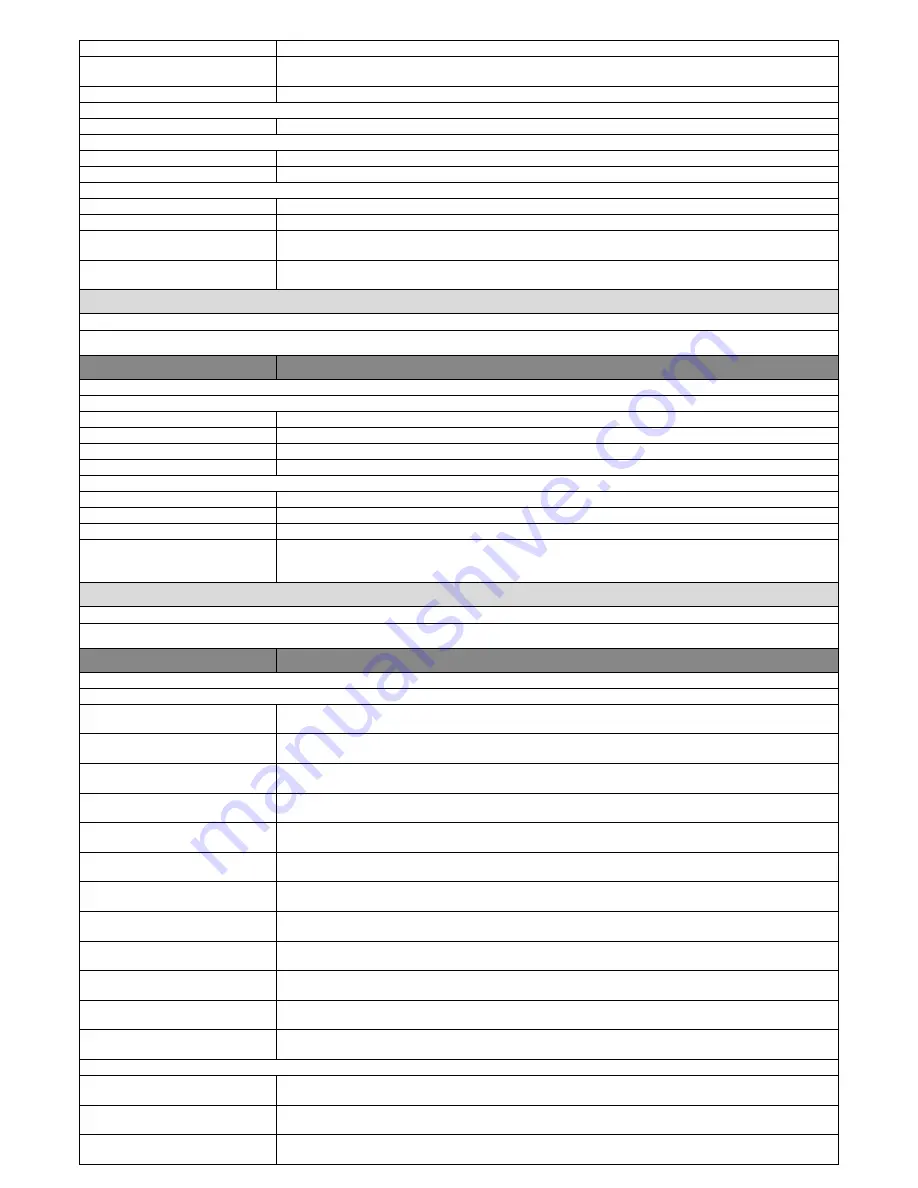
Stop
Indicates whether there is an error in the memorised data regarding the configuration of the alt input.
Bluebus
Indicates whether there is an error in the memorised data regarding the configuration of the devices connected to
the bluebus input.
Positions
Indicates whether there is an error in the memorised data regarding positions.
