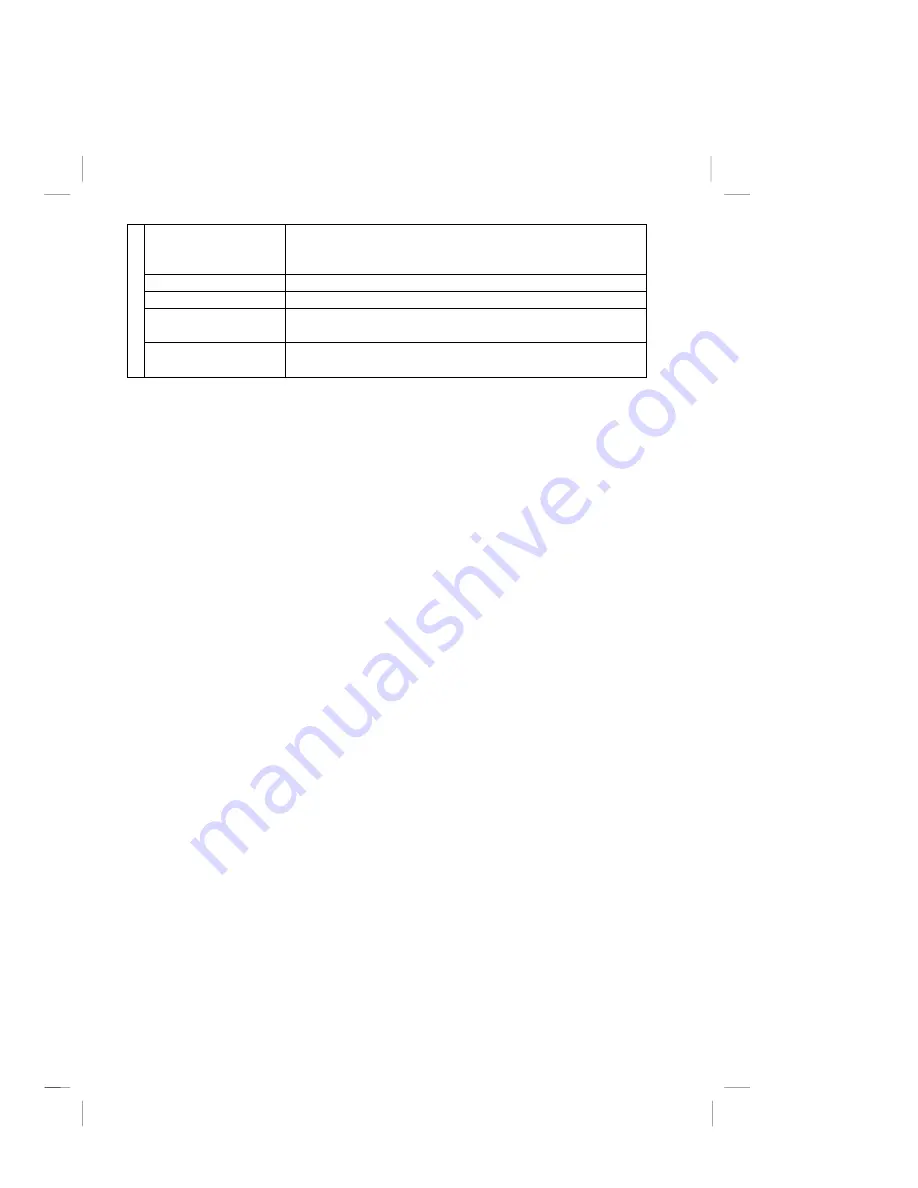
43
Ambient temperature
-10
°
C to +50
°
C (14
°
F to 122
°
F) (non-freezing)
(-10
°
C to +40
°
C (14
°
F to 104
°
F) for totally-enclosed structure
feature)
Ambient humidity
90%RH max. (non-condensing)
Storage temperature
-20
°
C to +65
°
C (-4
°
F to +149
°
F)
Atmosphere
Indoors (without corrosive gas, flammable gas, oil mist, dust
and dirt etc.)
Envi
ronm
ent
Altitude/vibration
Max. 1000m (3280.80feet) above seal level, 5.9m/s
2
or less
(conforms to JIS C 0911)
*1. When undervoltage occurs, no alarm output is provided but the output is
shut off. After power restoration, the inverter may be run as it is. Depending
on the running status (e.g. load magnitude), however, overcurrent,
regenerative overvoltage or other protection may be activated at power
restoration. (In external operation mode.)
*2. The magnitude of braking torque indicates the short-duration average
torque (which changes with the motor loss) developed when the motor
alone is decelerated from 60Hz in the shortest period, and is not continuous
regenerative torque. Deceleration made from a high speed above the base
frequency will reduce the value of average deceleration torque.
*3. This function is valid for only the type with RS-485 communication function.
*4. Compatible with only the product having the built-in cooling fan.
*5. Activated only when "1" is set in Pr. 40 "start-time ground fault detection
selection".
*6. Activated only when external thermal relay input (OH) is selected in any of
Pr. 60 to Pr. 63 (input terminal function selection).