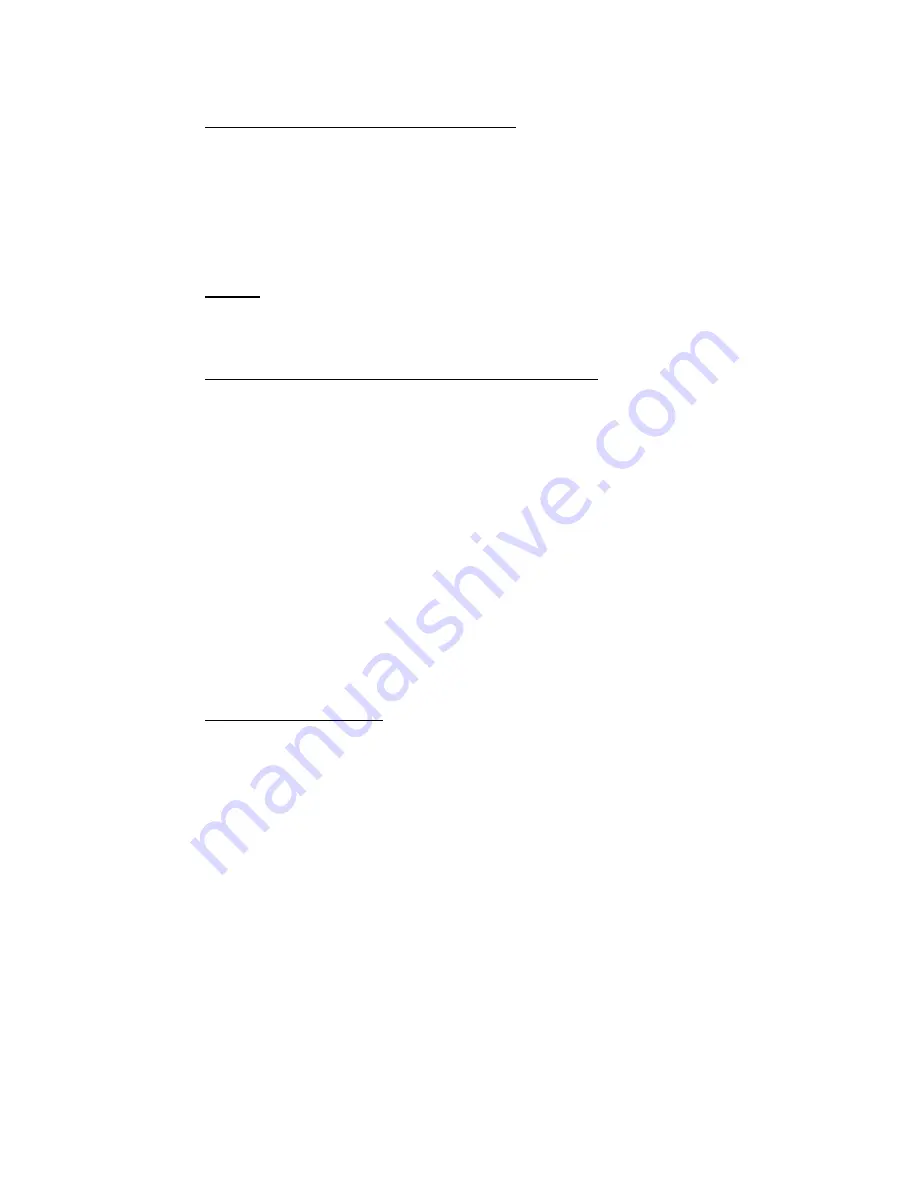
INSTALL A DOUBLE FILTER SYSTEM
Double exhaust and double inlet filters are recommended.
•
Attach a "Y" fitting to the top of the condenser with a piece of tubing. Attach
an exhaust filter on each branch. This allows you the flexibility to exchange
sterilized filters during a run should one filter become clogged, (pinch off
unused line with a clamp).
NOTE:
Fifty generations of recombinant E. coli have been propagated
by BioFlo III in continuous culture. Prolonged operation as a
chemostat
requires
double
filters.
