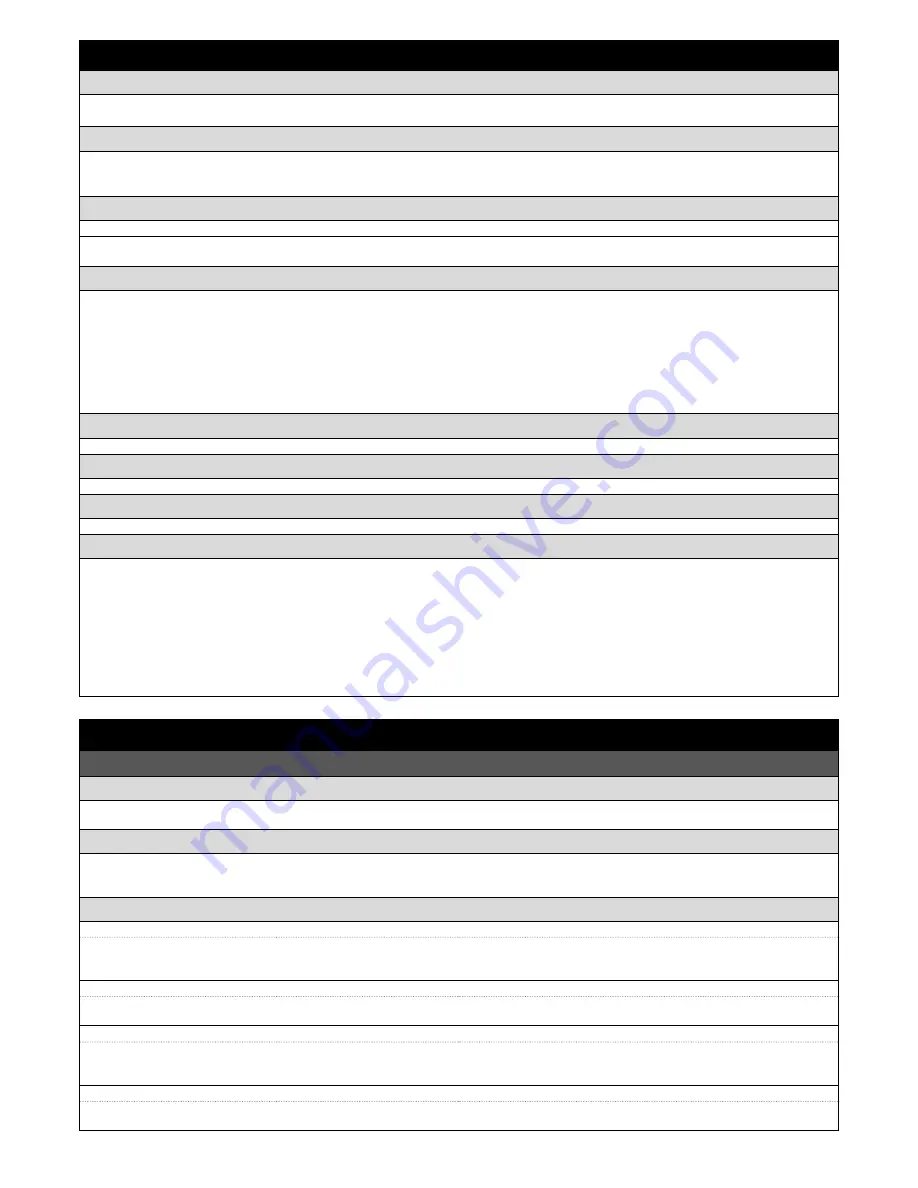
COMMON FUNCTIONS
name
This parameter enables the user to assign the automation with a name other than the original, to facilitate identification (e.g. “northern gate”).
A name comprising maximum 24 characters, including spaces, is admitted.
series
This parameter can be set with a value from 0 to 63; the factory setting is “0”.
The series is a number that has to be assigned to each gearmotor, receiver or other device potentially connectable on a BusT4 network, to define its “clas-
sification area”. Subsequently, when using automations in a complex system, all devices with the same series number can be controlled simultaneously.
Address
This parameter can be set with a value from 1 to 128; the factory setting is “2” for Receivers and 3 for Control Units.
The address is a number that has to be assigned to each gearmotor, receiver or other device potentially connectable on a BusT4 network, to distinguish it
from other devices in a
series
. Therefore all devices within a series must have a different address from one another.
group
This parameter can be set with a value from 1 to 14, or “None”; the factory setting is “None”.
The function enables the user to assign a number to a device to be controlled (for example a gearmotor or other device potentially connectable to a BusT4
network), which enables this device to belong to a specific “command group”.
Several devices, also if belonging to different series, can form part of the same group. Up to 14 groups of devices can be created and, in particular, the same
device may be inserted in 4 different groups.
In a device network, use of this function enables:
-
simultaneous control of different devices inserted in a group, even if some of these belong to different series;
-
use of a single receiver, installed in one of the devices belonging to the group, to control all the devices belonging to this group.
Firmware version (not modifiable)
This function enables the display of the version of the firmware present in a device.
Hardware version (not modifiable)
This function enables the display of the version of the hardware present in a device.
Serial number (not modifiable)
This function enables the display of the serial number identifying a specific device. This number is different for each device, even if of the same model.
password management:
This function is useful to restrict access by unauthorised personnel to all or some of the programming functions of a device. If a device is password protected,
the user must perform the “log in” procedure to proceed with a programming session, followed by the “log out” procedure on completion of the programming
procedure.
Note – the “log out” procedure enables the user to prevent access by unauthorised personnel, by re-activating the existing password.
Caution!
– In programming the password on multiple devices (for example, on the Oview, control unit, receiver, etc.), it is advisable to use the same password for all
devices, including the Oview itself. This will avoid the need to repeat the login procedure each time the device is changed during use of Oview and the con-
nected Software.
Two types of password can be programmed on the devices (including Oview).
-
the user password, at most 6 alphanumeric characters
.
Caution!
– Do not use uppercase letters.
-
the installer password, at most 6 alphanumeric characters
.
Caution!
– Do not use uppercase letters.
CONTROL UNIT FUNCTIONS
Installation
Bluebus search (0x0a)
This function enables start-up of the procedure for learning the devices connected to the Bluebus input and the HALT input of the control unit of an automa-
tion.
Important
– To activate the device search, press “Start”.
Position search
This function enables the measurement of the distance between the Closing limit position and Opening limit position (pole travel). This measurement is used
by the control unit to ensure the calculation of the points at which the pole must start to decelerate during a manoeuvre and to determine the partial opening
position.
Important
- To activate the position search, press “Start”.
Position programming
• reverse rotation (0xa3)
This parameter type is ON/OFF; the factory setting is “OFF” (standard motor rotation; the factory setting for pole rotation is to the left). This function enables
the user to program the direction of motor rotation on an automation; in other words it enables the inversion of the Opening manoeuvre and Closing manoeu-
vre.
Important
– If this function is enabled, the positions must be memorised anew.
• opening initial deceleration position (0x32)
This function is expressed in degrees. This enables programming the precise position at which the pole starts accelerating during an opening manoeuvre.
To save the position, press “
OK
”.
• opening deceleration (0x24)
This function is expressed in degrees. During the opening manoeuvre this enables programming of the precise position at which the pole should start decel-
erating before reaching the limit switch. To save the position, press “
OK
”.
Important
– The deceleration point also depends on the speed of the manoeuvre
and pole balancing.
• partial open 1 (0x1b)
This function is expressed in degrees. It enables you to program the position at which the pole stops moving (partial opening), during the opening manoeuvre.
To save the position, press “
OK
”.