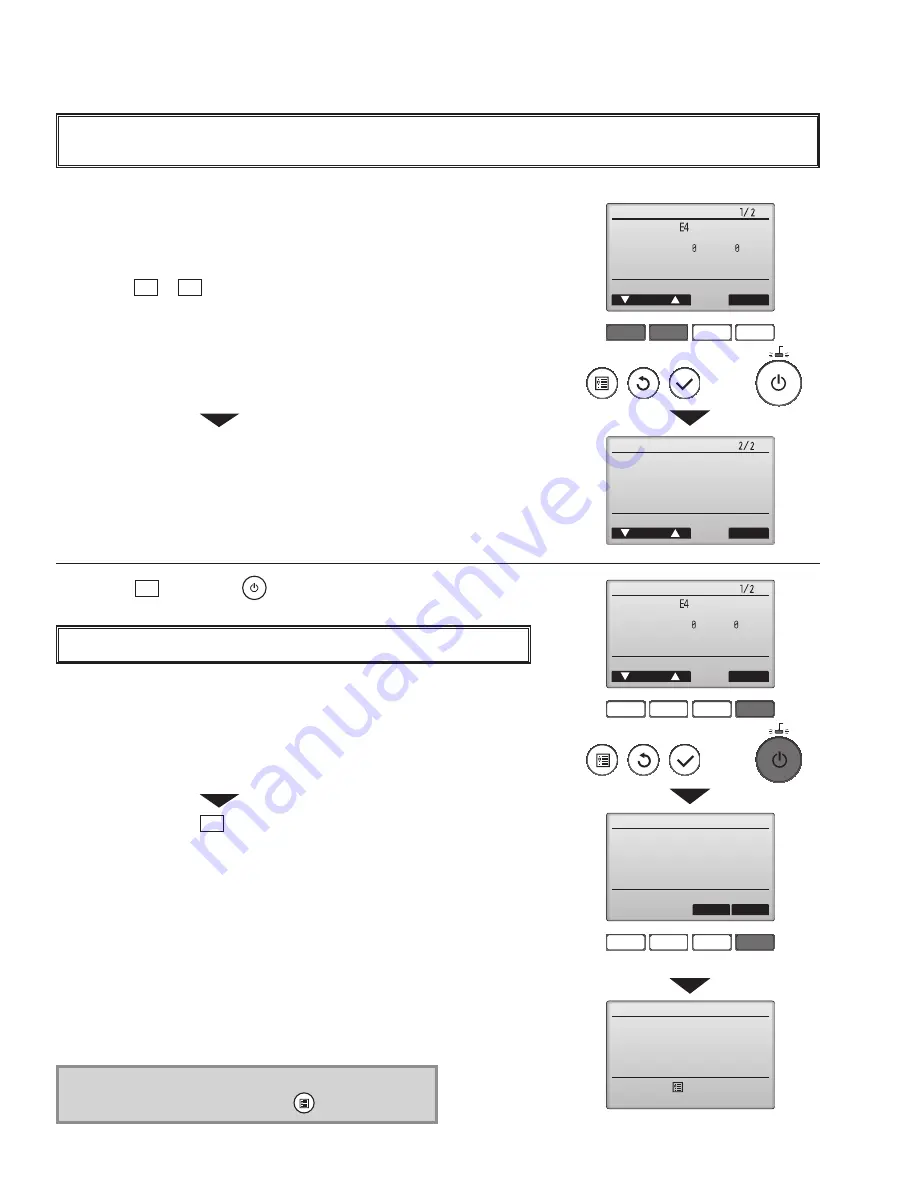
26
F1
F2
F3
F4
Error information
Error code
Error unit IU
Ref. address Unt#
Model name
Serial No.
Reset
Page
Error information
Contact information
Dealer
Tel
Reset
Page
Reset error: Reset button
Reset error: Reset button
blinks
1
Check code, error unit, refrigerant address, unit model name, and serial
number will appear.
The model name and serial number will appear only if the information has
been registered.
Press the F1 or F2 button to go to the next page.
When an error occurs, the following screen will appear.
Check the error status, stop the operation, and consult your dealer.
Contact information (dealer's phone number) will appear if the information has
been registered.
F1
F2
F3
F4
F1
F2
F3
F4
Error information
Error reset
Error reset
Error code
Error unit IU
Ref. address Unt#
Model name
Serial No.
Reset
Page
Reset current error?
Error reset
OK
Cancel
Main menu:
Reset error: Reset button
blinks
2
Press the F4 button or the
button to reset the error that is occurring.
Errors cannot be reset while the ON/OFF operation is prohibited.
Select "OK" with the F4 button.
Navigating through the screens
• To go back to the Main menu ..........
button
<Error information>
OCH636A
Summary of Contents for PUY-A12NKA7
Page 119: ...119 OCH636A ...