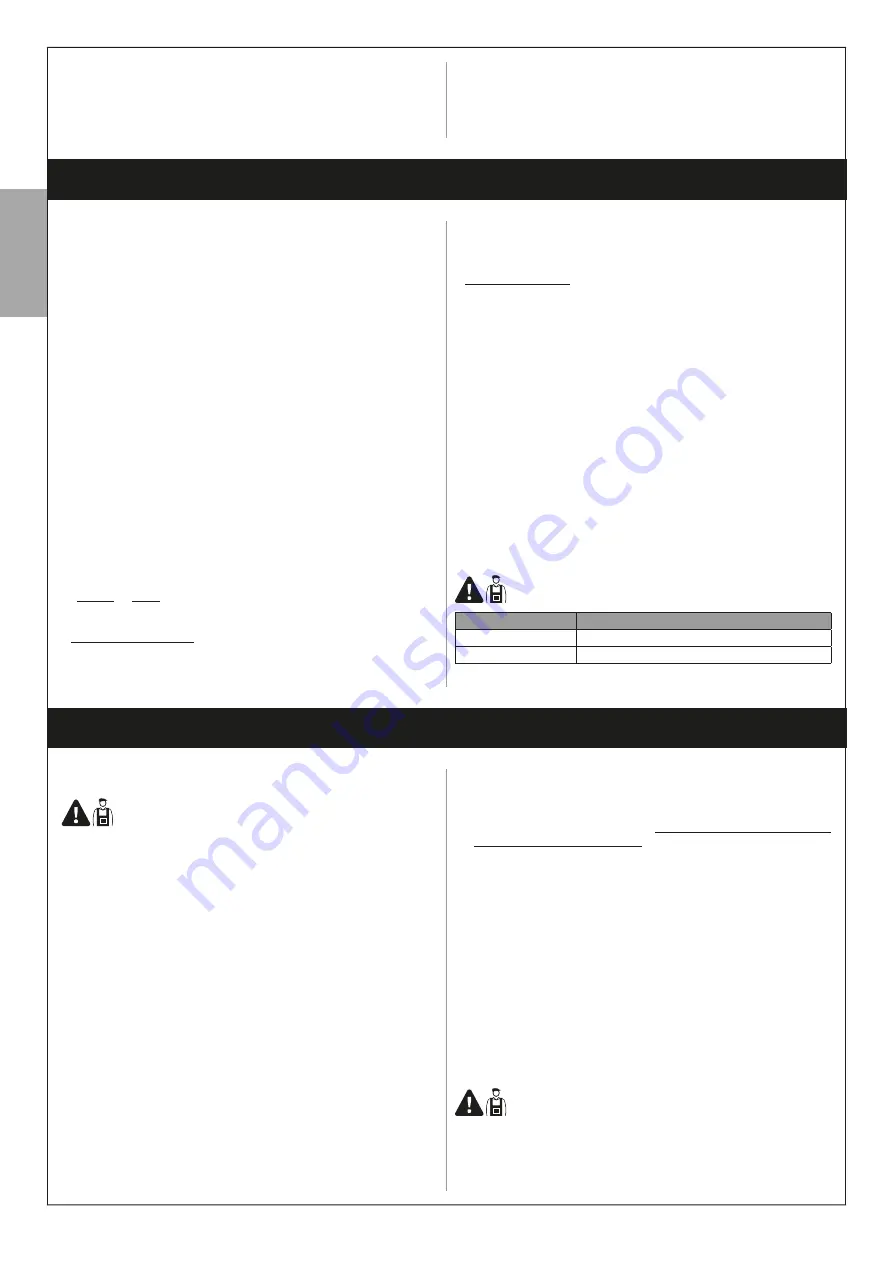
English
2
– English
INSTALLATION: COMPONENT ASSEMBLY AND CONNECTION
––– STEP 3 –––
3.1 - SET-UP FOR INSTALLATION
In
Fig. 2
there is an example of a complete installation, built with Nice
components. These parts are positioned according to a typical standard
layout.
Refer to
Fig. 2
to establish the approximate location where each
specified component is to be installed, and to decide on the layout of the
electrical connections between the components
.
Components useful for realising a complete plant (fig.
2):
A
- Electro-mechanical gear motors
B
- Control unit
C
- Pair of photocells
D
- Columns for pairs of photocells (C)
E
- Flashing signal with antenna incorporated
F
- Digital keyboard / Key selector switch
G
- Pair of mechanical stops in opening and closure
3.2 - INSTALLATION
To install the gearmotor, perform all the steps shown in the figures in the
Appendix, starting
from Fig. 1 to Fig. 18
. You must strictly follow the
order as shown.
3.3 - MANUAL RELEASE AND BLOCK OF THE
GEAR MOTOR
To release or block
the gearmotor, use the lever provided in the following
way:
• To release a gate leaf
(reference to Fig. 19):
01.
