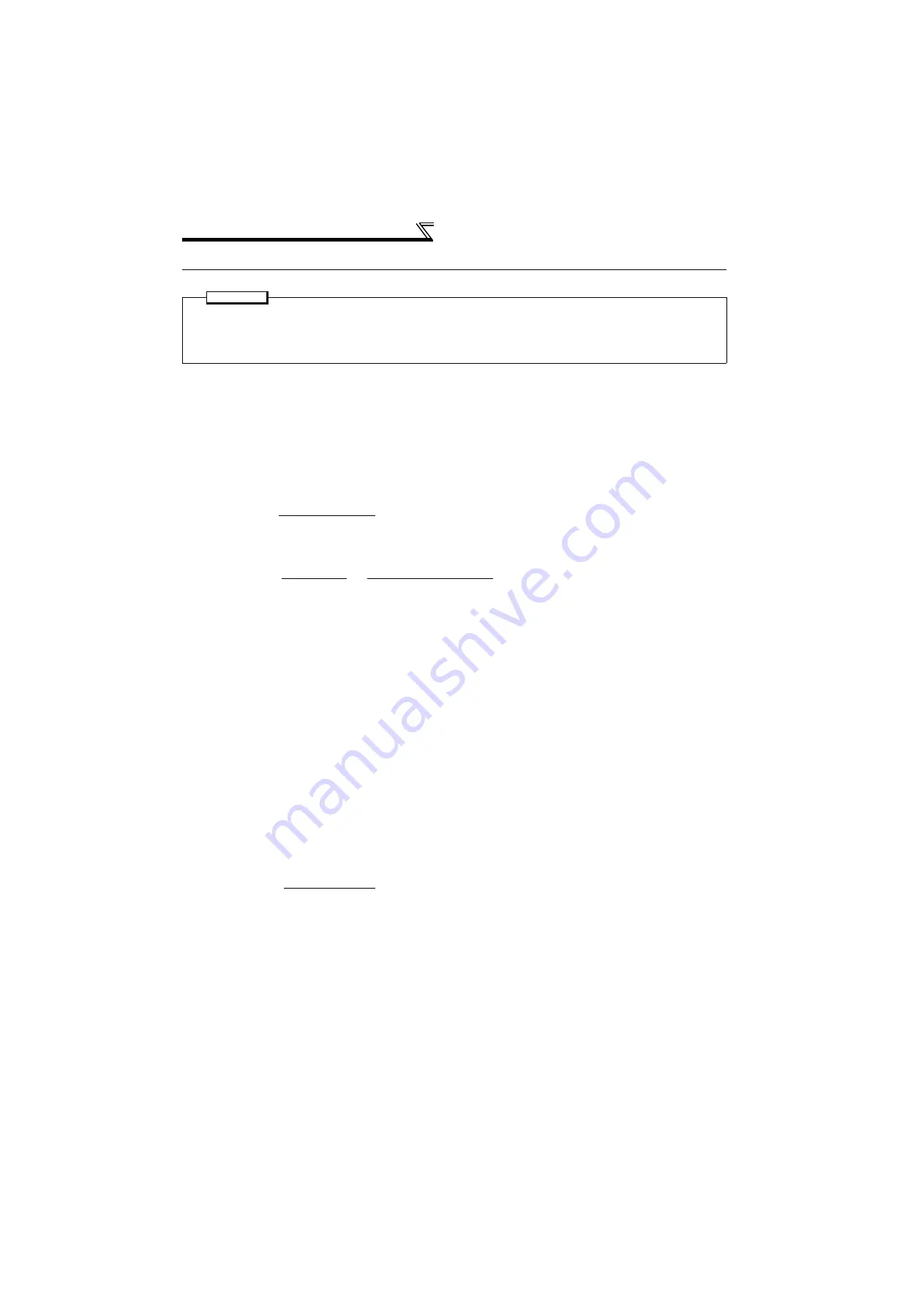
32
Winding diameter compensation
function
3.8 Winding diameter compensation function
3.8.1
Winding diameter calculation and compensation by winding diameter calculation
(1) Winding diameter calculation
1) Winding diameter calculation using line speed
Calculate winding diameter "D" from input line speed "V" and main speed (actual speed).
(Example) Calculation when line speed V = 409.9m/min
actual motor speed
fb = 659.0r/min
gear ratio Z = 0.396
2) Winding diameter calculation using addition of material thickness
Calculate winding diameter "D" from winded (unwinded) material thickness "d".
(2) Target line speed
Calculate target line speed "V*", which is desired to be constant, from main speed setting "
*" and initial diameter.
(3) Main speed compensation amount calculation
Calculate main speed compensation amount from the diameter "D", which is obtained from winding diameter
calculation (or from stored winding diameter), and target line speed "V*", which is desired to be constant.
POINT
Turn X83 signal ON to perform dancer control, tension control and winding diameter compensation.
When X83 signal is OFF, dancer control, tension control and winding diameter compensation are not performed.
To disable dancer control and perform winding diameter compensation only, turn ON X83 signal and X85 together.
Set "83 (X83)" or "85 (X84)" in
Pr. 178 to Pr. 189 (input terminal function selection)
to assign X83 and X85 signals.
D
fb
Z = V
V : line speed
fb : actual motor speed
D=
V
fb
Z
Z : gear ratio
D=
V
=
409.9[m/min]
1000
= 499.97[mm]
fb
Z
659.0[r/min]
0.396
D = D1
2
d
N
Z
D1 : initial diameter
d : material thickness
N : roll rotation number
Z : gear ratio
V* =
D1
*
Z
* : main speed setting (r/min)
D1 : initial diameter
Z : gear ratio
=
V*
D
Z
: main speed compensation
D
: winding diameter calculation result (stored winding diameter)
V*
: line speed which is desired to be constant
Z
: gear ratio