OPERATION AS A CHEMOSTAT, SUGGESTIONS
Switch the relative positions of the antifoam and acid pumps on the console so that the
antifoam pump is now on the bottom and the acid pump is on the top.
•
"Switching" pumps is achieved by switching electrical connections in the back
of
the
unit.
•
Simply exchange the 4 plugs which go to one pump board with the 4 plugs
from the other pump board.
•
It is convenient to use the newly positioned antifoam pump as the harvest
pump, (gravity is now in your favor; a continuously filled harvest tube will
prevent
"grow
back").
•
Place L-shaped harvest tube through a side port, 3/4 of the way down to
the bottom of the vessel.
Use the antifoam probe as a level probe to actuate the harvest pump.
OTR CALCULATIONS
OTR can be estimated by titrating fixed amount of sodium sulfite, Na2SO3, with
air,
•
2SO3 + O2 CU+2 2SO4
Calibrate D.O. electrode.
•
Set zero on DO
Fully oxygenate fermentor with agitation and airflow.
•
Set span to 100%
M1226-0050 21
Summary of Contents for BIOFLO III
Page 2: ......
Page 7: ......
Page 9: ...M1226 0050 2...
Page 37: ...M1226 0050 30...
Page 40: ...M1226 0050 33...
Page 48: ...FIGURE 1 VESSEL SCHEMATIC M1226 0050 41...
Page 49: ...FIGURE 2 SAMPLING SYSTEM M1226 0050 42...
Page 50: ...FIGURE 3 FLOWMETER CONVERSION M1226 0050 43...
Page 51: ...FIGURE 4 FRONT PANEL M1226 0050 44...
Page 52: ...FIGURE 5 REAR OF CABINET M1226 0050 45...
Page 53: ...FIGURE 6 SWITCH PANEL M1226 0050 46...
Page 54: ...FIGURE 7 EXTERNAL NUTRIENT PUMP TERMINAL M1226 0050 47...
Page 55: ...FIGURE 8 SUGGESTED IMPELLER LOCATION M1226 0050 48...
Page 56: ...FIGURE 9 HEADPLATE M1226 0050 49...
Page 57: ...FIGURE 10 SPARGER TUBE M1226 0050 50...
Page 58: ...FIGURE 11 HARVEST TUBE M1226 0050 51...
Page 59: ...FIGURE 12 THERMOWELL M1226 0050 52...
Page 60: ...FIGURE 13 FOAM PROBE M1226 0050 53...
Page 61: ...FIGURE 14 BAFFLE INSTALLATION M1226 0050 54...
Page 62: ...FIGURE 15 SIDE PORTS M1226 0050 55...
Page 63: ...FIGURE 16 pH PROBE INSTALLATION M1226 0050 56...
Page 64: ...FIGURE 17 D O PROBE PHOENIX INSTALLATION M1226 0050 57...
Page 65: ...FIGURE 18 D O PROBE INGOLD INSTALLATION M1226 0050 58...
Page 66: ...FIGURE 19 CONVERSION OF D O PORT TO INOCULATION PORT M1226 0050 59...
Page 67: ...FIGURE 20 EXHAUST CONDENSER INSTALLATION M1226 0050 60...
Page 68: ...FIGURE 21 RESTRICTOR IN CONDENSER WATER IN LINE M1226 0050 61...
Page 69: ...FIGURE 22 DISASSEMBLY OF CONDENSER M1226 0050 62...
Page 70: ...FIGURE 23 FACTOR AFFECTING pH CONTROL M1226 0050 63...
Page 86: ...M1226 0050 79...
Page 87: ...FIGURE 25 BEARING HOUSING ASSEMBLY M1226 0050 80...
Page 88: ...FIGURE 26 BEARING HOUSING IN STERILIZATION M1226 0050 81...
Page 89: ...M1226 0050 82...
Page 90: ...M1226 0050 83...
Page 91: ...M1226 0050 84...
Page 92: ...M1226 0050 85...