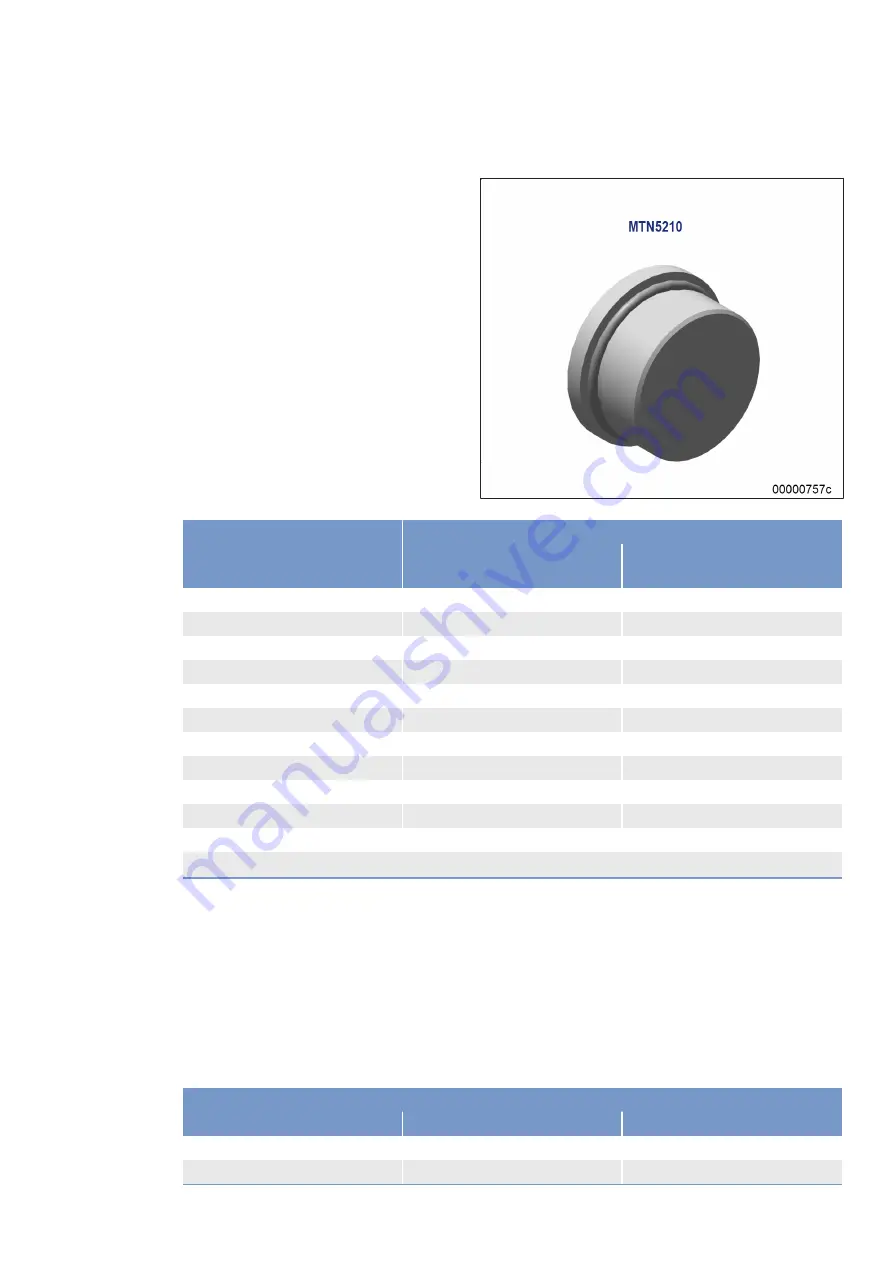
Tightening torques for plug screw joints as per MTN 5183-6
Thread
screwed into
Steel/gray cast iron M
A
(Nm)
AI alloy M
A
(Nm)
M10 x 1
20
10 +2
M12 x 1.5
35
14 +2
M14 x 1.5
45
15 +3
M16 x 1.5
55
18 +3
M18 x 1.5
70
23 +3
M22 x 1.5
100
33 +4
M27 x 2
170
57 +5
M33 x 2
310
103 +10
M42 x 2
330
110 +11
M48 x 2
420
140 +14
M60 x 2
–
200 +20
M
A
= tightening torques
Assembly instructions and tightening torque for hose fittings with union nuts
These instructions do not apply to ORFS fittings. In contrast to the instructions for pipe unions, hose fittings
with sealing heads and the matching adapters must be fitted and connected as follows.
Hose fitting, metallic sealing with union nut: tighten union nut by hand then tighten a further max. 1/4 of a
turn with a wrench.
Hose fitting with O-ring and union nut: tighten union nut by hand then tighten a further max. 1/2 of a turn
with a wrench.
Hoses must be properly aligned before tightening the union nuts.
Sealing head/sealing cone with metric union nut
Metric thread
Pipe outer dia.
Torque (Nm)
M12 x 1.5
6
20
M14 x 1.5
8
38
MS15041/03E 2018-08
| General Information | 33
TIM-ID: 0000002333 - 018
Summary of Contents for 12V4000C*5 series
Page 1: ...Operating Instructions Diesel engine 12V4000Cx5 16V4000Cx5 MS15041 03E...
Page 3: ......
Page 4: ......
Page 46: ...1 B13 Crankskaft speed 44 General Information MS15041 03E 2018 08 TIM ID 0000063565 001...
Page 196: ...1 Bypass flap 194 Exhaust Gas Recirculation MS15041 03E 2018 08 TIM ID 0000063475 002...
Page 264: ...262 Manufacturer s Documentation MS15041 03E 2018 08...
Page 266: ...264 Manufacturer s Documentation MS15041 03E 2018 08 TIM ID 0000098598 001...
Page 267: ...MS15041 03E 2018 08 Manufacturer s Documentation 265 TIM ID 0000098598 001...
Page 268: ...266 Manufacturer s Documentation MS15041 03E 2018 08 TIM ID 0000098598 001...
Page 269: ...MS15041 03E 2018 08 Manufacturer s Documentation 267 TIM ID 0000098598 001...
Page 270: ...268 Manufacturer s Documentation MS15041 03E 2018 08 TIM ID 0000098598 001...
Page 271: ...MS15041 03E 2018 08 Manufacturer s Documentation 269 TIM ID 0000098598 001...
Page 272: ...270 Manufacturer s Documentation MS15041 03E 2018 08 TIM ID 0000098598 001...
Page 273: ...MS15041 03E 2018 08 Manufacturer s Documentation 271 TIM ID 0000098598 001...
Page 274: ...272 Manufacturer s Documentation MS15041 03E 2018 08 TIM ID 0000098598 001...
Page 275: ...MS15041 03E 2018 08 Manufacturer s Documentation 273 TIM ID 0000098598 001...
Page 276: ...274 Manufacturer s Documentation MS15041 03E 2018 08 TIM ID 0000098598 001...
Page 288: ...286 Manufacturer s Documentation MS15041 03E 2018 08 TIM ID 0000083486 002...