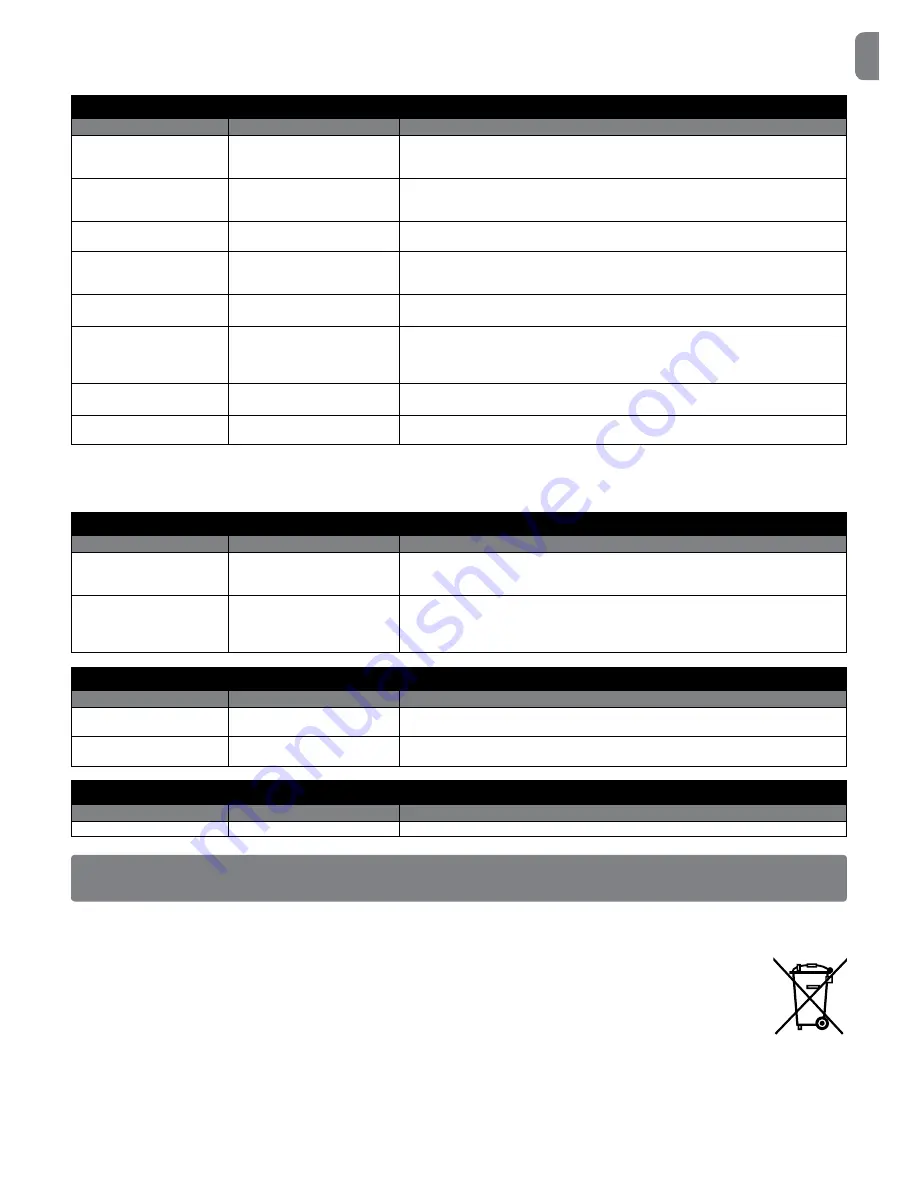
English –
11
EN
7.2 - Diagnostics
Some devices are supposed to issue warnings that allow identifying their status or any faults.
Table 6 describes the various messages with their relative causes and solutions; the warnings are based on combinations of colours, OK led flashing and a
possible, suitably programmed, flasher connected to the outputs of the control unit.
TABLE
6: OK LED SIGNALS (flashing red)
Signal
Cause
Solution
2 flashes - 1 sec. pause
2 flashes - red led
Triggering of a photocell
At the beginning of the manoeuvre, one or more photocells are preventing movement;
check if there are any obstacles.
