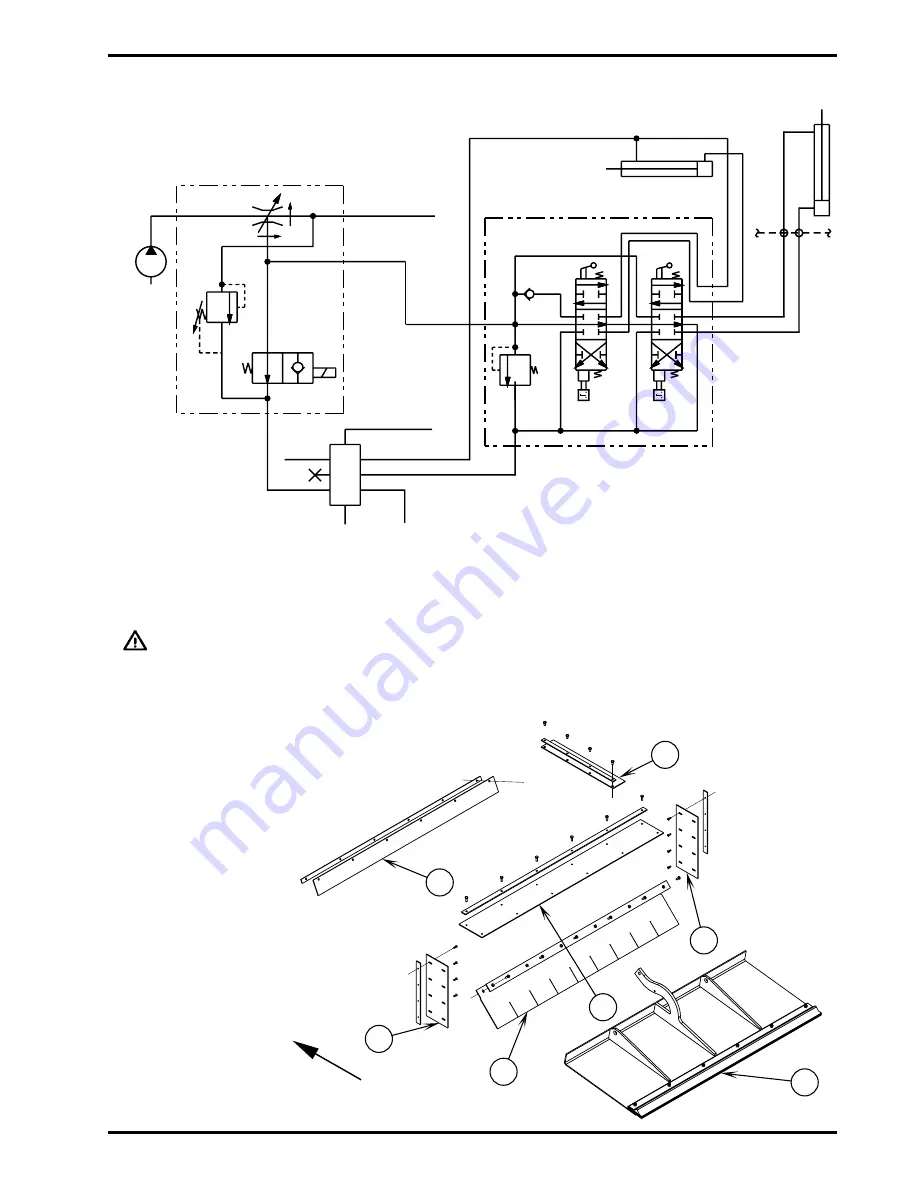
FORM NO. 56043051 / Retriever
™
2060 - 25
HOPPER SYSTEM
FRONT
B
C
E
D
A
F
C
1500
PSI
Door Cylinder
1.5 x 4.5
OPEN
6.5
GPM
To Steering Unit
Accessory
Pump
.50 CIR
Priority Divider
P
ST
DV
T
Lift Cylinder
3 x 16.5
Manifold
Directional Control Valve
T
Hopper
Lift
Dump
Door
2400
PSI
D
C
B
A
L1
Hopper System Hydraulic Diagram
________________________________________________________________________________________________________________________________________________________________________________________________________________________________________________________________________
SEALS AND SKIRTS
To access: Hopper should be empty. Raise and support the hopper, open the dump door.
WARNING!
Do not have engine running when working under hopper.
Part Number
Qty
A
56418297
1
B
56418295
1
C
56418291
2
D
56418289
1
E
56418293
1
F
56418284
2
FIGURE 1
Summary of Contents for Advance Retriever 2060
Page 87: ...4 99 Form No 56040696 page 2 A 3 B C D 5 1 2 6...
Page 94: ...6 99 revised 3 00 Form No 56040702 page 2 5 3 2 6 6 5 3 4 1 2...
Page 111: ...9 00 Form No 56040733 page 2 of 3 Diesel H FRONT M K L N R W P O T S J Q O P U V FIGURE 1...
Page 128: ...PROGRAM PURPOSE and OBJECT ZENITH FUEL SYSTEMS Page 1 1 5 48 7 0 1 2 3 4 5 0 50...
Page 133: ...ZENITH FUEL SYSTEMS Page 5 1 5 0 50 A 50 4 4 B 8 6 A C D FIG 5 1...
Page 134: ...ZENITH FUEL SYSTEMS Page 5 2 6 5 8 0 8 2 0 2 0 2 E F 0 D 50 4 C D 5 5 5 5 6 6 2 0 6 FIG 5 2...
Page 139: ...Fuel Enrichment 4 6 6 50 5 5 6 A 50 5 0 0 ZENITH FUEL SYSTEMS Page 5 7...
Page 144: ...ZENITH FUEL SYSTEMS INC Page 5 12 3F 6 6 H J 3F FIG 5 19 6 G 6 FIG 5 20...
Page 147: ...ZENITH FUEL SYSTEMS Page 6 2 A A 1 6 FIG 6 1...
Page 148: ...ZENITH FUEL SYSTEMS Page 6 3 5 2 3 0 0 1 4 4 B 6 6 6 4 4 3 6 6 6 9 6 6...
Page 149: ...ZENITH FUEL SYSTEMS Page 7 2 8 2...
Page 150: ...ZENITH FUEL SYSTEMS Page 7 3 8 2...
Page 153: ...ZENITH FUEL SYSTEMS Page 9 3...
Page 160: ...ZENITH FUEL SYSTEMS Page 9 11 6 6 9 8 2...
Page 163: ...ZENITH FUEL SYSTEMS Page 9 14 6 6 9 8 Continued...