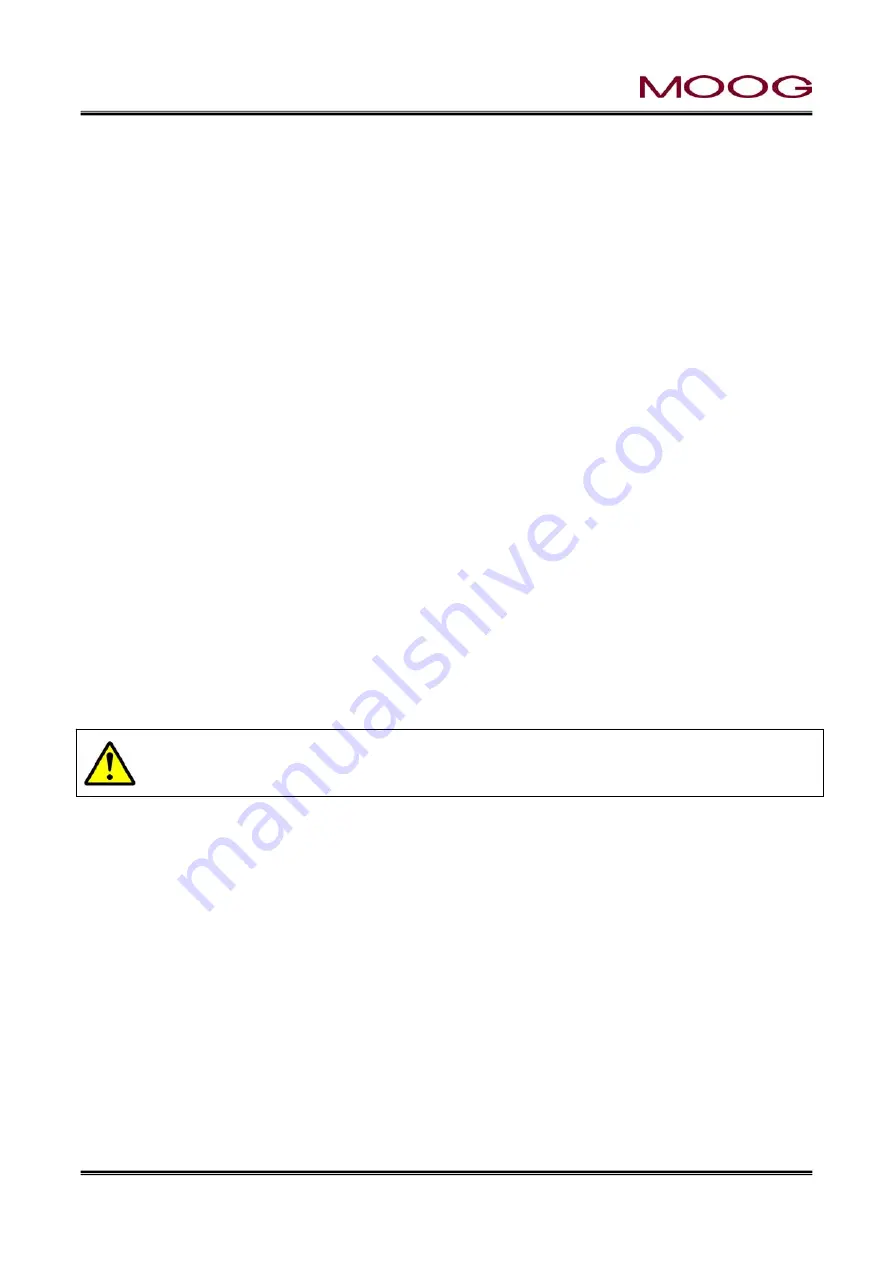
© MOOG 2010
This document is subject to MOOG INTELLECTUAL AND PROPRIETARY INFORMATION LEGEND . The details are on page II.
29
MRJ04410
DigiPackⅡ Manual, Installation and Maintenance
1-7.
TOOLING SYSTEM SETUP
1-7-1.
GENERAL
The Mechanical and Electrical installation must be finished before the Dig Gap Tooling position control
system can be set up. In addition the, hydraulic system must have been flushed for at least 24 hours.
The Die Gap Tooling position control system setup involves several steps:
1)
The Machine setup in the DigiPackⅡdisplay (F4+Set) must be set to match various options
determined by the blow molding machine and tooling head type.
2)
The correct tooling type selection, Convergent or Divergent, must be determined. This will be
determined by which portion of the tooling moves, the die or mandrel, as well as its internal
shape.
3)
The DigiPackⅡmust know if the blow molding machine is a Accumulator or a Continuous
molding machine.
4)
The working Die Gap end positions, closed and maximum open, must be set.
5)
The responsiveness of the Die Gap Tooling position control system is measured and opti-
mized.
When finished with the Die Gap Tooling system setup, the blow molding machine will be ready to be pro-
grammed for production containers.
The hydraulic pressure must be lowered during the setup procedure or the die gap tooling may be
damaged.
1-7-2.
MACHINE SETTINGS (F4+Set)
At the DigiPackⅡdisplay “F4+Set” (“
Figure 1-31
”) is Setting for Machine setting. Set these parameters
according to Machine type, these parameters should setting before start setting any parameter of tooling
and accumulator. (Accumulator setting only accumulator machine)
The settings required now are:
1)
Machine type
- Either Continuous or Accumulator
2)
Servovalve type
– Either mechanical feedback, MFB, or electrical feedback, EFB
3)
Valve current
– If selected MFB type, this parameter can be selected current level
10, 20, 50 or 100 mA
4)
Core sensor
- Either DCDT or SSI
5)
Output mode select - Either EFB/MFB or Pulse