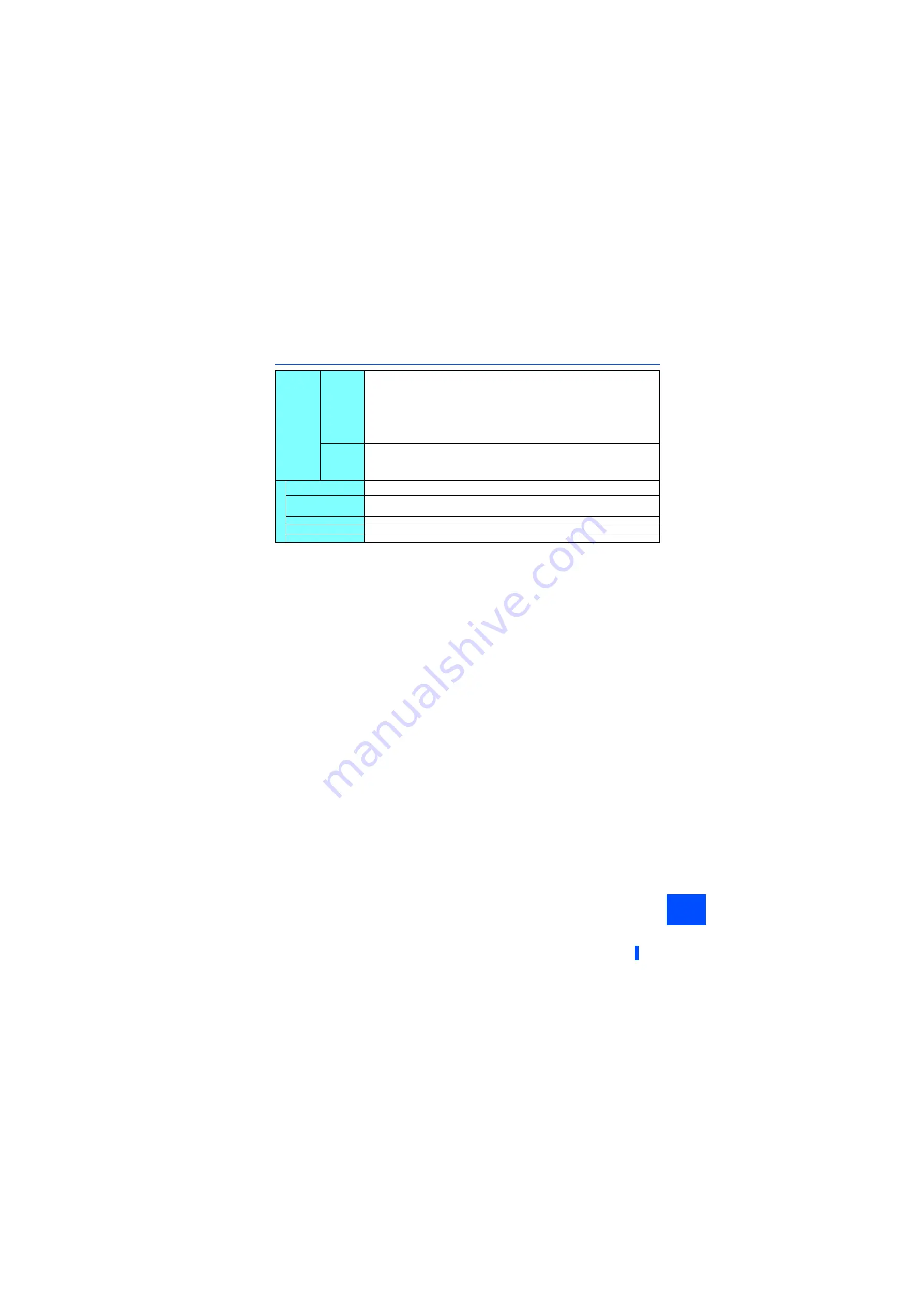
Common specifications
77
4
Available only when a vector control compatible option is installed.
For PM sensorless vector control, refer to the Instruction Manual (Detailed) of the FR-A800 inverter.
In the initial setting of the FR-A820-00340(5.5K) or higher and the FR-A840-00170(5.5K) or higher, it is limited to 150% by the torque limit level.
Enabled only for standard models and IP55 compatible models.
This protective function is not available in the initial status.
Enabled only for standard models.
Available for the IP55 compatible model only.
Temperature applicable for a short time, e.g. in transit.
For the installation at an altitude above 1000 m (up to 2500 m), consider a 3% reduction in the rated current per altitude increase of 500 m.
2.9 m/s
2
or less for the FR-A840-04320(160K) or higher.
Protective/
warning
function
Protective
function
Overcurrent trip during acceleration, Overcurrent trip during constant speed, Overcurrent trip during deceleration or stop,
Regenerative overvoltage trip during acceleration, Regenerative overvoltage trip during constant speed, Regenerative
overvoltage trip during deceleration or stop, Inverter overload trip, Motor overload trip, Heatsink overheat, Instantaneous
power failure
, Undervoltage
, Input phase loss
, Stall prevention stop, Loss of synchronism detection
, Brake
transistor alarm detection
, Output side earth (ground) fault overcurrent, Output short circuit, Output phase loss, External
thermal relay operation
, Option fault, Communication option fault, Parameter storage device
fault, PU disconnection, Retry count excess
, CPU fault, Operation panel power supply short circuit, 24 VDC power fault,
Abnormal output current detection
, Inrush current limit circuit fault
, Ethernet communication fault
, Analog input fault,
USB communication fault, Safety circuit fault, Overspeed occurrence
, Speed deviation excess detection
, Signal loss
detection
, Excessive position fault
, Encoder phase fault
, Pre-charge
fault
, PID signal fault
, Option fault, Opposite rotation deceleration fault
, Internal circuit fault, Abnormal internal
temperature
, Magnetic pole position unknown
Warning
function
Fan alarm, Stall prevention (overcurrent), Stall prevention (overvoltage), Regenerative brake pre-alarm
, Electronic
thermal relay function pre-alarm, PU stop, Speed limit indication
, Parameter copy, Safety stop, Maintenance timer 1 to
3
, USB host error, Home position return setting error
, Home position return uncompleted
, Home position return
parameter setting error
, Password locked
, Parameter write error, Copy operation error, 24 V
external power supply operation, Internal fan alarm
, Continuous operation during communication fault, Ethernet
communication fault
Env
ir
onme
n
t
Surrounding air
temperature
-10°C to +50°C (non-freezing) (LD, ND, HD ratings)
-10°C to +40°C (non-freezing) (SLD rating, IP55 compatible model)
Surrounding air humidity
95% RH or less (non-condensing) (With circuit board coating (conforming to IEC60721-3-3 3C2/3S2), IP55 compatible
model)
90% RH or less (non-condensing) (Without circuit board coating)
Storage temperature
-20°C to +65°C
Atmosphere
Indoors (without corrosive gas, flammable gas, oil mist, dust and dirt, etc.)
Altitude/vibration
1000 m or lower
, 5.9 m/s