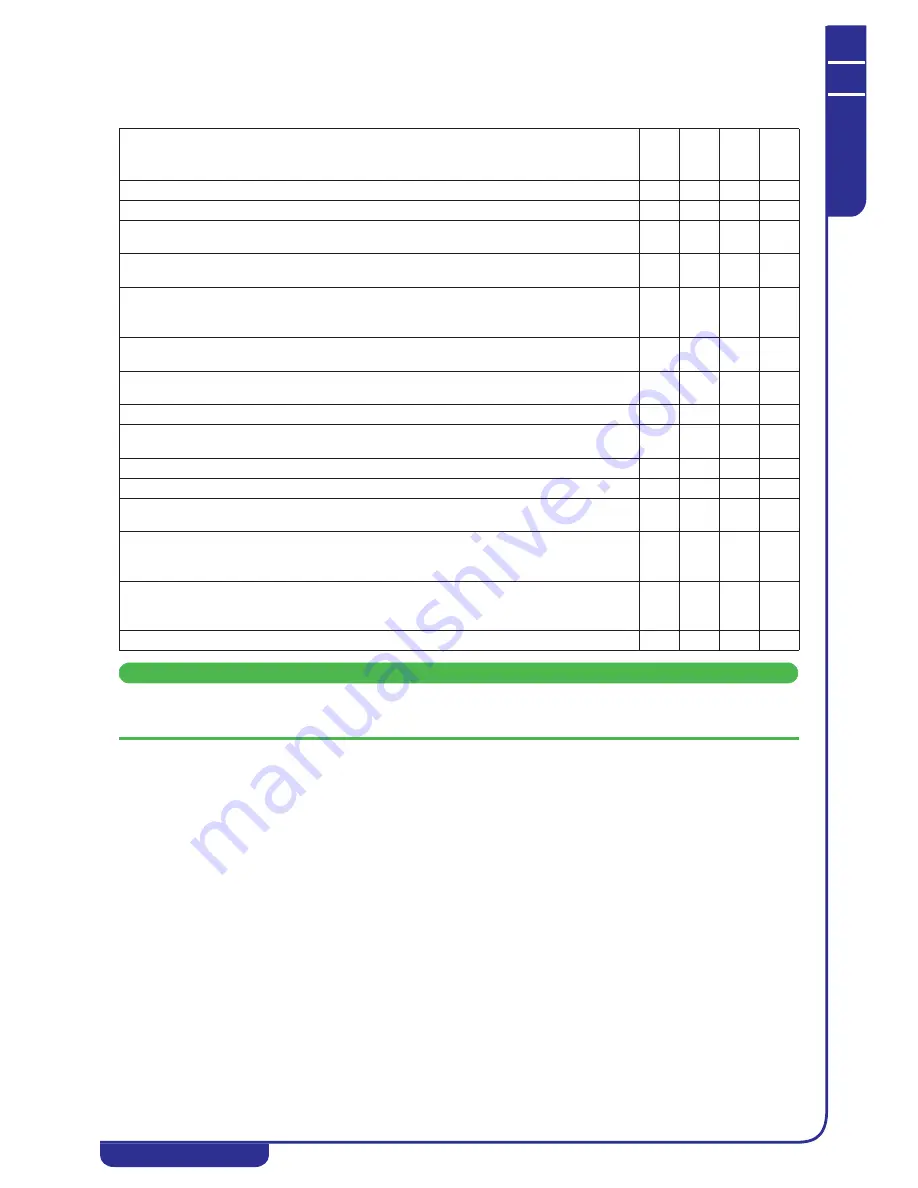
OPERATING AND MAINTENANCE MANUAL
Operation and maintenance
MCCY - CY 013÷301
56
ENGLISH
EN
The data in this manual are not binding and they can be modified by the manufacturer without notice.
Reproduction of this manual is strictly prohibited.
9 . 3
M a i n t e n a n c e s c h e d u l e
ATTENTION
This plan is based on an average working situation.
In some installations it may be necessary to increase the frequency of maintenance.
OPERATION
1 day
1 m
onth
6 months
1 y
ear
Check for any alarm signals.
¡
Check that the water outlet temperature is within the envisaged range.
¡
Check that the water inlet temperature is in accordance with the value used for selecting the
unit.
¡
In units with hydraulic group check that the pressure in the tank (with pump stopped) is about
0.5 bar.
¡
In units with hydraulic group check that the difference between the pump outlet pressure and
inlet pressure (measured by a pressure gauge with the pump stopped) is within the limits
envisaged and, in particular, is not lower than the value corresponding to the maximum flow.
¡
Clean the water filter (if installed).
We recommend to clean the filter after a week from the unit starting.
¡
Check that the liquid indicator (if present) is full or with a small stream of bubbles when the
compressor is running.
¡
Check that the unit current absorption is within the values on the data plate.
¡
Carry out visual inspection of refrigerant circuit, looking out for any deterioration of the
piping or any traces of oil which might indicate a refrigerant leak.
¡
Check the condition and security of piping connections.
¡
Check the condition and security of electrical connections.
¡
Using a spanner, check that the connections between the compressor inlet and outlet piping
have not slackened.
¡
Check that the ambient air temperature is in accordance to the value used for selecting the
machine (normally 30-35°C / 77-86°F).
Check that the ambient is well ventilated.
¡
Check that the fan operation is automatically started up.
Clean the condenser fins with a soft sponge or a jet of clean compressed air.
Check that the grilles of the unit are free from dirt and any other obstructions.
¡
Clean condenser fins with a mild detergent.
¡
Summary of Contents for MCCY-CY013 301
Page 68: ......