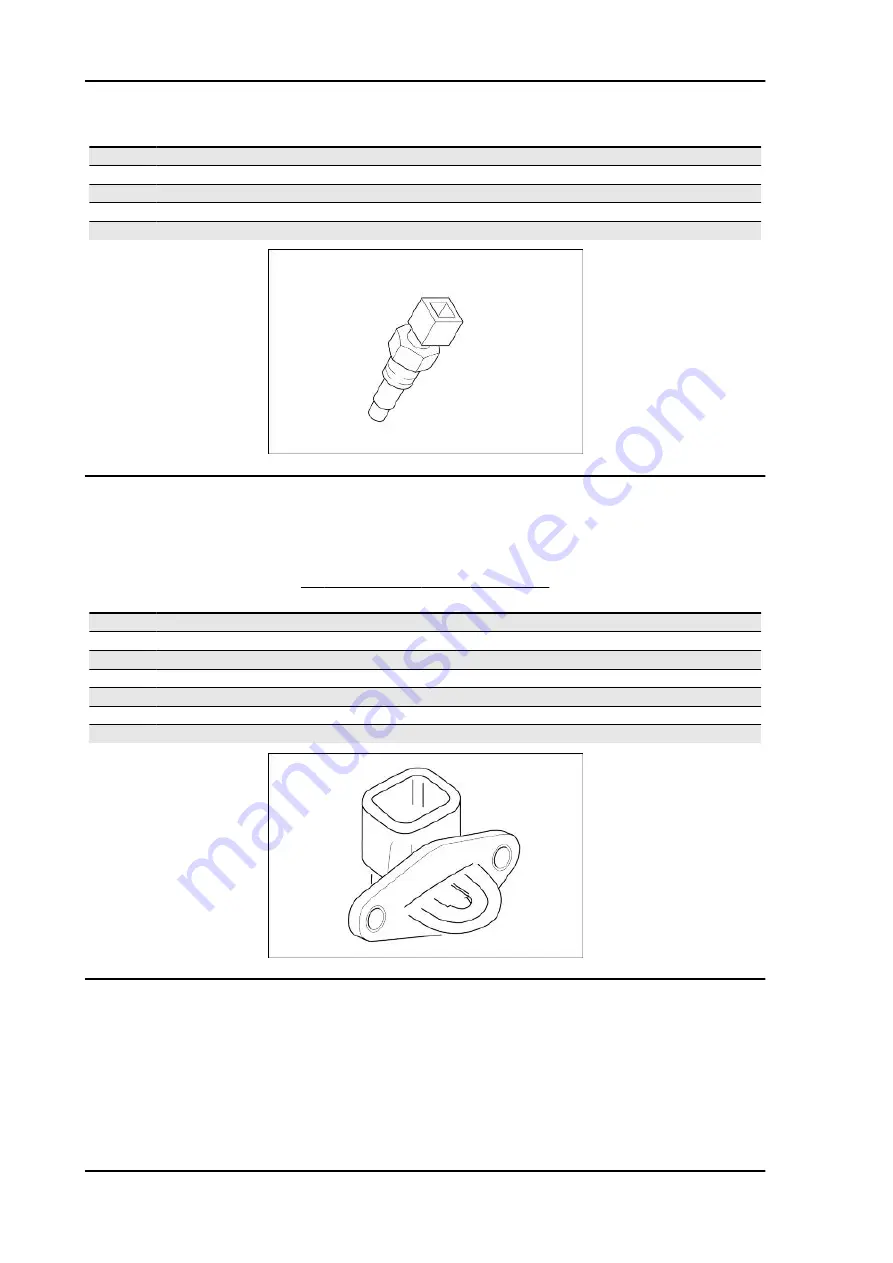
Specification
Desc./Quantity
13
Resistance at +80 °C (176 °F)
0.380 kOhm
14
Resistance at +90 °C (194 °F)
0.280 kOhm
15
Resistance at +100 °C (212 °F)
0.204 kOhm
16
Resistance at +110 °C (230 °F)
0.153 kOhm
17
Resistance at +120 °C (257 °F)
0.102 kOhm
Air temperature sensor
NTC type sensor
A
IR
TEMPERATURE
SENSOR
RESISTANCE
Specification
Desc./Quantity
1
Resistance at -40 °C (-104 °F)
100.950 kOhm
2
Resistance at 0 °C (32 °F)
9.750 kOhm
3
Resistance at 10 °C (50 °F)
5.970 kOhm
4
Resistance at 20 °C (68 °F)
3.750 kOhm
5
Resistance at 30 °C (86 °F)
2.420 kOhm
6
Resistance at 40 °C (104 °F)
1.600 kOhm
7
Resistance at 90 °C (194 °F)
0.280 kOhm
Electrical system
STELVIO 4V - 1200
ELE SYS - 4
Summary of Contents for Stelvio 1200 4V
Page 1: ...SERVICE STATION MANUAL 981063 STELVIO 4V 1200...
Page 4: ......
Page 6: ......
Page 7: ...INDEX OF TOPICS CHARACTERISTICS CHAR...
Page 16: ...Characteristics STELVIO 4V 1200 CHAR 10...
Page 17: ...INDEX OF TOPICS MAINTENANCE MAIN...
Page 20: ...Maintenance STELVIO 4V 1200 MAIN 4...
Page 21: ...INDEX OF TOPICS ELECTRICAL SYSTEM ELE SYS...
Page 27: ...INDEX OF TOPICS ENGINE ENG...
Page 28: ...Gearbox Diagram Key 1 Ball bearing Engine STELVIO 4V 1200 ENG 2...
Page 36: ...Remove the forks and collect the shaft Engine STELVIO 4V 1200 ENG 10...
Page 108: ...Engine STELVIO 4V 1200 ENG 82...
Page 109: ...INDEX OF TOPICS POWER SUPPLY P SUPP...
Page 119: ...INDEX OF TOPICS CHASSIS CHAS...