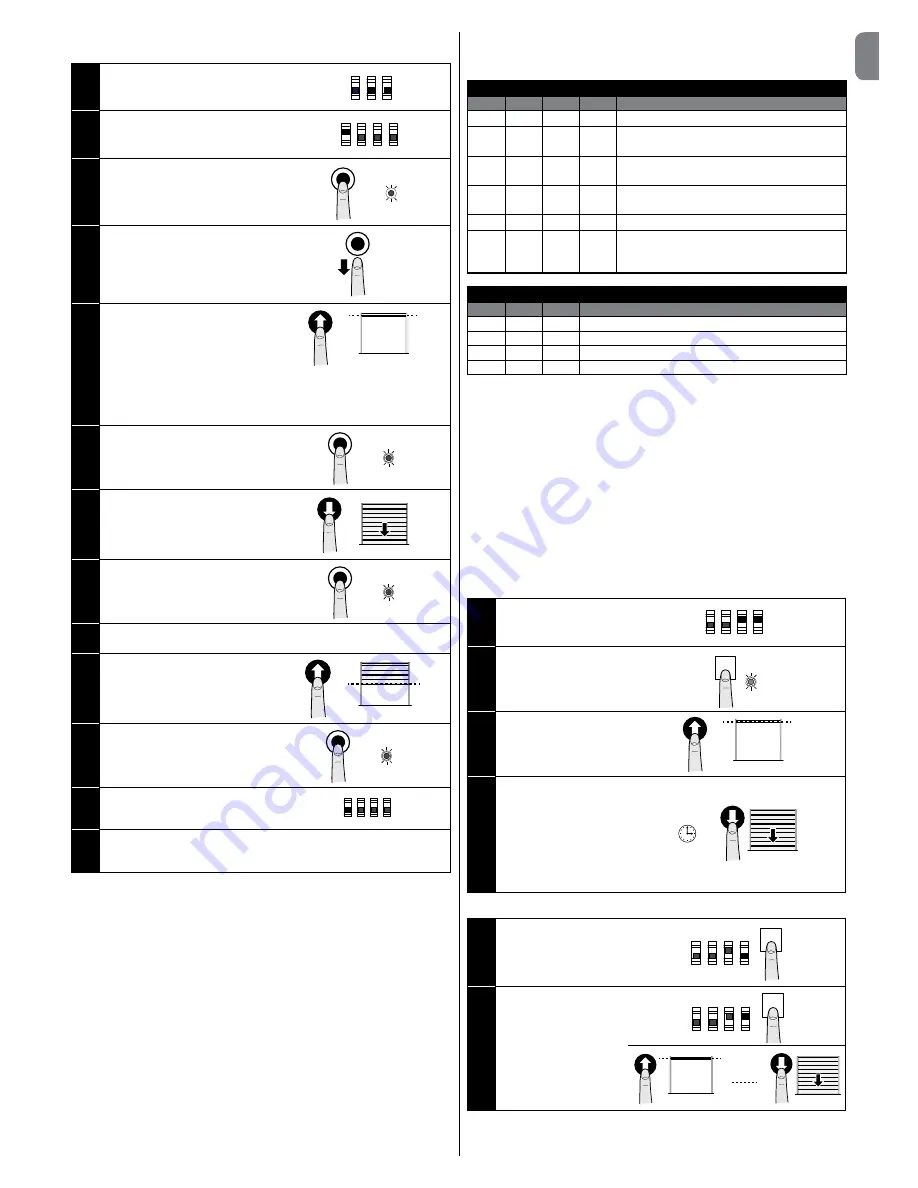
English –
7
EN
‘hold-to-run’ mode, until synchronization of the encoder position is completed.
To perform this procedure, follow the following instructions:
01.
Select the type of motor, setting
dip switches B-2 and B-3 to OFF
OFF
1
2
3
B
02.
Set dip switch A-1 to ON (A-2,
A-3 and A-4 are OFF)
OFF
1
2
3
4
ON
A
03.
Keep the STOP button pressed
until the led is on with fixed red
light (after about 3 seconds)
3”
04.
Release the STOP button
05.
Press the OPEN button to bring
the door to the desired open po-
sition
Caution!
- if the sense of rotation does not match the set direction (OPEN button =
opening direction, it is necessary to swap the positive and negative poles
of the motor cables and repeat the learning procedures from the start
06.
