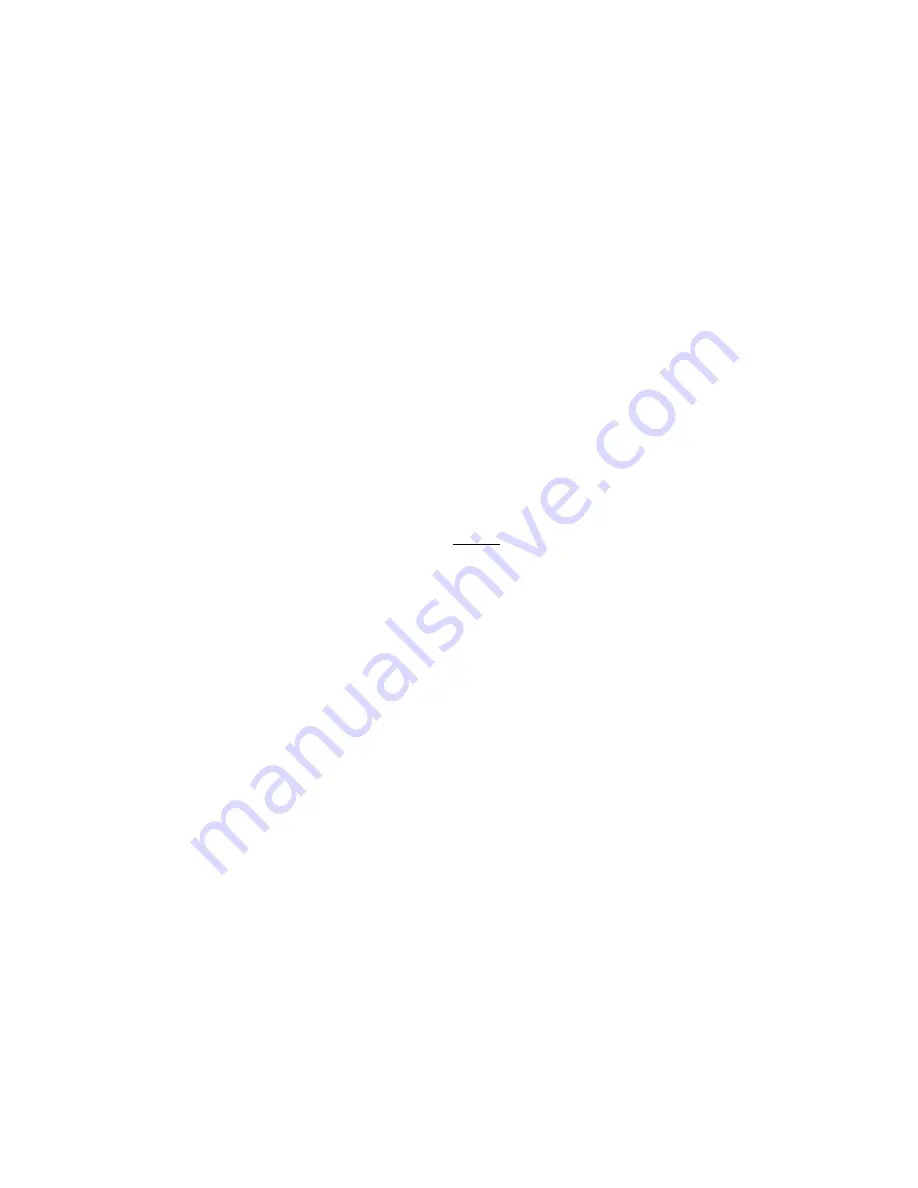
source. It should be the same size
as the pump inlet or sized based
on reasonable fluid friction losses.
A foot valve is recommended when
lifting fluid from a sump. This will
save wear and tear on any pump,
even those equipped with self
priming capability.
A Y-Strainer is recommended
immediately ahead of the pump on
any newly constructed system.
This is advisable due to the
probability that foreign material
large enough to damage pump
clearances may remain even
though the piping has been
flushed.
Valves in the outlet piping of a
regenerative turbine pump should
always be open as far as possible
when the pump is started. This will
reduce the start-up load on the
pump and motor. Never start the
pump with the discharge valve
closed.
