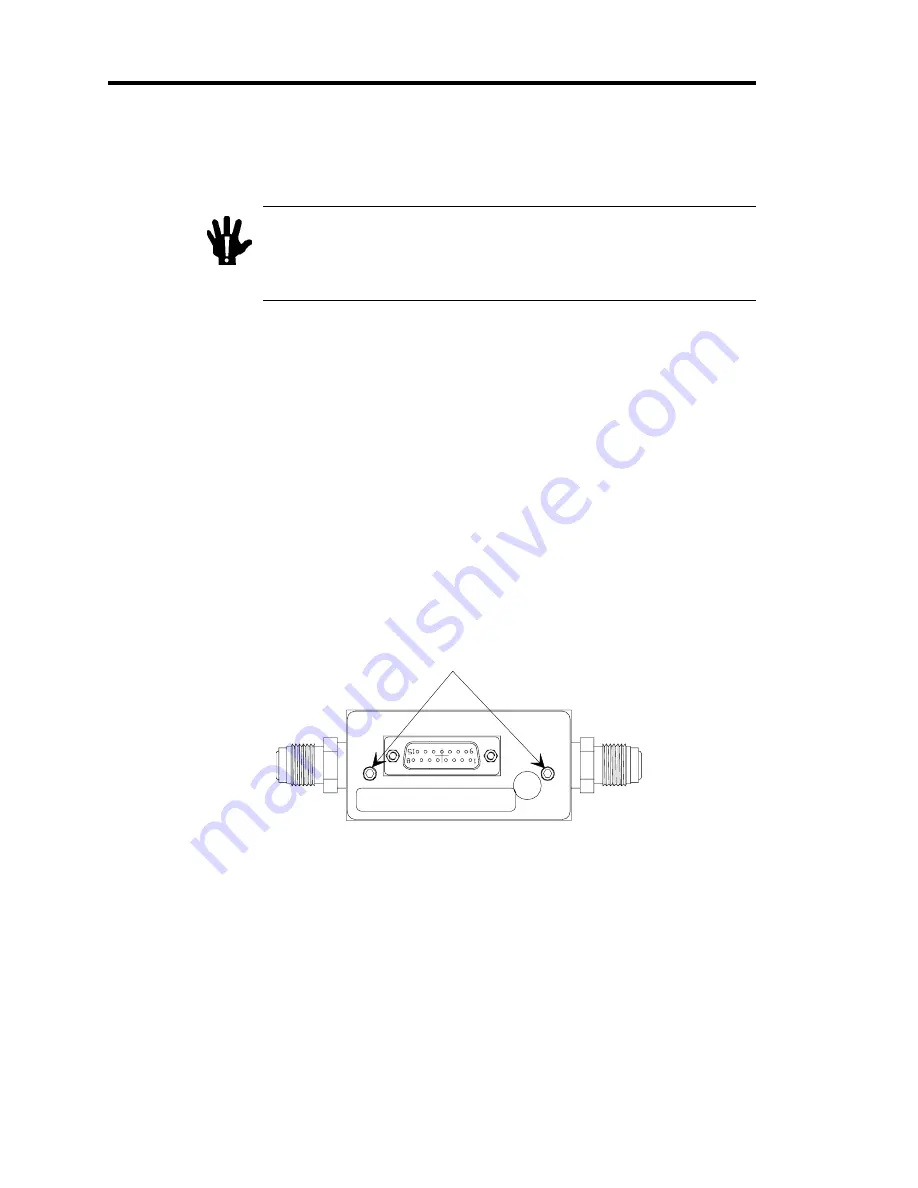
How To Adjust the Valve Preload
Chapter Seven: Troubleshooting
38
1. Set your processing system to supply the MFC with a non-hazardous gas (Ar, N
2
, or He)
and purge thoroughly.
Warning
You MUST use a “safe” gas while making any valve
adjustments to safeguard against inadvertent exposure to
any toxic or hazardous gas. DO NOT adjust the valve while a
hazardous or toxic gas is flowing through the MFC.
If you cannot use a “safe” gas within your processing system, remove the MFC and
purge the unit as required by your corporate policies and any appropriate safety
procedures.
2. Disconnect the cable to power down the unit and remove the unit from the process tool.
3. Connect the inlet of the unit to the gas supply and adjust the pressure to the maximum
level used on the process tool.
Choose a “safe” gas with a similar molecular weight as the actual process gas. More
specifically, helium is best used as a substitute for other very light gases such as
hydrogen.
4. Use a
3
/
32
” allen wrench to remove the enclosure retaining screws. Remove the enclosure
cover.
Figure 8 shows the location of the retaining screws.
Enclosure Retaining Screws
Figure 8: Location of the Retaining Screws
5. Disconnect the leads from the control valve to the PC board.
6. Remove the two (2) 4-40 socket head cap screws and the two (2) 2-56 Phillips head
screws (holding the PC brackets). Gently lay the bracket/PC board assembly on the
bench top.
Handle the unit carefully to avoid damaging the flex print that connects the sensor and
the main PC board.
Summary of Contents for Mass-Flo 1479A
Page 3: ...119474 P1 Rev B 10 97 MKS Type 1479A Mass Flo Controller ...
Page 8: ...Table of Contents vi ...
Page 10: ...List of Figures and Tables viii ...
Page 34: ...Control Valve Chapter Three Overview 24 This page intentionally left blank ...
Page 40: ...The Optional Input Chapter Four Operation 30 This page intentionally left blank ...
Page 44: ...Zero Adjustment Chapter Six Maintenance 34 This page intentionally left blank ...
Page 70: ...Model Code Appendix D Model Code 60 This page intentionally left blank ...