ENCODER STATUS:
Abs M1
Indicates whether there is a reading error or operating malfunction on the absolute encoder of motor 1.
OUTPUTS:
Out 1
Indicates when output 1 is active. Caution – 12/24 V DC voltage present.
Out M1
Indicates when motor 1 is in operation.
ALARMS:
Out 1 overload
Indicates an electrical overload or short circuit on output 1 or on the courtesy light of the control unit.
Out 2 overload
Indicates an electrical overload or shortcircuit at output 2.
M1 low overtravel
Indicates that the absolute encoder of motor 1 is in a position close to the minimum limit (0%), below which the
motor does not function.
M1 high overtravel
Indicates that the absolute encoder of motor 1 is in a position close to the maximum limit (100%), over which the
motor does not function.
other parameters
This function enables display of the operating status of some parameters measured by the control unit. These parameters are described in Table 5.
TABLE 5: DIAGNOSTICS of other parameters
PARAMETER
DESCRIPTION
• Diagnostics 2
MISCELLANEOUS PARAMETERS:
Courtesy light
Indicates the timer for shutoff of the courtesy light.
Pause time
Indicates the timer for counting the pause time between one manoeuvre and the next.
Service voltage
Indicates the voltage supplied to external devices.
Bus medium current
Indicates the current absorption of the devices connected to the bluebus output, calculated as a percentage.
MOTOR 1:
Torque
Indicates the torque generated by motor 1 during the manoeuvre, calculated as a percentage.
Speed
Indicates the speed of motor 1 during the manoeuvre, calculated as a percentage.
Voltage
Indicates the mean voltage to be supplied to motor 1 during the manoeuvre, calculated as a percentage.
Position
Indicates the physical encoder position, as a percentage: the limits implemented are the encoder minimum limit
(equal to 0 = 0%) and the encoder maximum limit (equal to 4096 = 100%). This data is useful to understand whether
the encoder is in an overtravel position, i.e. outside the operating zone of the absolute encoder.
bluebus device diagnostics
This function displays the type, operating status and configuration of devices connected ot the Bluebus output. These parameters are described in Table 6.
TABLE 6: DIAGNOSTICS of bluebus devices
PARAMETER
DESCRIPTION
• Bluebus
PHOTOCELLS
PHOTO
Indicates whether the photocell is present, the relative operating status and the correct memorisation in the control
unit.
PHOTO II
Indicates whether the photocell is present, the relative operating status and the correct memorisation in the control
unit.
PHOTO 1
Indicates whether the photocell is present, the relative operating status and the correct memorisation in the control
unit.
PHOTO 1 II
Indicates whether the photocell is present, the relative operating status and the correct memorisation in the control
unit.
PHOTO 2
Indicates whether the photocell is present, the relative operating status and the correct memorisation in the control
unit.
PHOTO 2 II
Indicates whether the photocell is present, the relative operating status and the correct memorisation in the control
unit.
PHOTO 3
Indicates whether the photocell is present, the relative operating status and the correct memorisation in the control
unit.
FT A
Indicates whether the sensitive edge is present, the relative operating status and the correct memorisation in the
control unit.
FT B
Indicates whether the sensitive edge is present, the relative operating status and the correct memorisation in the
control unit.
FT C
Indicates whether the sensitive edge is present, the relative operating status and the correct memorisation in the
control unit.
OPEN PHOTO
Indicates whether the control photocell is present, the relative operating status and the correct memorisation in the
control unit.
OPEN PHOTO II
Indicates whether the control photocell is present, the relative operating status and the correct memorisation in the
control unit.
COMMANDS:
CMD 1
Indicates whether the control photocell is present, the relative operating status and the correct memorisation in the
control unit.
CMD 2
Indicates whether the control photocell is present, the relative operating status and the correct memorisation in the
control unit.
CMD 3
Indicates whether the control photocell is present, the relative operating status and the correct memorisation in the
control unit.