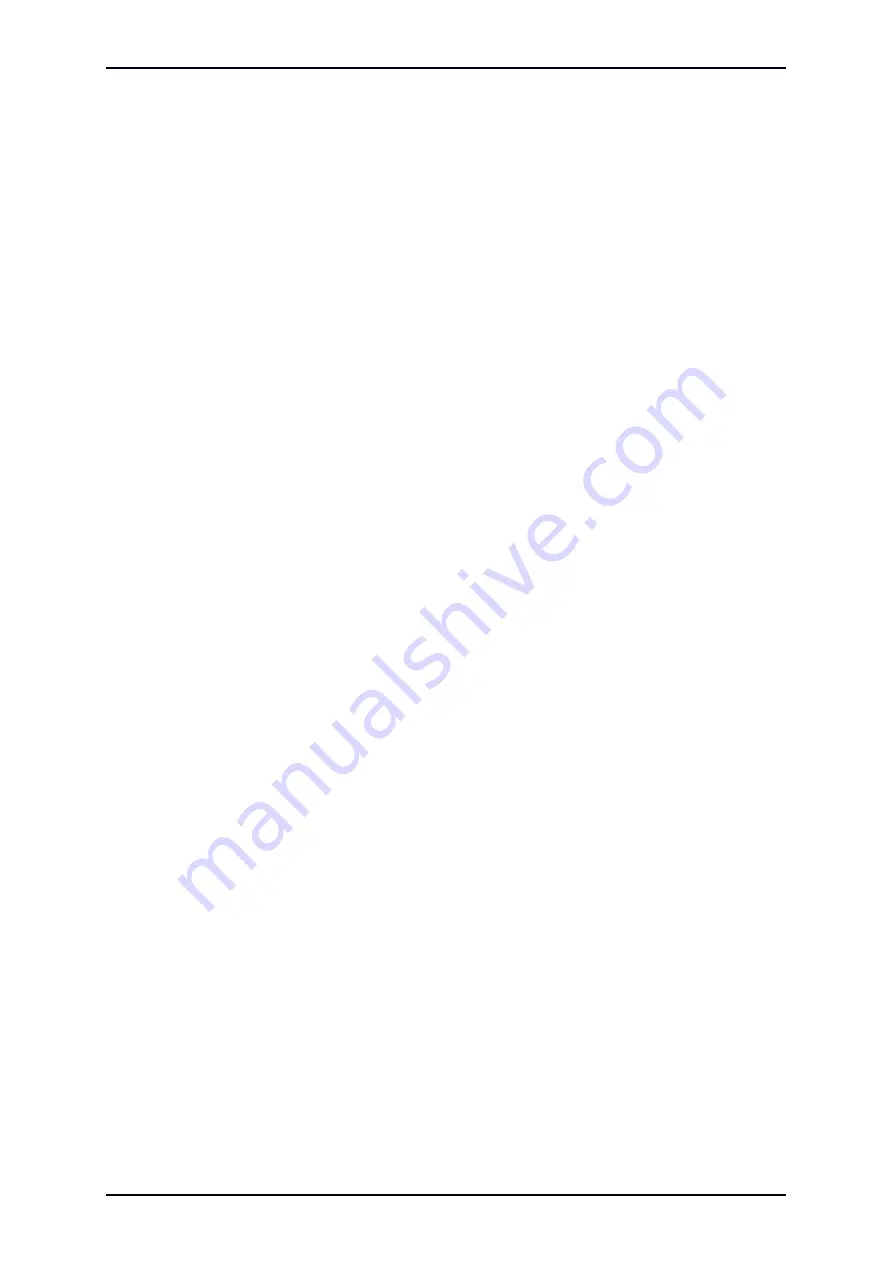
Page 60
5.3 Positioning mode
5.3.1 Overview
In positioning mode a certain position is set, which is to be approached by the motor. The current
position is derived from the information provided by the internal encoder evaluation. The position
deviation is processed in the position controller and is passed on to the speed controller.
The integrated positioning control allows jerk-limited or time-optimal positioning relative or absolute to
a point of reference. It provides the position controller and - to improve the dynamics - the speed
controller also, with the set points.
In the case of absolute positioning a set target position is directly approached. In the case of relative
positioning a parameterised route is run.
The positioning control is parameterised via a target table with 256 entries and additional positioning
sets, which are reserved for the communication interfaces (fieldbuses). The setting options for each
positioning set (see below) are freely parameterisable. The only thing to do for positioning is then to
select an entry and start the action. Optionally, it is possible to adjust the number of the required
positioning set via the digital inputs. For coding the positioning set number, up to 8 digital inputs can
be used (2
8
possibilities
256 positioning sets).
The following settings are possible for all positioning sets:
Target position
Driving speed
Final speed
Acceleration
Deceleration
Torque feed forward
Remaining distance trigger
Additional flags, these are in detail:
Relative / relative to last target / absolute
Wait for end / interrupt / ignore start
Synchronized
Rotary axis
Option: automatic deceleration in case of missing following positioning
Different options on the setup of path programs
The positioning sets can be activated via all bus systems or via the parameterisation software
Metronix ServoCommander
®
. The positioning process can be controlled via digital inputs.
Product Manual „Servo drives ARS 2100 SE“
Version 5.0