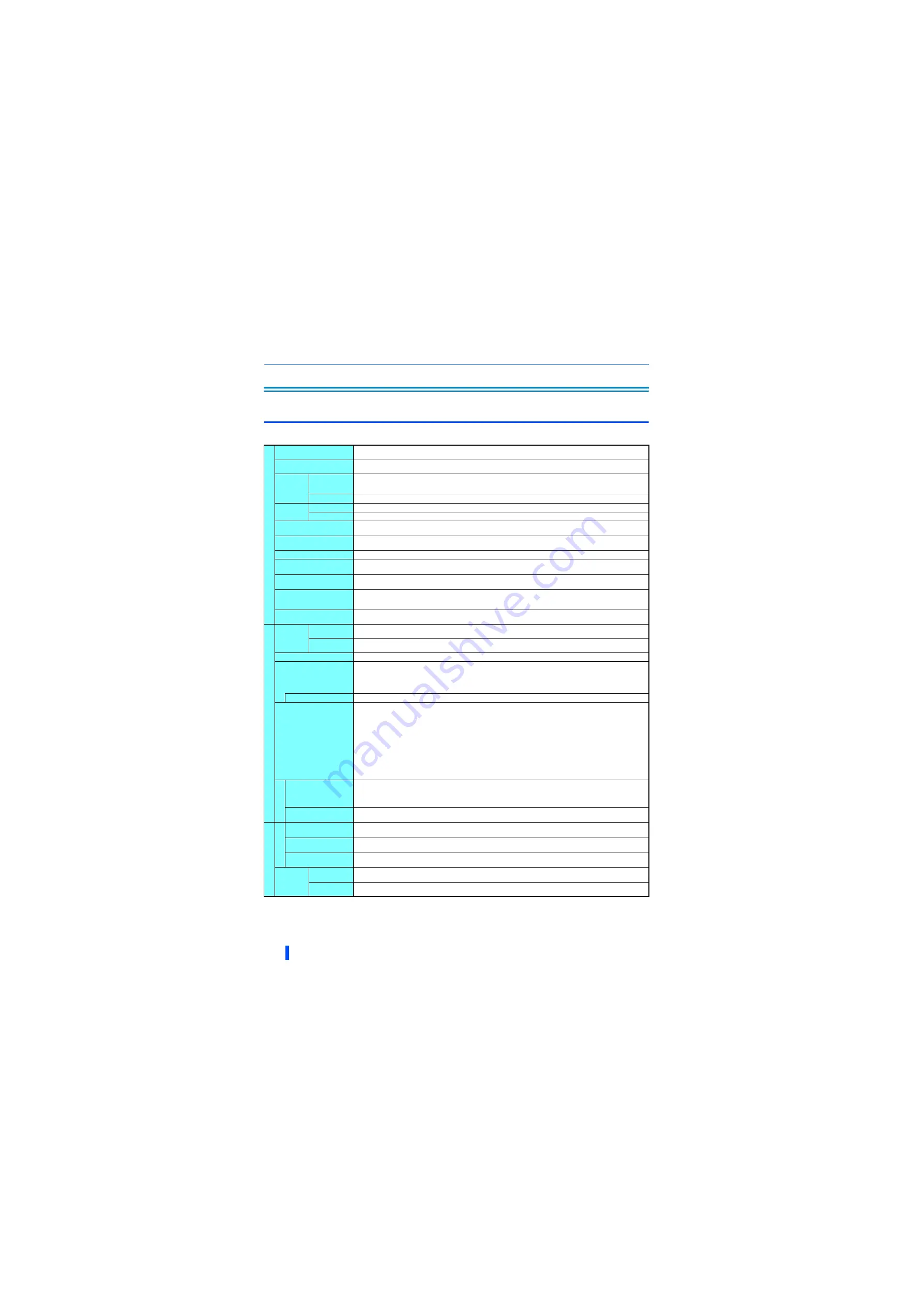
Common specifications
76
4
SPECIFICATIONS
4.1
Common specifications
FR-A800-E
Co
ntr
o
l spe
c
if
ic
at
ions
Control method
Soft-PWM control, high carrier frequency PWM control (selectable among V/F control, Advanced magnetic flux vector
control, Real sensorless vector control), Optimum excitation control, vector control
, and PM sensorless vector control
Output frequency range
0.2 to 590 Hz (The upper-limit frequency is 400 Hz under Advanced magnetic flux vector control, Real sensorless vector
control, vector control
, and PM sensorless vector control.)
