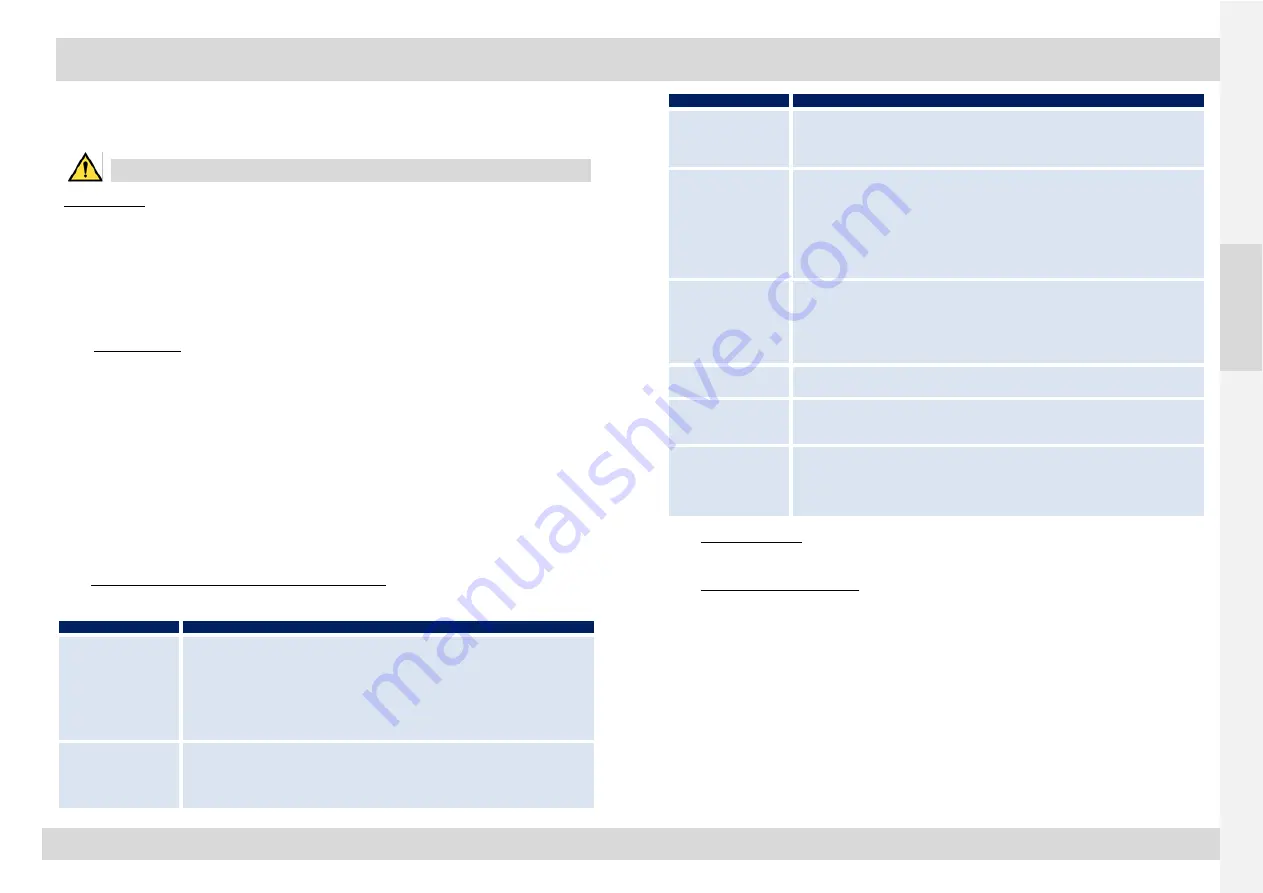
EVISA ATEX E65.R / E100.R / E200.R / E300.R
517976-04
20
EN
Oil level safety device (optional)
3.3.11.
It is possible to install a float that triggers an alarm if the oil level drops. It is mounted on the plate where
the oil level sight glass and drainage valve are installed.
