRAL LEADS
6
3
4
1
7
8
9
5
2
6
3
4
1
FA
N
Summary of Contents for G7XA Series
Page 2: ...2...