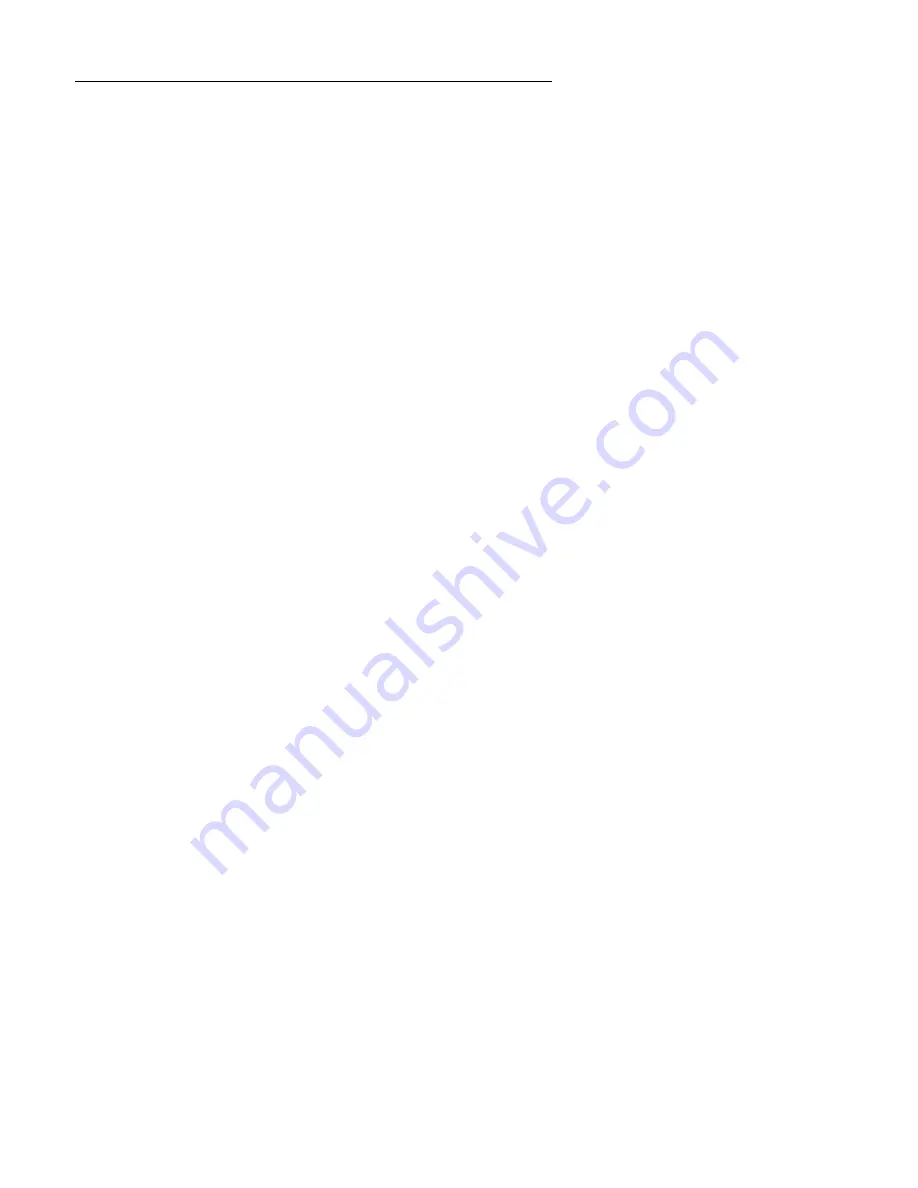
A. Failure to Pump
B. Reduced Capacity
C. Reduced Pressure
D. Pump Loses Prime After
Starting
E. Excessive Power Consumption
F. Pump Vibrates or is Noisy
G. Mechanical Problems
H. Seal Leakage
5B Reduced Capacity
1. Pump not up to speed — Use a
tachometer to determine actual
RPM. Check voltage and wiring
connections.
2. Excessive suction lift — Relocate
pump, supply tank or both to
minimize suction lift.
3. Insufficient NPSH — Relocate
pump, supply tank or both to
improve NPSH available if
possible. Increase suction
pressure. Reduce fluid tempera-
ture. Select a pump with lower
NPSH requirements.
4. Mechanical damage — Rotate
the pump by hand to determine if
there are tight spots. Broken or
bent impeller vanes can some-
times be detected in this manner.
If there is a suspicion of damage,
remove the pump from service
and disassemble for inspection.
5. Air leak in the suction line — Fill
the system with fluid and
hydrostatically test. Tighten
connections or replace leaky
components.
6. Air pockets in the suction piping
— Operating the system at
maximum flow conditions will
usually clear the lines. Evacuate
the system with a vacuum pump
if necessary.
7. Suction lines, strainer, or foot
valve too small or clogged —
Inspect and clean out as neces-
sary. Fittings and lines should
be at least equal to the pump
suction size.
8. Discharge head too high —
Install a pressure gauge at the
pump discharge to determine the
actual operating pressure.
Compare readings with pump
performance curve. A larger
pump may be necessary.
9. Excessive wear — If a pump had
previously performed satisfactori-
ly and now gives evidence of
reduced performance, it should
be disassembled and examined
for wear after the simpler
possible problems have been
investigated.
5C Reduced Pressure:
1. Pump not up to speed — Use a
tachometer to determine actual
RPM. Check voltage and wiring
connections.
2. Air or vapor in liquid — Install a
separator in the suction line.
Check the seal on the inlet end
of the pump to determine if air is
being drawn in. Hydrostatically
test the system to insure that
there are no leaks.
3. Mechanical wear or damage —
Rotate the pump by hand to
determine if there are tight spots.
Broken or bent impeller vanes
can sometimes be detected in
this manner. If there is a
suspicion of damage or wear,
remove the pump from service
and disassemble for inspection.
Look for wear on the impeller,
suction cover, and motor bracket.
4. System head less than expected
— Replace pump with higher
capacity unit or add a valve or
orifice to increase line resis-
tance.
5D Pump Loses Prime After
Starting
1. Leak in suction line — Fill the
system with fluid and hydrostati-
cally test. Tighten connections or
replace leaky components.
2. Air entering pump through inlet
seal or “O” rings — Hydrostati-
cally test the pump and look for
leaks. Replace faulty seals or
“O” rings.
5.
5A Failure to Pump
1. Pump not up to speed — Use
tachometer to determine actual
RPM. Check voltage and wiring
connections.
2. Pump not primed — Confirm that
pump and all inlet piping is filled
with fluid.
3. Discharge head too high —
Install a pressure gauge at the
pump discharge to determine the
actual operating pressure.
Compare readings with pump
performance curve. A larger
pump may be necessary.
4. Excessive suction lift — Relocate
pump, supply tank, or both to
minimize suction lift.
5. Wrong direction of rotation —
Compare pump rotation with
arrow on pump. Standard
pumps rotate in a clockwise
direction when looking at the
shaft extension end or from the
motor end on close coupled
pumps. Reverse two leads on a
three phase motor to change
rotation. Check motor nameplate
for single phase operation.
6. Clogged suction line, strainer or
valve — Inspect and clean out if
necessary.
7. Air pocket in suction line — Look
for high spots in inlet piping
system. Evacuate the system
with a vacuum pump if neces-
sary.
Page 518
FLEXIBLE COUPLED PUMPS
CLOSE COUPLED PUMPS
VERTICAL FLANGE MOUNTED PUMPS
Troubleshooting
T51 SERIES