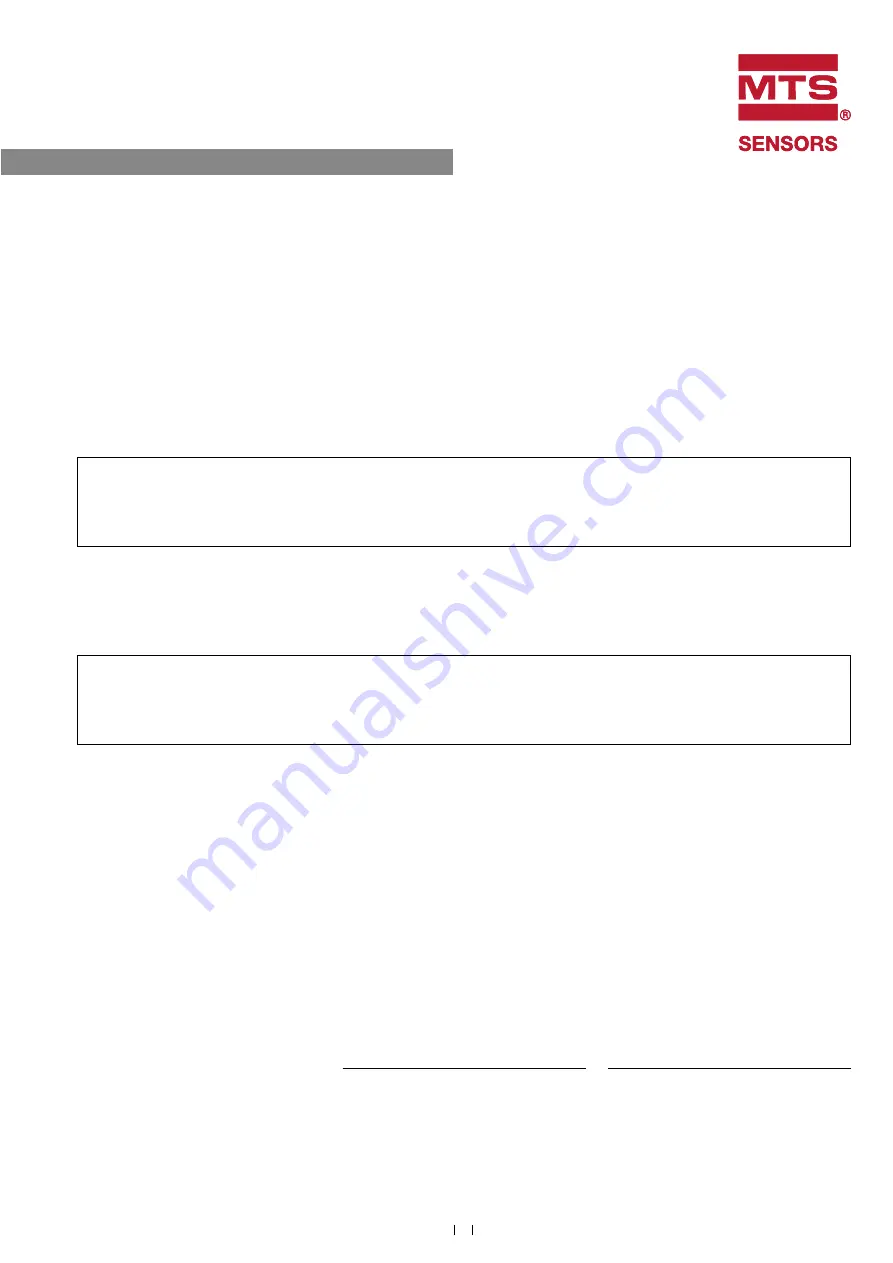
51
10. Appendix
Safety Declaration
Dear Customer,
If you return one or several sensors for checking or repair, we need you to sign a safety declaration. The purpose of this declaration is to ensure
that the returned items do not contain residues of harmful substances and / or that people handling these items will not be in danger.
MTS Sensors order number: ________________________________
Serial number(s): _________________________________________
Sensor type(s): __________________________________________
Sensor length(s): ________________________________________
The sensor has been in contact with the following materials:
In the event of suspected penetration of substances into the sensor,
consult MTS Sensors to determine measures to be taken before
shipment.
Do not specify chemical formulas.
Please include safety data sheets of the substances, if applicable.
Short description of malfunction:
Corporate information
Company: _______________________________________________
Address: _______________________________________________
_______________________________________________________
Contact partner
Name: _______________________________________________
Phone: _______________________________________________
E-mail: _______________________________________________
We hereby certify that the measuring equipment has been cleaned and neutralized.
Equipment handling is safe. Personnel exposure to health risks during transport and repair is excluded.
Date
Signature
Stamp
Tel. + 49 - 23 51- 95 87 0
Fax. + 49 - 23 51- 5 64 91
[email protected]
www.mtssensors.com
GERMANY
MTS Sensor Technologie
GmbH & Co.KG
Auf dem Schüffel 9
58513 Lüdenscheid, Germany
USA
MTS Systems Corporation
Sensors Division
3001 Sheldon Drive
Cary, N.C. 27513, USA
Tel. +1 919 677-0100
Fax +1 919 677-0200
[email protected]
www.mtssensors.com
Safety Declaration
Dear Customer,
If you return one or several sensors for checking or repair, we need you to sign a safety declaration. The purpose of this declaration is to ensure
that the returned items do not contain residues of harmful substances and / or that people handling these items will not be in danger.
MTS Sensors order number: ________________________________
Serial number(s): _________________________________________
Sensor type(s): __________________________________________
Sensor length(s): ________________________________________
The sensor has been in contact with the following materials:
In the event of suspected penetration of substances into the sensor,
consult MTS Sensors to determine measures to be taken before
shipment.
Do not specify chemical formulas.
Please include safety data sheets of the substances, if applicable.
Short description of malfunction:
Corporate information
Company: _______________________________________________
Address: _______________________________________________
_______________________________________________________
Contact partner
Name: _______________________________________________
Phone: _______________________________________________
E-mail: _______________________________________________
We hereby certify that the measuring equipment has been cleaned and neutralized.
Equipment handling is safe. Personnel exposure to health risks during transport and repair is excluded.
Date
Signature
Stamp
Tel. + 49 - 23 51- 95 87 0
Fax. + 49 - 23 51- 5 64 91
[email protected]
www.mtssensors.com
GERMANY
MTS Sensor Technologie
GmbH & Co.KG
Auf dem Schüffel 9
58513 Lüdenscheid, Germany
USA
MTS Systems Corporation
Sensors Division
3001 Sheldon Drive
Cary, N.C. 27513, USA
Tel. +1 919 677-0100
Fax +1 919 677-0200
[email protected]
www.mtssensors.com