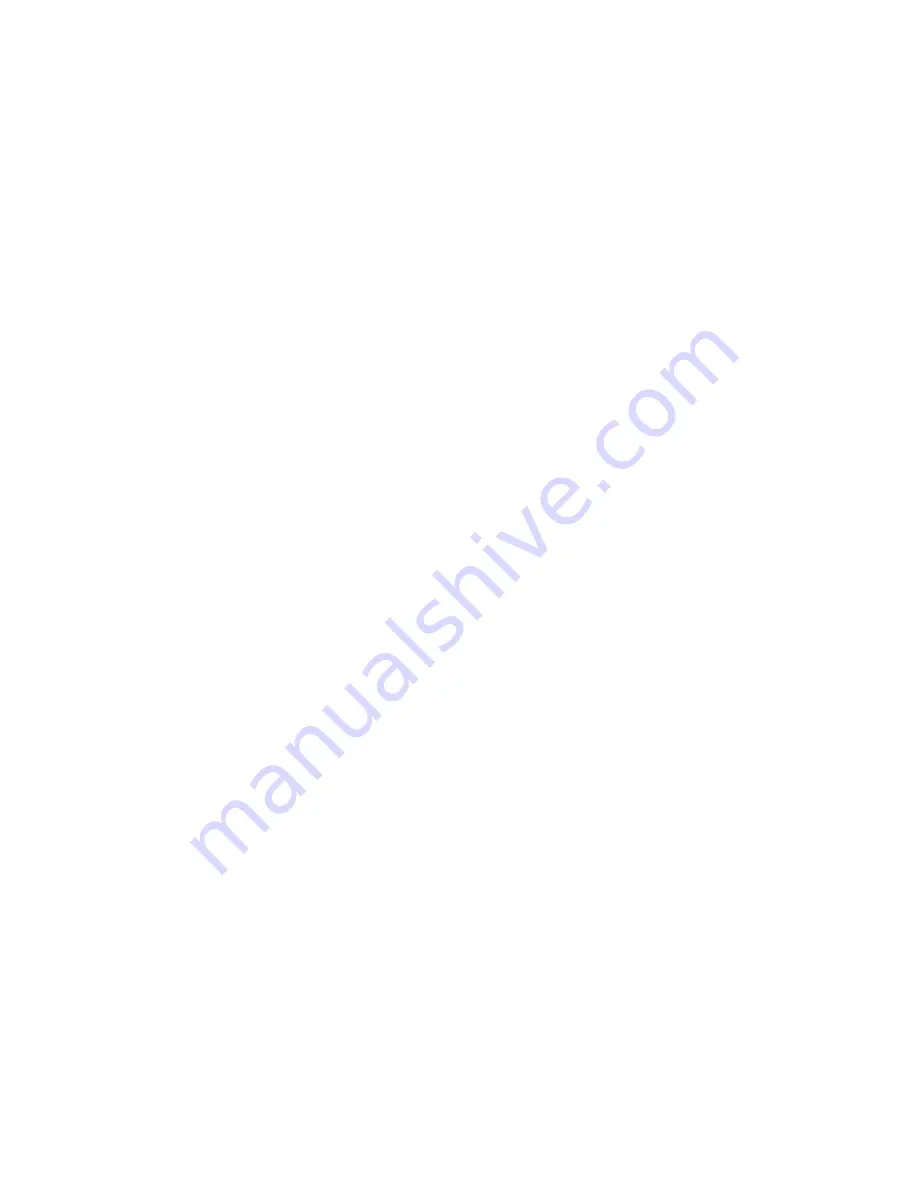
1.6 AERATION
Sterile air is introduced into the medium through the ring sparger, and is controlled by
the needle valve of the flowmeter. It is able to provide 1.5 (working volume) of sterile
air thru 0.2
μ
m replaceable cartridge filter (Fig. 1). The filter is sterilizable with the
vessel. With the system, Oxygen Transfer Rates of 350 mMO2/L/Hr may be obtained.
1.7 pH
CONTROL
pH is controlled in the range of 2.00-12.00 (
±
0.01). The pH is sensed by a glass
electrode. Control is maintained by PID controller which operates two peristaltic
pumps, connected to acid and base addition ports (Fig. 1).
