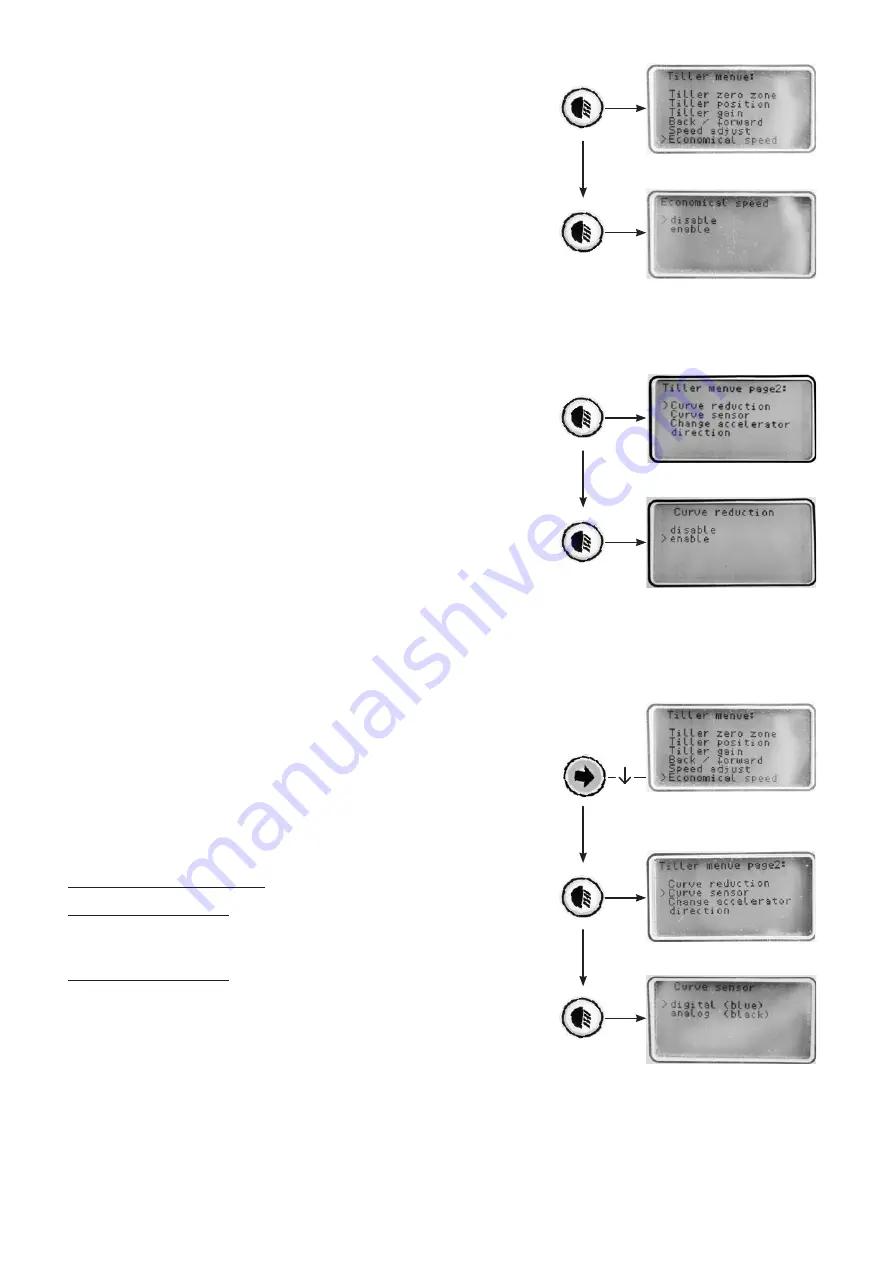
68
Economical speed
Here you can activate or deactivate the cruise con-
trol.
Curve reduction
Here you can activate or deactivate the speed re-
duction in curves.
☞
While driving in curves the speed is reduced to
about 7.5 km/h.
☞
When the final speed is set to 6 km/h a curve
speed setting is not possible.
Curve sensor
This setting adjusts the existing curve sensor. The
curve sensor is located behind the headlight.
☞
With an incorrect selection of the curve sensor
this function is not or incorrectly processed.
Curve sensor digital (blue) for Cityliner:
Model 3.263 / 3.264 and
Model 2.663 / 2.664
Curve sensor analogue (black) for Ortocar:
Model 2.563 / 2.564
Summary of Contents for 1.163
Page 2: ...2...
Page 8: ...8 OVERVIEW Cityliner 306 model 1 163 Cityliner 408 model 3 264 Cityliner 406 model 3 264...
Page 9: ...9 Cityliner 310 model 1 363 Cityliner 410 model 1 364...
Page 10: ...10 Cityliner 312 model 2 363 Cityliner 412 model 2 364...
Page 11: ...11 Cityliner 315 model 2 663 Cityliner 415 model 2 664...
Page 12: ...12 Ortocar 315 SP II model 2 563 Ortocar 415 SP II model 2 564...
Page 78: ...78 NOTES...
Page 79: ...79 NOTES...