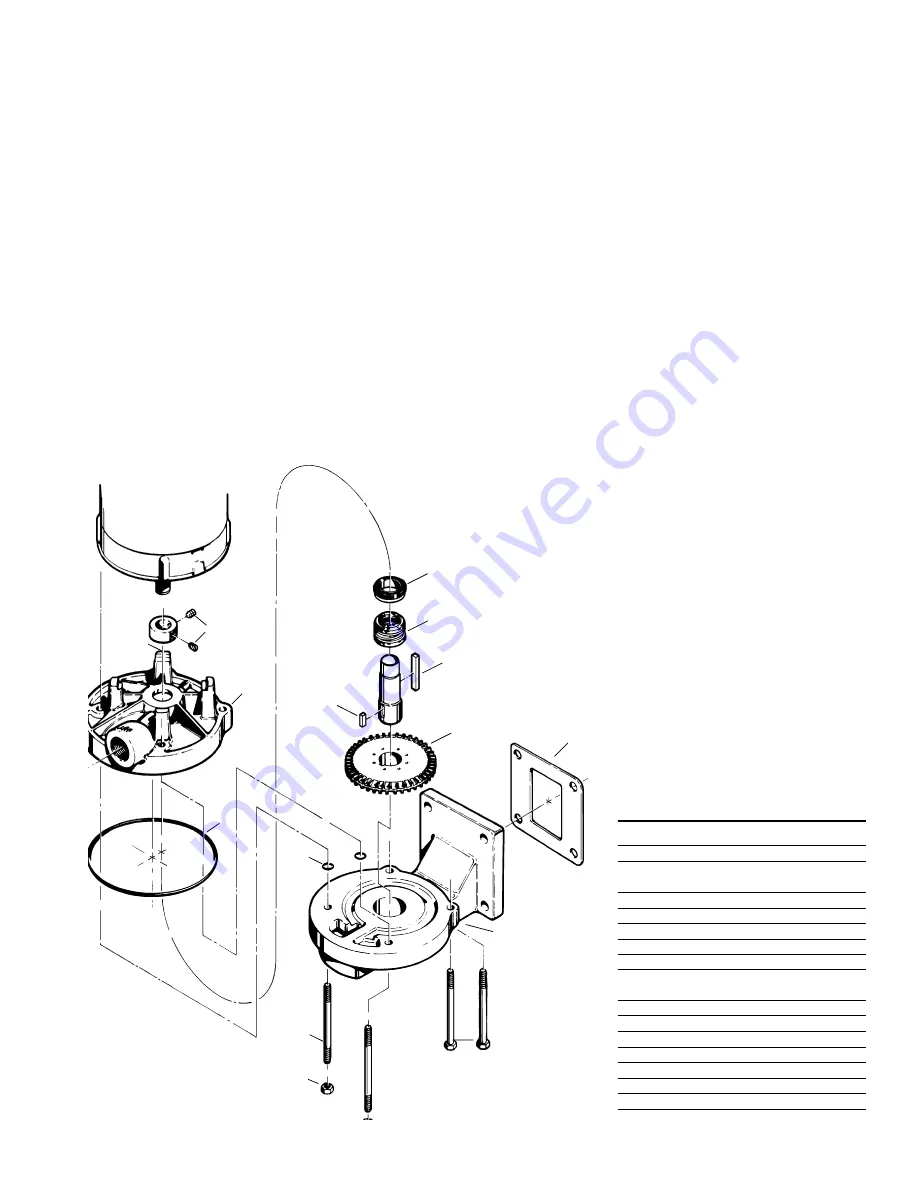
Page 511
Figure 4-5
C3 VERTICAL FLANGE MOUNT PUMP
carefully inspect for microscopic
cracks and nicks. Scratches that
might be ignored elsewhere can
produce leakage if they are on seal
carbons and seat wearing surfaces.
Cleanliness is imperative when
working with mechanical seals.
Almost unnoticeable particles
between seal faces can be, and
often are, the cause of early seal
failures.
Check the impellers, they are
designed to float. They should
move easily on the shaft. As long
as they can be moved on the shaft
by hand, they are loose enough. If
the impeller can be rocked or
wobbled, it is too loose and must be
replaced.
Check the sleeve or shaft for
galling, pitting, and corrosion. If the
shaft or sleeve is corroded where
the seal comes in contact with
them, the shaft or sleeve must be
replaced. Surface corrosion must
be removed so that seals can slide
freely during assembly. The shaft
diameter should be no smaller than
.002" below the nominal fractional
seal sizes. Remove any nicks or
burrs which may have occurred
during disassembly. Reclean parts
as necessary.
4E Reassembly (C3 and P3)
All parts should be visually inspect-
ed and cleaned or replaced as
outlined in 4D above.
1. The seal seat (#125) must be
installed in the motor bracket
before the bracket is installed on
the motor. To install the seat:
a. Place the motor bracket face
up on a flat surface.
15
14
1
7
125
12
23
11
23A
60
19
2
18
20
b. Carefully press the seat,
smooth side up, into the seat
cavity of the motor bracket.
To make the installation of the
seat easier, apply a thin
coating of compatible lubricant
to the elastomer portion of the
seat prior to installation. Care
must be taken not to damage
the seat face. Thumb
pressure is usually sufficient
to install the seat.
2. Install the motor bracket.
a. Make sure the locking collar is
positioned on the motor shaft.
b. While holding the motor
bracket with the outlet port
facing up, slide the bracket
over the two (2) studs on the
motor face.
c. Slide the bracket back until
the feet are resting against the
motor face. Light tapping may
be necessary to seat the
motor bracket in the proper
position.
d. Install the four (4) “O” rings
(#8) on the two studs. This
will help hold the bracket in
place during the remainder of
the assembly operation.
NAME/DESCRIPTION
PART NO.
QTY.
Motor Bracket
1
1
Cover/Vertical
2
1
"O" Ring/Casing
7
1
"O" Ring/Guide Rod
8
4
Impeller
11
1
Seal Rotating Element
12
1
Seal Stationary Seat
125
1
Lock Collar/Sleeve
14
1
Setscrew/Lock Collar
15
2
Shaft Sleeve
17
1
Guide Rod
18
2
ThruBolt
19
2
Nut
20
2
Pipe Plug/Drain
22
1
Key/Impeller Drive
23
1
Key/Sleeve Drive
23A
1
Gasket
60
1
8
C3