1.8 DO
CONTROL
DO is controlled in the range of 5-95% (
±
1%). It is sensed by the DO electrode and
control is maintained by the PID controller which changes the speed of agitation.
1.9 FOAM
CONTROL
Foam is controlled during batch fermentation by the antifoam probe which is located
in the headplate. The controller operates the antifoam addition pump that adds
chemical defoamer through the port in the wall of the vessel (Fig. 1). Sensitivity and
time adjustments are made on potentiometers located on a small printed circuit board
mounted on the underside of the electronic shelf, easily accessible when the rear door
is open. The potentiometer on the right (P1) is for sensitivity adjustment and the
potentiometer on the left (P2) is for percent pump on time adjustment.
1.10 MEDIUM FLOW CONTROL
A nutrient feed peristaltic pump is provided for use during continuous culture
fermentation. The maximum flow rate can be found in section 3.8.
1.11 EXHAUST
SYSTEM
The exhaust gases pass into the exhaust condenser where moisture is removed and
returned to the vessel. The air remaining passes through the 0.2
μ
m exhaust filter and
goes to the atmosphere (Fig. 1).
1.12 SAMPLING
SYSTEM
The sampler is attached to a sampling tube that extends to the liquid of the vessel.
The
sampler has a rubber suction bulb to facilitate collection of representative samples
M1226-0050 3
Summary of Contents for BIOFLO III
Page 2: ......
Page 7: ......
Page 9: ...M1226 0050 2...
Page 37: ...M1226 0050 30...
Page 40: ...M1226 0050 33...
Page 48: ...FIGURE 1 VESSEL SCHEMATIC M1226 0050 41...
Page 49: ...FIGURE 2 SAMPLING SYSTEM M1226 0050 42...
Page 50: ...FIGURE 3 FLOWMETER CONVERSION M1226 0050 43...
Page 51: ...FIGURE 4 FRONT PANEL M1226 0050 44...
Page 52: ...FIGURE 5 REAR OF CABINET M1226 0050 45...
Page 53: ...FIGURE 6 SWITCH PANEL M1226 0050 46...
Page 54: ...FIGURE 7 EXTERNAL NUTRIENT PUMP TERMINAL M1226 0050 47...
Page 55: ...FIGURE 8 SUGGESTED IMPELLER LOCATION M1226 0050 48...
Page 56: ...FIGURE 9 HEADPLATE M1226 0050 49...
Page 57: ...FIGURE 10 SPARGER TUBE M1226 0050 50...
Page 58: ...FIGURE 11 HARVEST TUBE M1226 0050 51...
Page 59: ...FIGURE 12 THERMOWELL M1226 0050 52...
Page 60: ...FIGURE 13 FOAM PROBE M1226 0050 53...
Page 61: ...FIGURE 14 BAFFLE INSTALLATION M1226 0050 54...
Page 62: ...FIGURE 15 SIDE PORTS M1226 0050 55...
Page 63: ...FIGURE 16 pH PROBE INSTALLATION M1226 0050 56...
Page 64: ...FIGURE 17 D O PROBE PHOENIX INSTALLATION M1226 0050 57...
Page 65: ...FIGURE 18 D O PROBE INGOLD INSTALLATION M1226 0050 58...
Page 66: ...FIGURE 19 CONVERSION OF D O PORT TO INOCULATION PORT M1226 0050 59...
Page 67: ...FIGURE 20 EXHAUST CONDENSER INSTALLATION M1226 0050 60...
Page 68: ...FIGURE 21 RESTRICTOR IN CONDENSER WATER IN LINE M1226 0050 61...
Page 69: ...FIGURE 22 DISASSEMBLY OF CONDENSER M1226 0050 62...
Page 70: ...FIGURE 23 FACTOR AFFECTING pH CONTROL M1226 0050 63...
Page 86: ...M1226 0050 79...
Page 87: ...FIGURE 25 BEARING HOUSING ASSEMBLY M1226 0050 80...
Page 88: ...FIGURE 26 BEARING HOUSING IN STERILIZATION M1226 0050 81...
Page 89: ...M1226 0050 82...
Page 90: ...M1226 0050 83...
Page 91: ...M1226 0050 84...
Page 92: ...M1226 0050 85...