When mounting the float, take care to seal the threading properly
Practical advice:
it is recommended to apply a timeout of at least 30 seconds on the alarm signal to avoid having untimely
activation (swashing of the oil).
When connecting this sensor, the manufacturer's instructions given in the appendix must be observed.
For sensor management, refer to EN80079-37 §6.5.
Electric motor
3.3.12.
The motor must only be operated by hand if there is no explosive atmosphere.
Contact an electrical motor specialist for maintenance and assistance.
Disposal of waste
3.4.
Before any dismantling operation, make sure that the pump does not present any risk generated by
substances sucked in. See safety data sheet on ANNEX.
The pump must be dismantled. Materials must be sorted, collected and recycled in accordance with local
and national safety and environmental regulations.
The main wastes to be recovered are:
Metallic materials
DEEE
Oil
Collection and recovery must be carried out by approved service providers in accordance with the
regulations in force in the country.
TROUBLESHOOTING ADVICE IN CASE OF MALFUNCTIONING
4.
Do not dismantle the pump more than necessary during repair, servicing or maintenance operations.
INCIDENT
PROBABLE CAUSE
1 - The motor cuts out.
1.1.
Mains power supply voltage or frequency incompatible with motor characteristics.
1.2.
Check the circuit breaker setting.
1.3.
Check the electrical connections.
1.4.
The oil is too viscous or the room temperature is too low.
1.5.
Rise of pressure in the exhaust unit:
- oil separating cartridge clogged,
- pump exhaust line restricted or blocked.
1.6.
Hard spot felt when pump rotated by hand: check the vanes.
2 – The pump flow rate is
too low.
2.1.
Pump inappropriate for the application.
2.2.
Suction intake screen clogged
2.3.
Suction filter (optional) clogged
2.4.
Oil separating cartridge clogged.
2.5.
Piping too long or diameter too small, causing excessive head loss.
INCIDENT
CAUSE PROBABLE
3 – Insufficient vacuum
created.
3.1
Leaks in the vacuum pipes or monitoring and control gear.
3.2
Insufficient lubrication: add oil; or filter clogged.
3.3
Pump too hot.
3.4
Air being taken in at automatic trap (impurities, etc.).
4 – Vacuum pump
overheating.
4.1
Room too small, poorly ventilated or room temperature is too high.
4.2
Insufficient distance between the wall and the pump fan.
4.3
Unsuitable oil.
4.4
Temperature of sucked in gas is too high.
4.5
Start of clogging of the separating filter.
4.6
Exhaust line cross-sectional area too small.
4.7
Poor lubrication: add oil; or oil filter clogged.
4.8
Clean oil cooler (only E200 & E300 vacuum pumps)
5 – Vacuum pump emits
fumes at exhaust, or oil
consumption is high.
5.1
Separating cartridge incorrectly installed.
5.2
Separating cartridge broken or burst.
5.3
Automatic trap for re-injecting oil is blocked or its float is filled with oil.
5.4
Oil filler cap not properly tightened.
5.5
Vacuum pump overheating.
5.6
Unsuitable oil.
6 – Oil backs up by suction
to vacuum chamber
6.1
Non-return valve faulty.
6.2
Motor running in reverse
7 – Abnormal noises
7.1
Pump makes clicking noise: vanes worn or deformed.
7.2
Metallic noises: fan is touching another part or the cover is touching a lubrication pipe.
7.3
Oil viscosity too high or oil too cold.
8 – Presence of water in
the oil
8.1
Pump is sucking up fluids: trap fluids upstream of pump.
8.2
Open the gas ballast system.
8.3
Pump temperature too low due either to insufficient operating time or because room is too
cold: install a preheating and rinsing system. Consult us for this.
8.4
Exhaust channelled and condensates returning into the pump: install a low point trap.
SAFETY DATA SHEET
5.
See Annex
EC CONFORMITY DECLARATION
6.
The EC conformity declaration can be found at the end of this document.