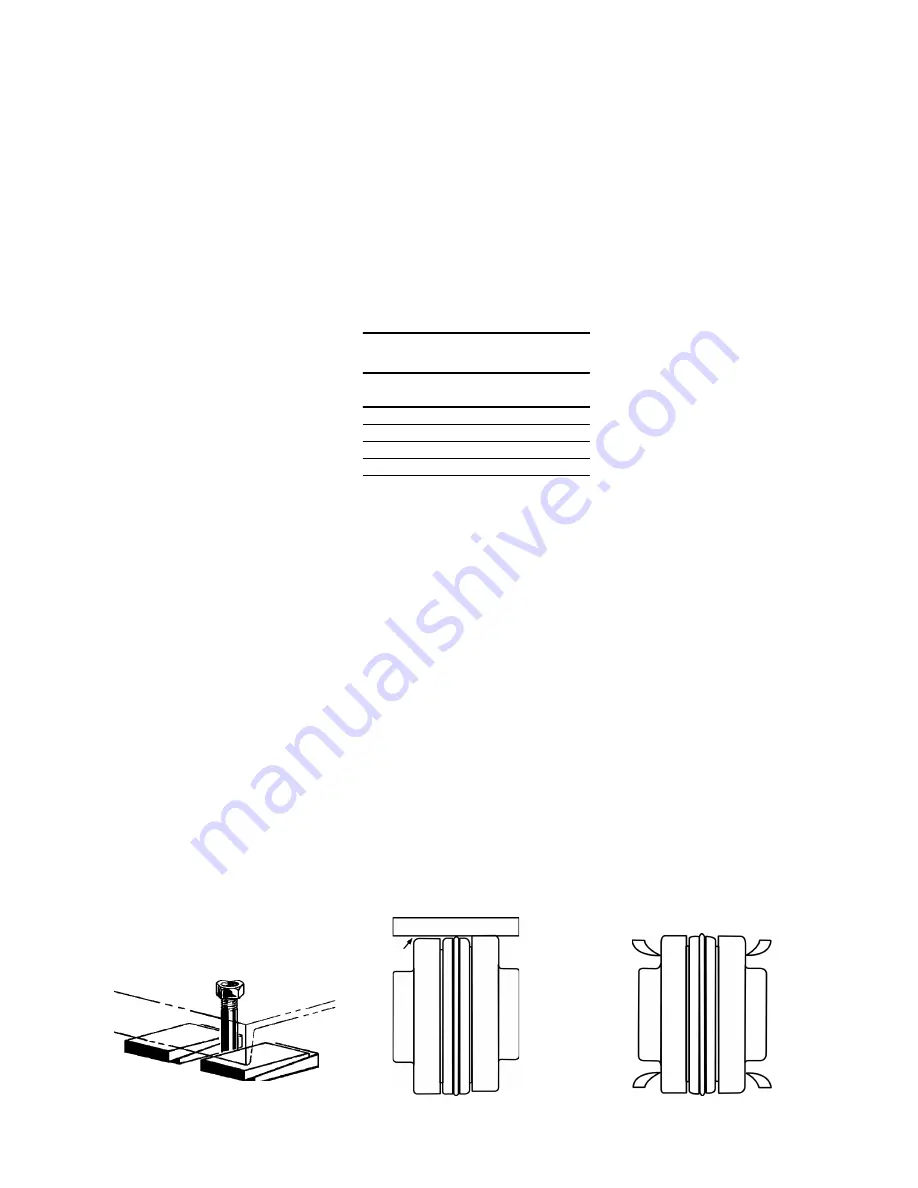
Page 505
2D Alignment
Although flexible coupled pumps are
carefully aligned prior to crating and
shipping, it is very likely that strains
imposed during transit have altered
the alignment. Complete the
following steps after the unit has
been placed on the foundation and
leveled.
The standard coupling supplied by
MTH Pumps has an elastomer
member between two internal
serrated flanges. They have smooth
outsides of equal diameter. These
surfaces are used for alignment
procedures. To check the PARAL-
LEL alignment: (Refer to Figure 2-4)
1. Place a straightedge across the
two coupling flanges.
2. Measure the maximum offset (A),
Figure 2-4, at various points
around the periphery of the
coupling. DO NOT rotate the
coupling.
3. If the maximum offset exceeds
the Parallel dimension in Chart 1
for your sleeve size, loosen the
motor or pump and place thin
metal shims under the motor or
pump feet until the offset is
corrected.
4. Torque down the motor or pump.
5. Recheck alignment.
To check the ANGULAR alignment:
(Refer to Figure 2-5)
1. Using a micrometer or caliper,
measure from the outside of one
flange to the outside of the other
at intervals around the periphery
of the coupling. DO NOT rotate
the coupling.
2. Determine the maximum (B) and
minimum (C) dimensions.
2E Piping
2E1 Alignment
It is important that all piping be lined
up and not forced into place. It is
recommended that you begin piping
at the pump. If the lines are ended
at the pump, particularly if the last
piece is cut a little too short or long,
the pump will be forced to meet the
pipe and strain or distortion will
result.
2E2 Piping Support
Never allow the pump to support
piping. Other means such as pipe
hangers and pipe supports should
be used to carry piping to avoid
misalignment and distortion.
Consideration should be given to
thermally induced expansion and
contraction, particularly in long runs
of straight pipe.
2E3 Piping Size
In general, outlet and especially inlet
pipe sizes should be equal to or
larger than those of the pump.
This may not, however, be the final
determining factor. Many things,
including installation and operating
costs are involved in the decision.
Careful use of the pipe and fitting
friction loss tables (as shown in the
Hydraulic Institute manual), along
with the appropriate pump perfor-
mance curve, should be the basis
for judgements.
Figure 2-3
3. If the difference between the
maximum and minimum exceeds
the Angular dimension in Chart 1
for your sleeve size, loosen the
motor or pump and place thin
metal shims under the motor or
pump feet until the misalignment
is corrected.
4. Torque down the motor or pump.
5. Recheck the parallel alignment
above.
CHART 1
If the parallel or angular misalign-
ment is great, this is an indication of
baseplate distortion and must be
corrected first, refer to 2C Leveling.
After all leveling and alignment
operations have been completed,
piping can begin. After the piping
has been completed, refer to 2E1,
Piping Alignment. Alignment of the
unit must be rechecked to make
certain that no piping strains are
causing distortion. After approxi-
mately two weeks of operation,
check the alignment again to make
sure that temperature changes,
piping strain, or foundation varia-
tions have not caused
misalignment. If alignment has
been maintained over this period,
the pump and motor can be
dowelled to the baseplate.
B
C
A
Figure 2-5
Figure 2-4
COUPLING TYPES JE, J, S
MAX. RPM & ALLOWABLE MISALIGNMENT
SLEEVE
SIZE
MAXIMUM
RPM
PARALLEL
A
ANGULAR
B-C
3
9200
.010
.035
4
7600
.010
.043
5
7600
.015
.056
6
6000
.015
.070