The inlet valving should be open
when starting any pumping system.
Without some fluid in the pump, it
can gall and lock up impellers.
Violent pump failure will result from
continued operation with the inlet
valve closed.
1D4 Priming
Regardless of whether self-priming
equipment is used or not, always
fill the pump and vent it of air
before starting for best seal and
pump life. Under most circum-
stances, regenerative turbine
pumps can be made to self-prime
as long as a small amount of fluid
can be recirculated through the
impeller and the fluid doesn’t heat
up noticeably.
1D5 NPSH (Net Positive Suction
Head)
The NPSH required varies with
every size and capacity of pump.
The NPSH required by your unit
can be obtained from the perfor-
mance curves or from your MTH
representative.
If the NPSH available is not equal
to or greater than that required by
the pump, it must be increased or
a different pump selected. The
usual method for increasing NPSH
is to raise the static head on the
pump inlet, H
s
.
Page 503
P
s
- P
vp
sp. gr.
By definition, NPSH means: “net
positive suction head” above the
vapor pressure of the pumped
liquid available at the centerline of
the pump. It should always be
given in feet of pumped liquid. The
NPSH is actually a measurement
of the amount of energy available
in the pumped liquid to produce the
required absolute entrance velocity
in the pump. If a pump requires
more energy (or NPSH) than is
available at a given capacity, the
pressure at the inlet will fall below
the vapor pressure of the pumped
liquid and loss of performance will
result.
P
s
= Pressure in the suction vessel
in PSIA.
P
vp
= Vapor pressure of the
pumped fluid in PSIA.
H
s
= Static height of the pumped
fluid above (+) or below (-) the
centerline of the pump in feet.
H
f
= All friction losses from the
vessel to the pump in feet.
NPSH = 2.31(
)+H
s
-H
f
For boiling liquids, P
s
and P
vp
are
equal. This item then becomes
zero and can be omitted from the
equation.
1D6 Noise
Regenerative turbine pumps
typically produce a high pitched
whine that increases in intensity as
the differential pressure produced
in the pump increases. While high
frequency sound is attenuated
more easily than lower frequen-
cies, piping structures and the
fluids in them readily transmit
noise. Motors, bearings, and other
rotating components add to the
noise and sometimes create
objectionable harmonics.
Careful pump installation can
alleviate noise problems. Proper
alignment of the pump and driver is
essential. Adequate supports for
the inlet and discharge piping is
equally important. A degree of
noise reduction may be obtained
when the pumping unit is support-
ed free of building structures by the
use of vibration isolators and
flexible piping and conduit connec-
tions. Elastomer type couplings are
the best choice to separate motor
noises from the fluid and piping
structure.
1D7 Freezing
When ambient temperatures drop
below the freezing point of the fluid in
a pump, consideration should be given
to heating, insulating, or draining the
pump. If you choose to drain the
pump, and it will only be for a short
period, first remove the drain plugs,
and then drain the inlet and outlet
lines. Carefully blow out the pump
with compressed air to clear all
internal cavities of fluid.
1E Recommended Spare Parts
FOR CRITICAL SERVICES - a duplex
installation, with two identical pumping
units in parallel, is the safest and many
times the most cost effective choice.
FOR IMPORTANT SERVICES - a
standby pump, ready for installation is
advised. Special pricing and new
pump warranty is offered for factory
rebuilding. Turn around time can be
as short as one or two days for
standard models.
FOR ROUTINE MAINTENANCE - only
the mechanical seals and a complete
set of “O” ring gaskets are recom-
mended. Should additional
components show wear, they are
available from stock at the factory.
FOR SERVICING A PUMP THAT
DOES NOT PRODUCE RATED HEAD
- mechanical seals, “O” ring gaskets,
impeller, motor bracket, and cover.
FOR REBUILDING A PUMP - all the
components required for servicing,
plus bearings, shaft, and drive keys for
flexible coupled pumps, should be
obtained. A factory rebuild should be
considered whenever your disassem-
bly indicates rebuilding is necessary
as this is usually more economical.
The factory recommendation for spare
parts are all of those needed for
rebuilding a pump and are shown on
the exploded view drawings for each
individual type of pump.