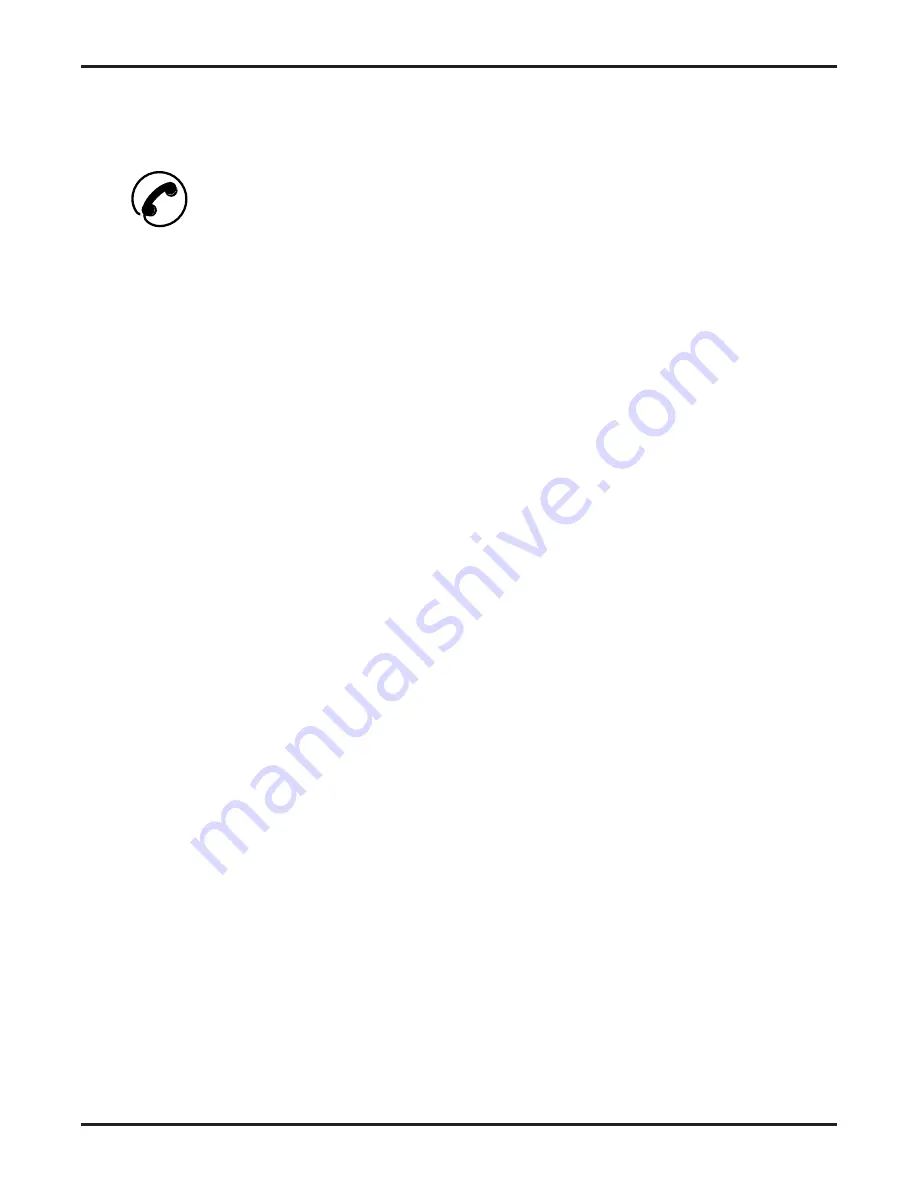
Troubleshooting
69
• For Technical Assistance call + 215-674-1234
• FAX: + 215-443-5117,
• E-mail: [email protected]
Please provide the following information:
• Instrument Model and Serial Numbers
• Sensing Element Model Number and Length
• Material being measured
• Temperature
• Pressure
• Agitation
• Brief description of the problem
• Checkout procedures performed and results
Trained field service engineers are available on a time-plus-
expense basis to assist in start-ups, diagnosing difficult
application problems, or in-plant training of personnel. Contact
the service department for further details.
Periodically, AMETEK Drexelbrook instrument training seminars
for customers are held at the factory. These sessions are guided
by Drexelbrook engineers and specialists, and provide detailed
information on all aspects of level measurement, including theory
and practice of instrument operation. For more information
about these valuable workshops, write to AMETEK Drexelbrook,
attention: Communications/ Training Group, or call 215-
674-1234.
Any equipment being returned for evaluation or credit must be
pre-approved by the factory.
In many applications, sensing elements are exposed to hazardous
materials.
• OSHA mandates that our employees be informed and
protected from hazardous chemicals.
• Material Safety Data Sheets (MSDS) listing the
hazardous materials to which the sensing element has
been exposed MUST accompany any repair.
• It is your responsibility to fully disclose all chemicals
and decontaminate the sensing element.
Summary of Contents for DREXELBROOK Universal IV Lite
Page 4: ...This page has no content...
Page 56: ...Section 4...
Page 67: ...Troubleshooting 61 Table 5 1 Problem Symptom Chart...
Page 78: ......
Page 80: ......
Page 85: ...Control Drawings 79 8 1 ATEX IECEX Section 8 Control Drawings...
Page 86: ...Universal IV Installation and Operating Instructions 80 8 1 ATEX IECEX Continued...
Page 87: ...Control Drawings 81 8 1 ATEX IECEX Continued...
Page 88: ...Universal IV Installation and Operating Instructions 82 8 1 ATEX IECEX Continued...
Page 89: ...Control Drawings 83 8 1 ATEX IECEX Continued...
Page 90: ...Universal IV Installation and Operating Instructions 84 8 1 ATEX IECEX Continued...
Page 91: ...Control Drawings 85 8 1 ATEX IECEX Continued...
Page 92: ...Universal IV Installation and Operating Instructions 86 8 1 ATEX IECEX Continued...
Page 93: ...Control Drawings 87 8 2 FM US FMC...
Page 94: ...Universal IV Installation and Operating Instructions 88 8 2 FM US FMC Continued...
Page 95: ...Control Drawings 89 8 2 FM US FMC Continued...
Page 96: ...Universal IV Installation and Operating Instructions 90 8 2 FM US FMC Continued...
Page 97: ...Control Drawings 91 8 2 FM US FMC Continued...
Page 98: ...Universal IV Installation and Operating Instructions 92 8 2 FM US FMC Continued...
Page 99: ...Control Drawings 93 8 2 FM US FMC Continued...
Page 100: ...Universal IV Installation and Operating Instructions 94 8 2 FM US FMC Continued...
Page 101: ...Control Drawings 95 8 2 FM US FMC Continued...
Page 102: ...Universal IV Installation and Operating Instructions 96 8 2 FM US FMC Continued...
Page 103: ...Control Drawings 97 8 2 FM US FMC Continued...
Page 104: ...Universal IV Installation and Operating Instructions 98 8 2 FM US FMC Continued...
Page 105: ...Control Drawings 99 8 2 FM US FMC Continued...
Page 106: ...Universal IV Installation and Operating Instructions 100 8 2 FM US FMC Continued...
Page 107: ...Control Drawings 101 8 2 FM US FMC Continued...
Page 108: ...Universal IV Installation and Operating Instructions 102 8 2 FM US FMC Continued...