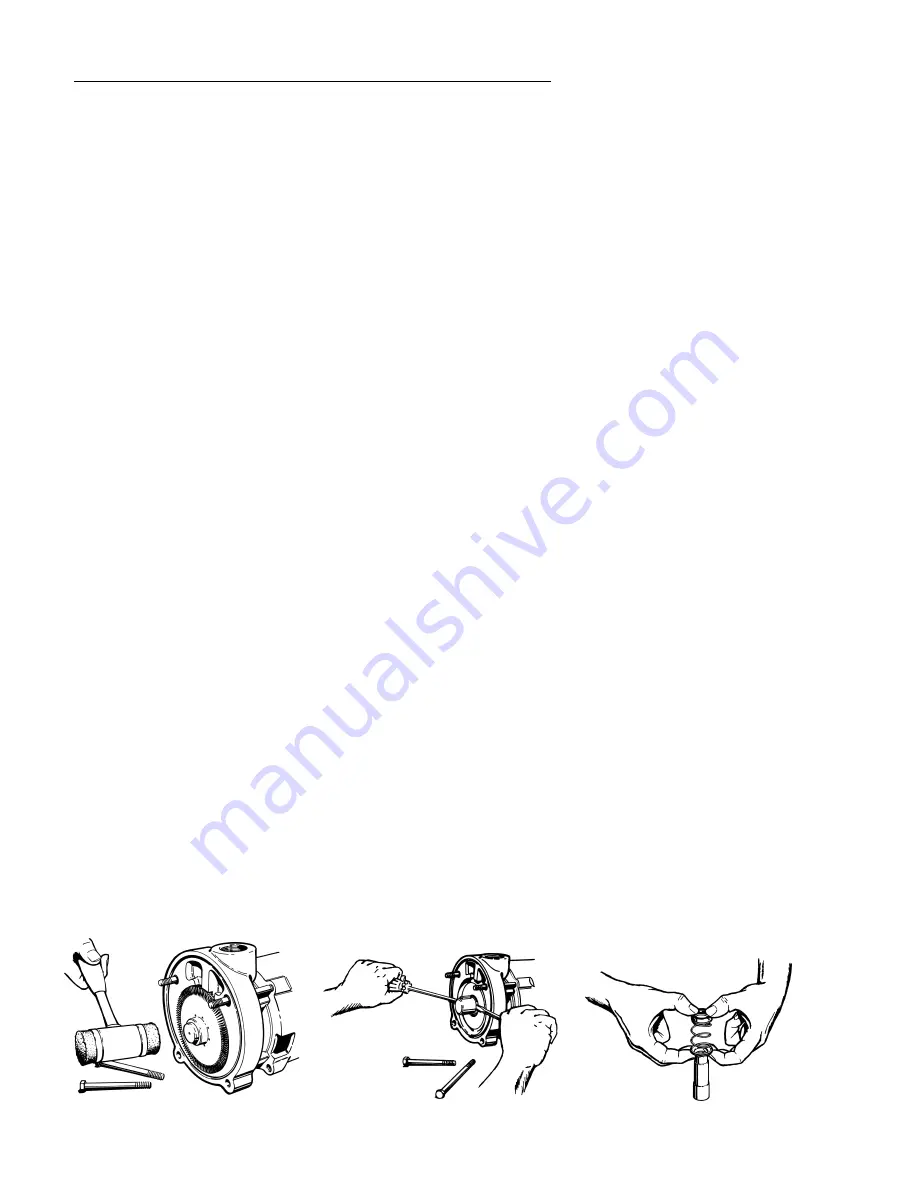
A. Preliminary
B. Disassembly C3 & P3
C. Disassembly C15 & P15
D. Inspection of Components
E. Reassembly C3 & P3
F. Reassembly C15 & P15
G. Testing and Final Adjustments
4A Preliminary
Before attempting any service on
the pump or motor, disconnect the
electrical power to the pump motor.
If the pump and motor are to be
removed as a unit, note the wiring
configuration. Use colored or
numbered tape to mark the wire
connections of the motor and power
source, for reconnection. If the
pump is being used to transfer hot
liquid, let the pump and liquid cool
before starting disassembly.
1. Disconnect the inlet and outlet
piping before unbolting the pump
and motor. If the pipes are
corroded, use penetrating oil on
the threads to aid in removal.
2. Unbolt the motor from the base
and remove the unit. All work on
the unit should be performed on
an elevated workbench whenev-
er possible.
The disassembly and reassembly
procedures are broken into four
sections covering the following
units:
4B — Disassembly of the C3 and
P3 Units (3 hp and under)
4C — Disassembly of the C15 and
P15 Units (5 hp and up)
4E — Reassembly of the C3 and
P3 Units
4F — Reassembly of the C15 and
P15 Units
Figure 4-2
Figure 4-3
Exploded views of each unit,
Figures 4-4, 4-5, 4-11, and 4-12,
are provided for referencing the
numbers in the following proce-
dures, i.e. (#1), motor bracket.
4B Disassembly (C3 and P3)
The following tools and equipment
are needed for disassembly of C3
and P3 units:
1. Soft plastic or wooden mallet.
2. Small ball pein hammer.
3. 9/16" wrench or socket.
4. 5/32" hex wrench.
5. Penetrating oil.
6. 1" wood dowel (Approx. 6"
long).
7. Thin blade screwdriver.
8. Two large blade screwdrivers.
9. Cealube G or similar glycol base
lubricant. (DO NOT use petro-
leum products.)
To disassemble the pump:
Refer to Figures 4-4 and 4-5 for
reference to the numbered parts in
the procedures below.
1. Remove all liquid from the
pump. Air blown through the
pump will remove the water
quickly.
2. Remove the two (2) nuts (#20),
and the two (2) 3/8" X 4" bolts
(#19) from the cover (#2).
3. Remove the cover. In some
cases light tapping with a plastic
or wooden mallet on the outside
diameter of the cover may be
required to loosen it from the
motor bracket. Care should be
taken if a screwdriver is needed
to pry between the cover and
motor bracket. Damage to the
“O” ring (#7) and/or impeller can
result.
4. Remove the impeller (#11), refer
to Figure 4-1. The impeller is a
slip fit and, under normal condi-
tions, can be removed by gently
tapping on the end of the shaft
sleeve with a mallet. Leave the
impeller key (#23) in place.
Striking the sleeve too hard could
damage the seat or rotating
element.
5. Using the 5/32" hex wrench,
loosen the set screws (#15) in the
locking collar (#14), located on
the shaft sleeve between the
motor bracket and the motor face.
The collar should now be loose on
the sleeve. Note the condition of
the setscrew in the collar and
replace if necessary.
6. Remove the shaft sleeve (#17).
The sleeve is a keyed fit and is
removed using two large screw-
drivers, Refer to Figure 4-2.
a. Insert the blades of the
screwdrivers between the
springholder on the rotating
element and the shoulder of
the shaft sleeve.
b. Holding the screwdrivers at
approximately 3 o’clock and 9
o’clock, push the handles in
toward the motor body, using
the motor bracket for leverage.
7. In some cases a rocking motion of
the screwdrivers will be necessary
to break the sleeve loose.
Normally the rotating element will
slide off with the sleeve. DO NOT
attempt to remove the sleeve by
rotating it. (Previous models have
used a threaded shaft and
different procedures are required
in these cases.)
4.
Figure 4-1
Page 508
PUMP ENDS
T51 SERIES
Service