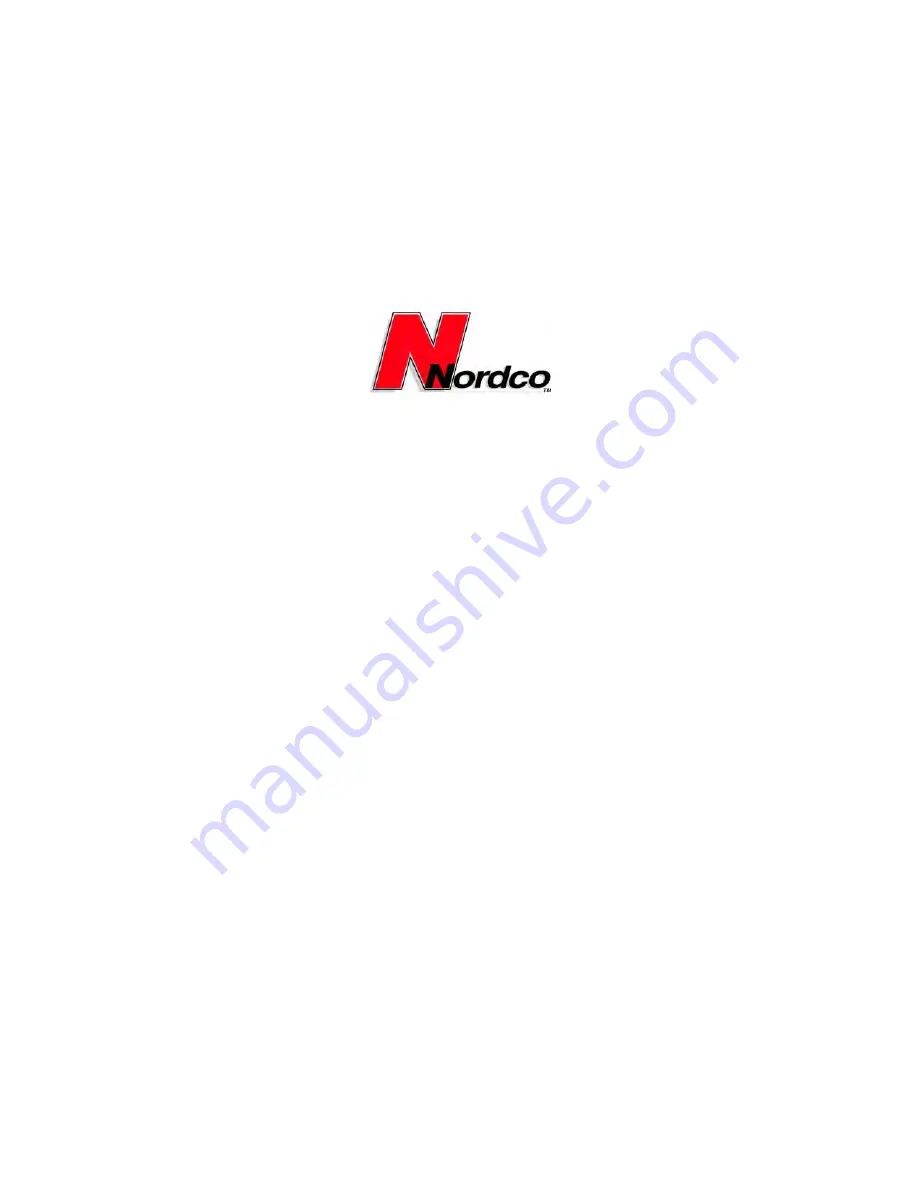
HAZARDOUS MATERIAL DATA
In an effort to provide information necessary for your employee safety training program and to meet the
requirements of OSHA Hazard Communication Standard 1910.1200, we have OSHA Form 20 Safety Data
Sheets available that cover the material contained in this machine.
If you are interested in receiving this information, please refer to the Name, model, and Serial Number of
your machine when calling or writing, and direct your inquiries to:
Vice-President of Operations
NORDCO Inc.
245 W. Forest Hill Avenue
Oak Creek, WI 53154
Fax: (414) 766-2299
Phone: (414) 766-2288
Summary of Contents for Super Claws LS-2
Page 2: ......
Page 16: ...GENERAL Super Claws Model LS 2 Section 2 4 MAR 2006 4945 3500 Page Intentionally Left Blank ...
Page 76: ......