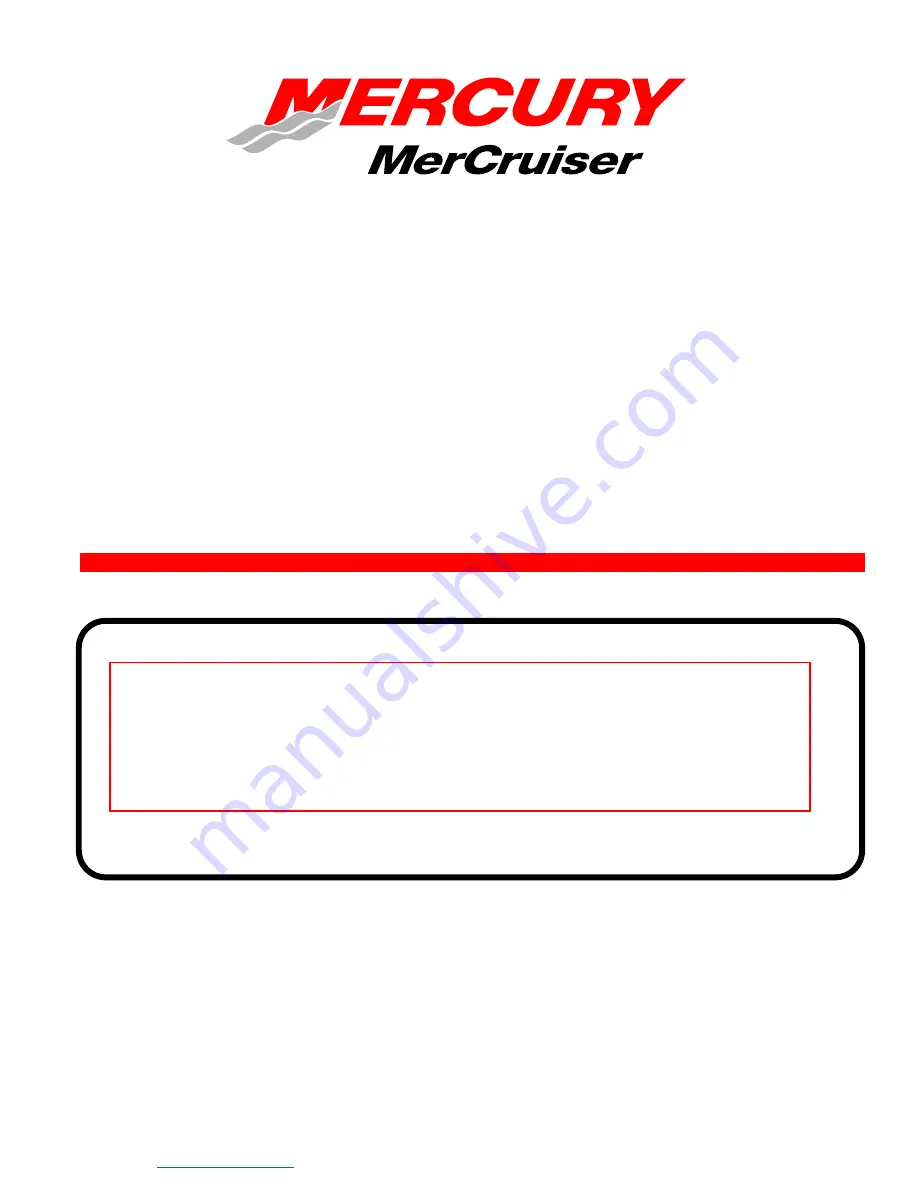
Number 23
Printed in U.S.A.
90-861326--1 MARCH 1999
1999, Mercury Marine
GM V8 454 cid (7.4L) / 502 cid (8.2L)
Book 1 of 2
Sections 1 thru 4
Downloaded from
https://needmanual.com/
MAIN MENU