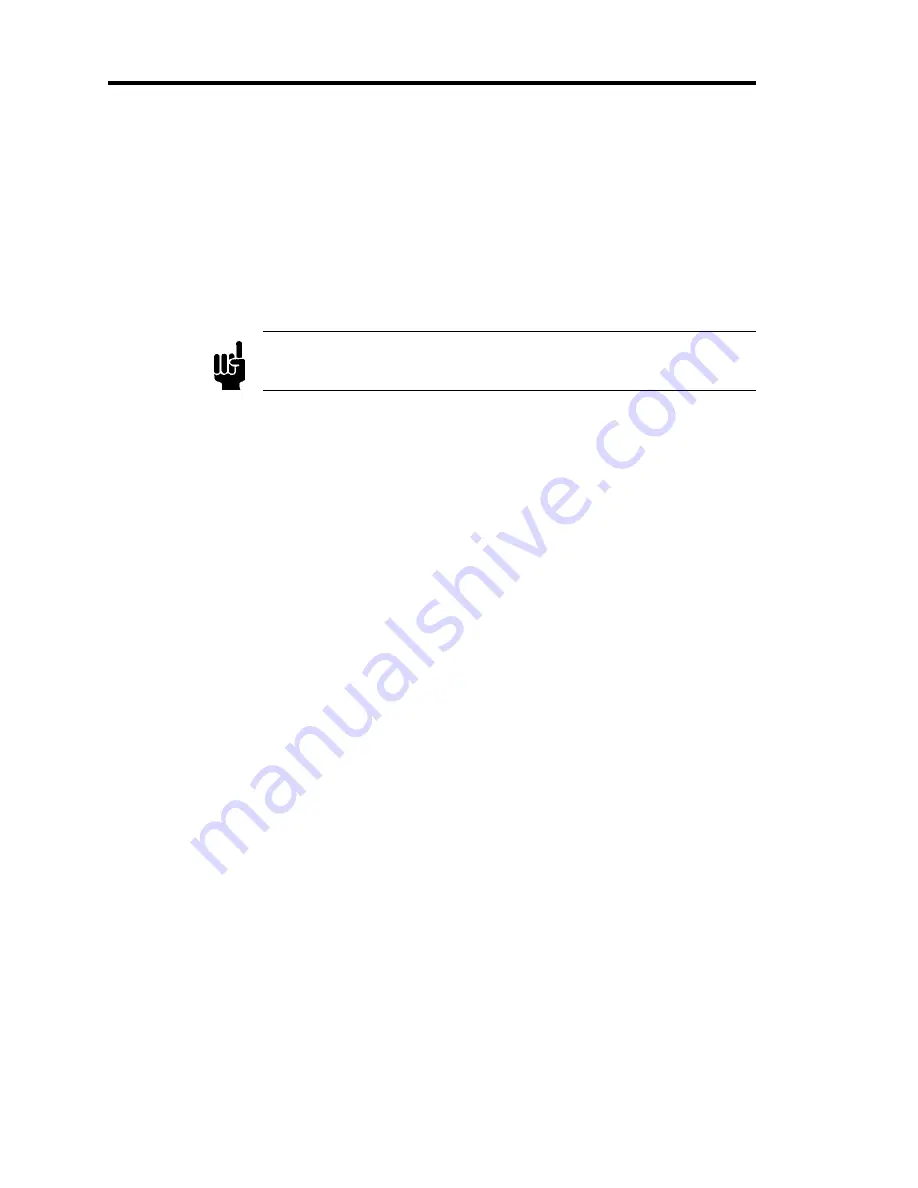
The I/O Connector
Chapter Two: Installation
14
Set Point Input (Pin 8)
The set point input signal can be a 0 to 5 Volt (factory setting) or 0 to 10 Volt signal. The range
of the set point input signal must match the range of the pressure output signal. The 640
controller is initially configured for a 0 to 5 Volt pressure output signal. Therefore, the set point
input signal must be 0 to 5 Volts, where 5 Volts represents 100% of full scale. To change the
range of the pressure output signal to 0 to 10 Volts, you must reposition jumpers on the
Transducer board. Refer to How To Change the Pressure Output Signal Range, page 50, for
instructions on changing the pressure output range.
Note
For downstream control applications, the 640 controller must have
sufficient pressure on its inlet side to achieve the set point.
Optional Input (Pin 10)
Use pin 10 to re-introduce another signal, such as a zero corrected pressure signal, into the
control circuitry of the 640 Series controller. The corrected signal introduced on pin 10 overrides
the pressure transducer signal (pin 2), and is sent to the control loop circuitry.
The Trip Point Pins (Pins 13 and 14)
The 640 Series controller offers two alarm trip points; Trip Point A and Trip Point B. Each trip
point has an LED and adjustment pot on the top cover. The trip points are NPN open collector
transistors.
The trip points can be set from 1 to 100% of full scale by adjusting the appropriate trip point pot
located on the top of the unit. The trip point setting is a 0 to 5 VDC signal available on the side
of the unit.
Use the appropriate trip point output signal to control a relay or another piece of equipment, such
as a valve, or as a digital input to a computer. The trip point signal is pulled to ground when the
trip point is on. The voltage value of the pin is 5 Volts when the respective trip point is off.
Refer to Trip Points, page 41, for a complete description of the trip points..
Summary of Contents for 640A/641A
Page 4: ...116669 P1 Rev C 12 99 MKS Type 640A 641A Pressure Controller...
Page 9: ...Table of Contents vi...
Page 11: ...List of Figures viii...
Page 13: ...List of Tables x...
Page 21: ...Customer Support Chapter One General Information 8 This page intentionally left blank...
Page 45: ...Initial Configuration Chapter Two Installation 32 This page intentionally left blank...
Page 85: ...Model Code Description Appendix D Model Code Explanation 72 This page intentionally left blank...