Choose the side of the leaf you want to work on.
02.
Gain access to the lock by turning its cover 180° (test it to see which
way you need to turn it).
03.
Insert the lever in the lock and turn it 180° in a clockwise direction.
04.
Remove the lever from the lock and put the cover back on the lock.
05.
Lastly, move the leaf by hand to its desired position.
•
To lock a gate leaf (reference to Fig. 20):
01.
Choose the side of the leaf you want to work on.
02.
Gain access to the lock by turning its cover 180° (test it to see which
way you need to turn it).
03.
Insert the lever in the lock and turn it 180° in an anti-clockwise direc
-
tion.
04.
Remove the lever from the lock and put the cover back on the lock.
05.
Move the leaf by hand to a position by the lock; finally release it only
after hearing the click of the lock (= door locked onto the gearmotor).
3.4 - ELECTRIC CONNECTIONS
Recommendations:
-
The gearmotor must only be connected to the
CL2SL
control unit.
-
The gear motor is supplied with an electric power input cable measur
-
ing 3 m. So if you need to cover a greater distance in order to connect
it to the CL2SL control unit,
it is essential to use a junction box (not
supplied) to adequately protect the added sections of electrical
cable.
- Make the electric connections with the mains power input dis
-
connected.
To connect the power input cable to the control unit, see the
manual regarding the latter and the following indications:
WIRE
CONNECTION
Blu wire
24 V motor power input
Brown wire
24 V motor power input
refer to a gate leaf with closed surfaces up to 20% of the total out
-
line. For leaves with more than 20% of closed surfaces, the maximum
weight and length values are reduced in proportion to the increased
percentage of closed surfaces.
• The gearmotor must only be connected to the
CL2SL
control unit.
•
Since the gearmotor must be installed inside the gate leaf, the leaf upright
(in which the rotation fulcrum is located) must be a hollow metal profile
with a housing space equal to or greater than a diameter of 56 mm.
• It is
imperative to install mechanical stops at the preset points for the
opening and closing limit switches (
fig. 1
–
these accessories are not
included).
INSPECTION AND COMMISSIONING
––– STEP 4 –––
ATTENTION! – The operations described in this chap-
ter must only be performed by qualified and skilled
staff, respecting the instructions in the manual, the
laws and the Safety Standards in force on the territory.
This is the most important phase in the realisation of the automation, in
order to guarantee maximum safety of the system. The inspection pro
-
cedure described can also be used to periodically check the devices that
make up the automation.
The inspection phases and commissioning of the automation must be
performed by qualified and expert staff that must establish the tests nec
-
essary to check the solutions used regarding the risks present and to
check respect with that envisioned by the Laws, Standards and Regula
-
tions: particularly, all requisites of the EN 13241-1 Standard, which estab
-
lishes the test methods for checking the gate automations.
ATTENTION! – Before carrying out any check, disconnect any
electrical power input source.
4.1 - INSPECTION
Each individual component of the automation, e.g. sensitive edges, pho
-
tocells, emergency stop etc requires a specific inspection phase. For
these devices the procedures given in the respective instruction manuals
must be performed
. When conducting tests on the gearmotor, proceed
as follows:
1
Check that everything envisioned in Chapter 1 - General safety warn
-
ings and precautions, is rigorously respected
.
2
Close the gate.
3 Remove any electric power input source to the control unit.
4
Release the gear motor using the relative wrench (see
paragraph 3.3
).
5
Move the gate leaf by hand to its maximum opening position; dur
-
ing movement
make sure there is minimum friction and that constant
force is used throughout the travel: there must be no points where the
friction is greater than elsewhere
.
6
Move the gate leaf by hand and leave it still at various points along its
travel; then make sure that the gate leaf remains in balance, i.e. it does
not move.
7
Make sure that the safety systems and mechanical stops are in good
condition.
8
Make sure that the screw terminals used for the electrical connections
are tight.
9
Block the gear motor using the relative wrench (see
paragraph 3.3
).
10
Apply the electric power input to the control unit.
11
Measure the force of impact according to that envisioned by the EN
12445 Standard. If the control of the “driving force” is used by the
control unit as an auxiliary to the system for the reduction of the force
of impact, try and adjust the functions that offer better parameters.
12
Place the label showing how to manually release and relock the gear
-
motor in a position close to the automated unit.
4.2 - COMMISSIONING
Commissioning can only be performed after all of the in
-
spection phases of the gear motor and other devices pre
-
sent have been performed with positive results. For commis
-
sioning refer to the control unit instruction manual.
IMPORTANT – Partial commissioning or in “temporary” situations
is prohibited
.
Summary of Contents for MhouseKit WI1
Page 5: ...IV rotation axis open close 13 14 15 17 16 18...
Page 6: ...V 2 1 3 4 1 2 3 5 CLICK 4 19 20...
Page 23: ......