Frequency
setting
resolution
Analog input
0.015 Hz/60 Hz (0 to 10 V/12 bits for terminals 2 and 4)
0.03 Hz/60 Hz (0 to 5 V/11 bits or 0 to 20 mA/approx. 11 bits for terminals 2 and 4, 0 to ±10 V/12 bits for terminal 1)
0.06 Hz/60 Hz (0 to ±5 V/11 bits for terminal 1)
Digital input
0.01 Hz
Frequency
accuracy
Analog input
Within ±0.2% of the max. output frequency (25°C ± 10°C)
Digital input
Within 0.01% of the set output frequency
Voltage/frequency
characteristics
Base frequency can be set from 0 to 590 Hz. Constant-torque/variable-torque pattern or adjustable 5 points V/F can be
selected.
Starting torque
SLD Rating:120% 0.3 Hz, LD Rating:150% 0.3 Hz, ND Rating:200% 0.3 Hz
, HD Rating:250% 0.3 Hz
(Real sensorless vector control, vector control
Torque boost
Manual torque boost
Acceleration/deceleration
time setting
0 to 3600 s (acceleration and deceleration can be set individually), linear or S-pattern acceleration/deceleration mode,
backlash countermeasures acceleration/deceleration can be selected.
DC injection brake
(induction motor)
Operation frequency (0 to 120 Hz), operation time (0 to 10 s), operation voltage (0 to 30%) variable
Stall prevention
operation level
Activation range of stall prevention operation (SLD rating: 0 to 120%, LD rating: 0 to 150%, ND rating: 0 to 220%,
HD rating: 0 to 280%). Whether to use the stall prevention or not can be selected. (V/F control, Advanced magnetic flux
vector control)
Torque limit level
Torque limit value can be set (0 to 400% variable). (Real sensorless vector control, vector control
, PM sensorless vector
control)
O
p
er
at
ion sp
ec
if
icat
ions
Frequency
setting
signal
Analog input
Terminals 2 and 4: 0 to 10 V, 0 to 5 V, 4 to 20 mA (0 to 20 mA) are available.
Terminal 1: -10 to +10 V, -5 to +5 V are available.
Digital input
Input using the setting dial of the operation panel or parameter unit
Four-digit BCD or 16-bit binary (when used with option FR-A8AX)
Start signal
Forward and reverse rotation or start signal automatic self-holding input (3-wire input) can be selected.
Input signals
(twelve terminals)
Low-speed operation command, Middle-speed operation command, High-speed operation command, Second function
selection, Terminal 4 input selection, Jog operation selection, Selection of automatic restart after instantaneous power
failure, flying start, Output stop, Start self-holding selection, Forward rotation command, Reverse rotation command,
Inverter reset
The input signal can be changed using
Pr.178 to Pr.189 (Input terminal function selection)
.
Pulse train input
100 kpps
Operational functions
Maximum and minimum frequency settings, multi-speed operation, acceleration/deceleration pattern, thermal protection,
DC injection brake, starting frequency, JOG operation, output stop (MRS), stall prevention, regeneration avoidance,
increased magnetic excitation deceleration, DC feeding
, frequency jump, rotation display, automatic restart after
instantaneous power failure, electronic bypass sequence, remote setting, automatic acceleration/deceleration, retry
function, carrier frequency selection, fast-response current limit, forward/reverse rotation prevention, operation mode
selection, slip compensation, droop control, load torque high-speed frequency control, speed smoothing control, traverse,
auto tuning, applied motor selection, gain tuning, RS-485 communication, Ethernet communication, PID control, PID pre-
charge function, easy dancer control, cooling fan operation selection, stop selection (deceleration stop/coasting), power-
failure deceleration stop function, stop-on-contact control, PLC function, life diagnosis, maintenance timer, current average
monitor, multiple rating, orientation control
, speed control, torque control, position control, pre-excitation, torque limit, test
run, 24 V power supply input for control circuit, safety stop function, anti-sway control
Out
put
signa
l Open collector output
(five terminals)
Relay output
(two terminals)
Inverter running, Up to frequency, Instantaneous power failure/undervoltage
, Overload warning,
Output frequency detection, Fault
The output signal can be changed using
Pr.190 to Pr.196 (Output terminal function selection)
.
Fault codes of the inverter can be output (4 bits) from the open collector.
Pulse train output
(FM type)
50 kpps
Indica
tion
For
me
te
r
Pulse train output
(FM type)
Max. 2.4 kHz: one terminal (output frequency)
The monitored item can be changed using
Pr.54 FM/CA terminal function selection.
Current output
(CA type)
Max. 20 mADC: one terminal (output frequency)
The monitored item can be changed using
Pr.54 FM/CA terminal function selection.
Voltage output
Max. 10 VDC: one terminal (output frequency)
The monitored item can be changed using
Pr.158 AM terminal function selection.
Operation
panel
(FR-DU08)
Operating
status
Output frequency, Output current, Output voltage, Frequency setting value
The monitored item can be changed using
Pr.52 Operation panel main monitor selection
.
Fault record
A fault record is displayed when a fault occurs. Past 8 fault records and the conditions immediately before the fault (output
voltage/current/frequency/cumulative energization time/year/month/date/time) are saved.