Keep the STOP button pressed
for 3 seconds until the led flashes
once with red light
3”
x 1
07.
Press the CLOSE button to bring
the door to the maximum closing
position
08.
Keep the STOP button pressed
for 3 seconds until the led flashes
twice with red light
3”
x 2
09.
If you do not wish to set the “partial opening” value, set dip switch A-1
or B-1 to OFF and go to step 12 of this procedure
10.
Press the OPEN button to bring
the door to the desired partial
opening position (e.g. half stroke)
11.
Keep the STOP button pressed
for 3 seconds until the led flashes
three times with red light
3”
x 3
12.
Set dip switch A-1 to OFF
ON
OFF
1
2
3
4
A
13.
Set dip switches A-3 and A-4 as per Table 3 for the desired operating
mode and confirm the setting of the dip switch with the P1 button on
the control unit
CAUTION! – The recognition phases must not be interrupted. If there is
an interruption, you must repeat the entire recognition process.
Once the position learning phase has been completed, it is necessary
to carry out learning about the handling forces: carry out 4 complete
manoeuvres; if the manoeuvre is not completed (e.g. for amp meter
intervention or stop or photo intervention) it is not counted. Until this
phase is complete, the OK led is flashing with red and green light during
the manoeuvre, THAT IS CARRIED OUT AT MAXIMUM FORCE.
Note: if the speed or slow down positions are modified or if the
sensitivity is activated, the force learning phase must be repeated.
4.5 - Operating modes
CAUTION! - If the functions of Table 3 are programmed with the Oview
programming unit, it is necessary to set the dip switches to OFF.
TABLE 3: DIP SWITCH A
DIP1 DIP2 DIP3 DIP4 Function
OFF
OFF
OFF
OFF
Hold-to-run movement
ON
X
OFF
OFF
Acquisition of positions and status of the ALT
input
OFF
ON
OFF
OFF
Rotation direction of the encoder reversed
(only for absolute encoder)
OFF
X
OFF
ON
Industrial mode (semi-automatic opening –
hold-to-run closing), if positions recognised
OFF
X
ON
OFF
Semi-automatic mode, if positions recognised
OFF
X
ON
ON
Automatic mode with adjustable pause time,
if positions recognised (see para. 4.5.1 “Set-
ting the automatic closing pause time”)
TABLE 4: DIP SWITCH B
DIP1 DIP2 DIP3 Function
OFF
X
Sensitivity disabled
ON
X
Sensitivity enabled
*
X
X
OFF
Motor with encoder
X
X
ON
Motor with electromechanical limit switch
*
Note: the sensitivity parameter allows reducing the door strength of interven-
tion against an obstacle considerably.
During the “Learning about the safety devices” procedure, the control
unit stores the status of dip switches A and B. At the end of this proce-
dure, a variation in the dip switches causes the OK led to flash quickly
with red and green light alternately to highlight the change in configura-
tion; in this phase the control unit allows no commands to be executed.
It is necessary to carry out a new “Learning about the safety devices”
procedure (paragraph 4.3) or press the P1 button for 2 seconds.
Once the positions have been acquired, it is necessary to perform 4
complete manoeuvres to get the control unit to store the force required
to move the door; the manoeuvres are represented by the OK led flash-
ing slowly with red and green light alternately.
The “force and sensitivity” parameters can be adjusted with the Oview pro-
grammer (accessory).
4.5.1 - Setting the automatic closing pause time
01.
Set dip switches A-3
and A-4 to ON
ON
OFF
1
2
3
4
A
02.
Press the P1 button for
2 seconds (the OK led
flashes with green light)
P1
OK
2”
03.
Send an opening com-
mand to bring the door
to the maximum open-
ing position
04.
Once this position is
reached, wait for a time
equal to the desired
automatic closing pause
time and send a closing
command.
The automatic closing
pause time is now
stored
4.5.2 - Modifying the pause time value
01.
Set dip switch A-4 to
OFF and confirm with
the P1 button for 2
seconds
ON
OFF
1
2
3
4
A
P1
2”
02.
Set dip switch A-4 to
ON and confirm with the
P1 button for 2 seconds
At this point the open-
ing, pause time and
closing sequence must
be repeated.
ON
OFF
1
2
3
4
A
P1
2”
CAUTION! - When dip switch A-4 is set to OFF, the pause time is can-
celled.