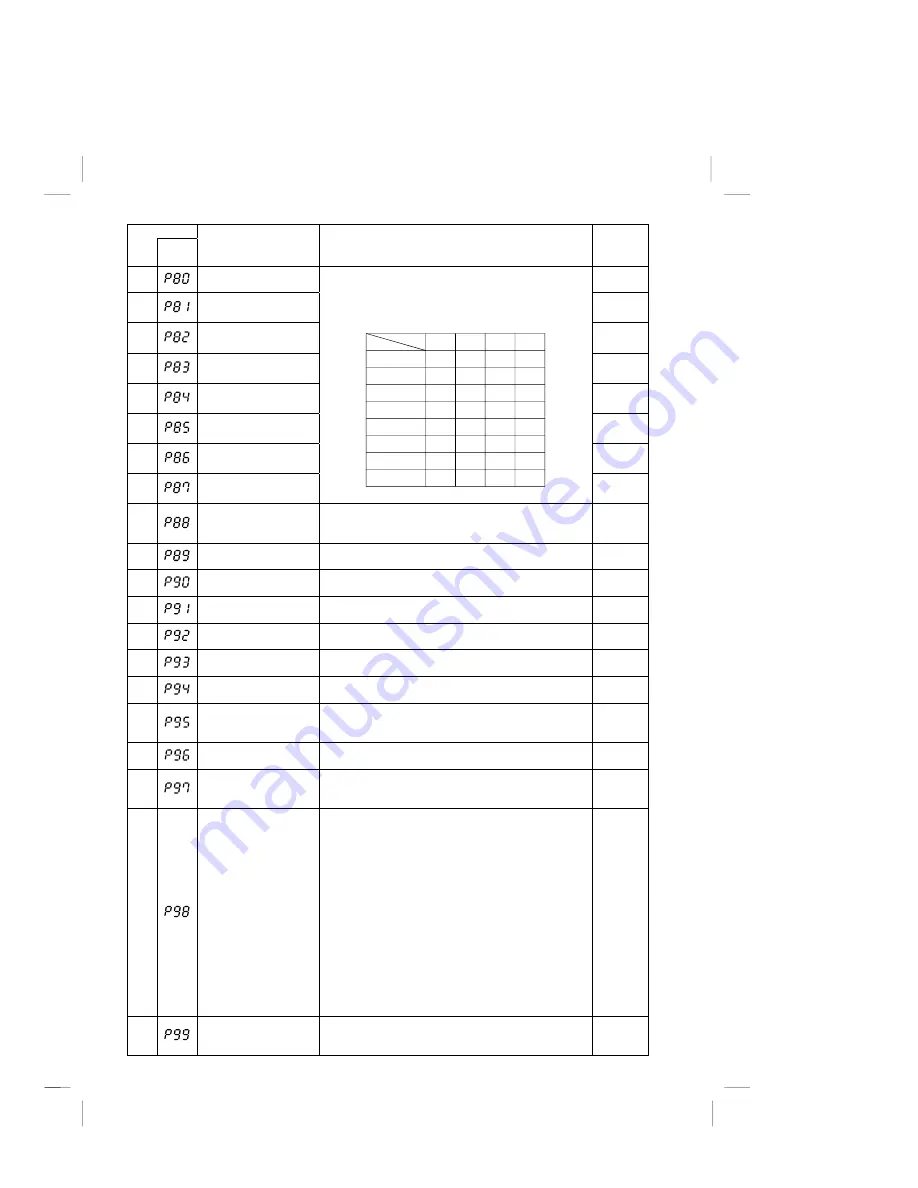
33
Parameter
Indica-
tion
Name
Outline
Factory
Setting
80
Multi-speed setting
(speed 8)
- - -
81
Multi-speed setting
(speed 9)
- - -
82
Multi-speed setting
(speed 10)
- - -
83
Multi-speed setting
(speed 11)
- - -
84
Multi-speed setting
(speed 12)
- - -
85
Multi-speed setting
(speed 13)
- - -
86
Multi-speed setting
(speed 14)
- - -
87
Multi-speed setting
(speed 15)
Setting other than "- - -" specifies speeds 8 to 15.
By combining ON and OFF of the contact
signals (RH, RM, RL, REX signals), the running
speed can be changed step-by-step.
Use Pr. 63 to assign the REX signal.
RH RM RL
ON
ON
ON
ON
REX
ON
ON
ON
ON
ON
ON
ON
ON
ON
ON
ON
ON
ON
ON
ON
ON
Speed 8
Speed 9
Speed 10
Speed 11
Speed 12
Speed 13
Speed 14
Speed 15
OFF
OFF
OFF
OFF OFF OFF
OFF
OFF
OFF
OFF
OFF
OFF
0 to 120Hz, - - -
- - -
88
PID action selection
Used to choose the operation of PID control.
20: PID reverse action,
21: PID forward action
20
89
PID proportional
band
Used to set the proportional band for PID control.
0.1 to 999%, - - -
100%
90
PID integral time
Used to set the integral time for PID control.
0.1 to 999s, - - -
1s
91
PID upper limit
Used to set the upper limit value for PID control.
0 to 100%, - - -
- - -
92
PID lower limit
Used to set the lower limit value for PID control.
0 to 100%, - - -
- - -
93
PID action set point
for PU operation
Used to set the PID action set point for PU operation.
0 to 100%
0%
94
PID differential time
Used to set the differential time for PID control.
0.01 to 10s, - - -
- - -
95
Rated motor slip
Used to set the rated motor slip to make slip
compensation.
0 to 50%, - - -
- - -
96
Slip compensation
time constant
Used to set the response time of slip compensation.
0.01 to 10s
0.5s
97
Constant-output region
slip compensation
selection
Used to choose whether slip compensation is
made or not in the constant-output region.
0, - - -
- - -
98
Automatic torque
boost selection
(Motor capacity)
You can set the motor capacity and exercise
automatic torque boost control.
"- - -" specifies V/F control.
Set the motor capacity used.
•
The motor capacity should be equal to or
one rank lower than the inverter capacity.
•
The number of motor poles should be 2, 4 or
6. (Only 4 poles for constant-torque motor)
•
Single-motor operation (one motor run by
one inverter) should be performed.
•
Wiring length from inverter to motor should
be within 30m (98.43feet).
When using a constant-torque motor, set "1" in
Pr. 71.
<Example> For 1.5kW, set "1.5".
0.1 to 3.7kW, - - -
- - -
99
Motor primary
resistance
You can set the motor's primary resistance value.
(Normally, this parameter need not be set.)
0 to 50
Ω
, - - -
- - -