During the closing movement it is normal if an obstacle is present.
3 flashes - 1 sec. pause
3 flashes - red led
Intervention of the “Driving
Force” or “Sensitivity” or
“Blocked Encode” limiter
While moving, the door has met with increased friction: check its cause.
4 flashes - 1 sec. pause
4 flashes - red led
Activation of the STOP input
At the start of the manoeuvre or during the movement, the STOP ALT input has been trig-
gered or the motor release lever has been activated: check the cause.
5 flashes - 1 sec. pause
5 flashes - red led
Internal parameter memorisation
error
Press the STOP button on the box lid to reset the error.
Wait for at least 30 seconds to allow the control unit to reset. If the situation does not
change, it is necessary to delete the memory and carry out the storing procedure again.
6 flashes - 1 sec. pause
6 flashes - red led
Maximum limit of manoeuvres
per hour exceeded
Wait for a few minutes to allow the manoeuvre limiter to go back below the maximum.
7 flashes - 1 sec. pause
7 flashes - red led
Error in the internal electrical
circuits
Press the STOP button on the box lid to reset the error.
Disconnect all the supply circuits for a few seconds, then try and send a command again;
if the situation does not change there may be a serious fault on the board or on the motor
wiring: check and replace as required.
8 flashes - 1 sec. pause
8 flashes - red led
Command already present
Another command is already present.
Remove the command to be able to send more.
9 flashes - 1 sec. pause
9 flashes - red led
Automation blocked
Send an automation unlocking command to reset normal operation.
Note – The diagnostic signals provided by flashing LEDs stop when the control unit is given a command.
By using an external flashing light*, the diagnostics signals continue for two sequences of flashes (e.g. “3 flashes – short pause – 3 flashes – long
pause” repeated twice).
*
Configured with the Oview programmer as “Flashing Light 1”
TABLE
7: OK LED SIGNALS (red light ON - green flashing)
Signal
Cause
Solution
Red light on
8 flashes - 1 sec. pause
8 flashes - green led
Encoder error.
No signal
Press the STOP button on the box lid to reset the error.
Check if the encoder cable has detached.
Red light on
10 flashes - 1 sec. pause
10 flashes - green led
Manoeuvre timeout.
The duration of the manoeuvre
has exceeded the one stored
during the learning phases
Press the STOP button on the box lid to reset the error.
If necessary, repeat learning the positions or change the value of the manoeuvre Time,
using the Oview programmer.
TABLE
8: OK LED SIGNALS (flashing red and green)
Signal
Cause
Solution
Alternate red - green flashing
Dip switch configuration modified Check the configuration and, if correct, confirm keeping the P1 button pressed for 2 sec-
onds
Red a nd green alternate
flashing during the manoeuvre
Force learning in progress
Carry our 4 complete manoeuvres to perform the learning of the forces required for handling.
Caution: during this phase the control unit uses maximum force.
TABLE 9: OK LED SIGNALS (flashing orange)
Signal
Cause
Solution
Fast orange flashing
Dip switch 2-B on ON
Modify the speed with the “OPEN” / “CLOSE” keys and set dip switch 2-B to OFF
8
DISPOSAL OF THE PRODUCT
This product is an integral part of the automation system, therefore it must be disposed of along with it.
As in installation, also at the end of product lifetime, the disassembly and scrapping operations must be performed by qualified personnel.
This product is made up of different types of material, some of which can be recycled while others must be disposed of. Seek information on
the recycling and disposal systems envisaged by the local regulations in your area for this product category.
Caution!
– Some parts of the product may contain pollutants or hazardous substances which, if released into the environment, may cause
serious damage to the environment or human health.
As indicated by the symbol on the left, disposal of this product in domestic waste is strictly prohibited. Separate the waste into categories for
disposal, according to the methods envisaged by current legislation in your area, or return the product to the retailer when purchasing a new
version.
Caution!
– Local legislation may envisage serious fines in the event of abusive disposal of this product.